Terex Ecotec and Ecohog to support creation of high-spec woodchips for biomass operation
Warwick Ward scoops landmark deal with Stobart Biomass Products
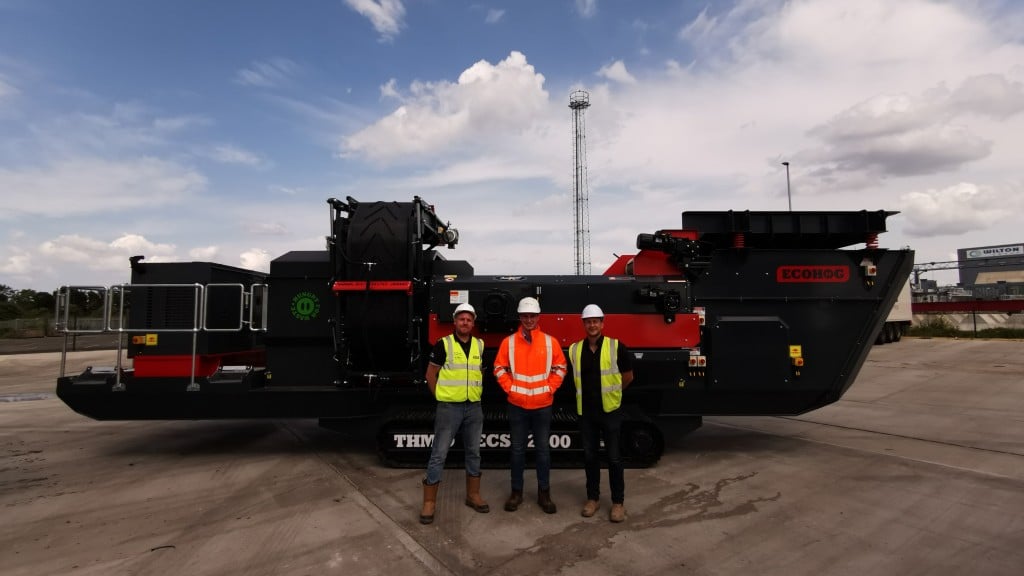
Waste recycling equipment supplier Warwick Ward recently signed a landmark deal that sees its Terex Ecotec and Ecohog products supporting a new biomass production process for Stobart Biomass Products Ltd.
Stobart Biomass Products is the UK's number one supplier of biomass fuel, with long-term contracts in place to supply 2 million tonnes of fuel to Energy Recovery Facilities, generating renewable energy equivalent to the annual domestic electricity needs of 2% of the UK population.
The company wanted to produce a high quality biomass wood chip with target specs, such as minimum fines and oversize. Warwick Ward demonstrated how Terex Ecotec's TDS 820 Slow Speed Shredder, TDS V20 Medium Speed Shredder and Ecohog's THM ECS-2000 Metal Separator worked together, achieving Stobart's required specifications and producing a high consistent through-put, with a more uniformed product achieved so that the biomass burners could get maximum efficiency out of their woodchip.
Mark McGlinn, Territory Sales Manager, Terex Ecotec said, "With such a tight specification to meet, Stobart were attracted to the TDS V20's unique ability to produce a high quality biomass product with minimal fines and oversize, without compromising on through-put. Its intelligent contaminant protection air-bag system also provides the confidence that no major damage will be caused should a foreign object slip through the net. Coupling up with the versatile and highly efficient TDS 820 pre-shredder gives their operators familiarity, using the same simple, easy to navigate control system on both machines."
These features, together with health and safety benefits gained from ease of maintenance and serviceability across all three machines, has resulted in Warwick Ward's solution taking Stobart forward in their biomass production. The mobile line has been set up across two sites, Port Clarence site (Middlesbrough) and Widnes site (Liverpool).
Aaron Whitrow, National Site Manager, Stobarts Biomass Products said, "Warwick Ward worked closely with us to create a mutually beneficial equipment and service level package that meets our specific needs. This included guaranteed through-put, a dedicated engineer, high level of internal training and on-site consignment stock. Producing high quality fuel that meets our customers' specification is of the upmost importance to us, so we needed a solution that could achieve this whilst reducing running costs across the whole process. We're delighted to identify significant savings using the Terex Ecotec and Ecohog set up, compared to our previous outgoings in wear parts and machine running costs per tonne."
James Tunnicliffe, Recycling Sales Manager, Warwick Ward said, "Following the machine trials - attended by representatives from Warwick Ward, Terex Ecotec and Ecohog, we took members of the Stobarts Group to Northern Ireland for a factory tour of Ecohog and Terex Ecotec, which also included a tour of Terex's multi-million-pound parts factory. Having seen the machines in operation on their site and then visiting the manufacturers, Stobart's were extremely impressed with these facilities, and we completed the deal in June 2019, consisting of all six machines and a three-year service contract plan across all machines.
‘'The day we got the signature on the order form was a fantastic milestone for Warwick Ward. We knew the machines were capable of achieving the targets required after already having both Terex Ecotec and Ecohog products in other blue-chip companies. I believe this shows confidence, not only within Warwick Ward, but also the manufacturers, to prove our concept worked, and would work well going forward in the biomass industry. It's been a pleasure to build such a great relationship with Stobarts."
Tony Devlin, Business Line Director for Terex Ecotec said, "Having Stobarts as a customer has shown the strides Warwick Ward have made since becoming a dealer for Terex Ecotec just over three years ago. We're privileged to be part of this prestigious set up at Stobarts—it is a clear demonstration to the burgeoning biomass industry that we can provide specific solutions to achieve desired results, and just as importantly, the resources needed to back it up."
Tristam Hubbard-Miles, Global Sales Director for Ecohog said, "Ecohog are delighted to have worked with Warwick Ward to secure another high profile Biomass processor contract in the UK. Our THM ECS-2000 is a well-established solution to adding value to the process by recovering valuable non-ferrous and ferrous metals, and other contaminants whilst also removing them from the biomass to protect the downstream boilers. We have no doubt the overall mobile solution chosen by Stobarts will enable them to achieve ultimate efficiency and production output whilst ensuring onsite flexibility and safety. We look forward to supporting the ongoing relationship between Warwick Ward and Stobarts in the future."
Company info
22 Whittier Street
Newton, NH
US, 03858
Website:
terex.com/ecotec
Phone number:
603-382-0556