Scrap tires for TDF: Tire Derived Fuel remains primary market for scrap tires
Alternative fuels is the largest application for scrap tires for good reason
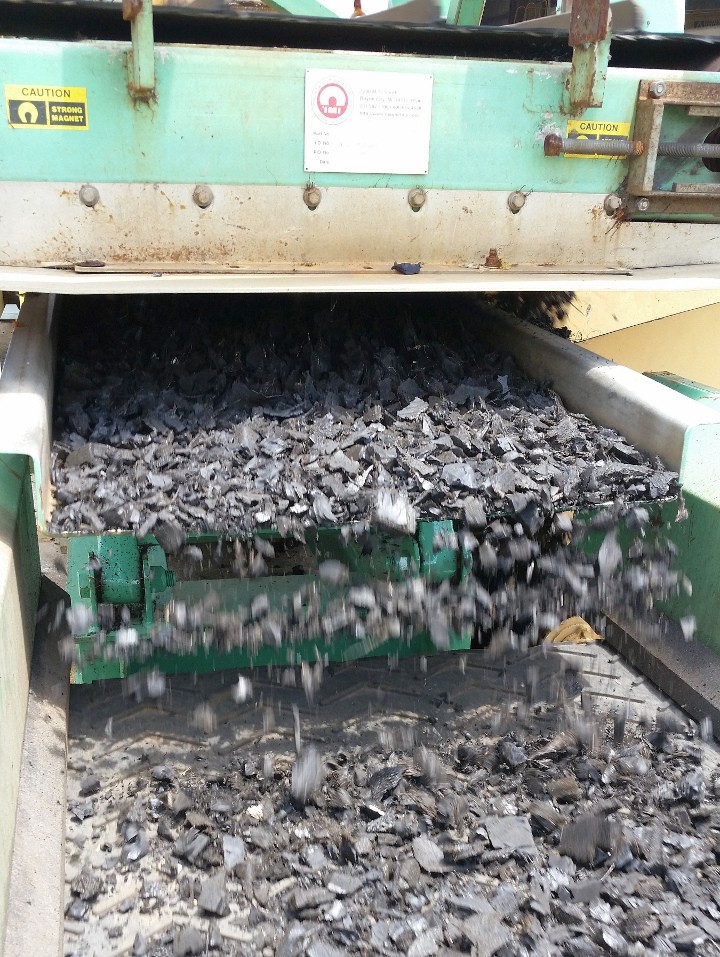
More than three decades into the tire recycling movement, the largest application for scrap tires remains the alternative fuels market. This is for good reason, as scrap tires are a tremendous resource of energy and iron. Major industries consuming tire-derived fuel (TDF) include cement producers, paper mills and energy utilities.
To produce TDF, tires are first shredded into small chips. For cement plants, the steel is retained in the chips as it serves a useful purpose in the production of cement, reducing the volume of iron ore needed for addition into the mixture. For other fuel markets, the preference (or requirement) is for a smaller low-steel-content tire chip, since steel content can be detrimental, by reducing the energy value of TDF and causing havoc with the feed grates in the combustion unit.
While TDF does not fit the traditional idea of what a biofuel is, by definition biofuels can come from "domestic and/or industrial wastes."
Numerous government and environmental studies from around the world have substantiated the energy benefits achieved with tire-derived fuel, while confirming emission levels comparable to other fossil fuels. Countries that are considered the model for environmental responsibility, such as Sweden, endorse, support and encourage the use of TDF.
In April 2005, the U.S. EPA published the following statement: "Based on over 15 years of experience with more than 80 individual facilities, EPA recognizes that the use of tire-derived fuels is a viable alternative to the use of fossil fuels."
For cement plants, TDF provides an alternative fuel at a competitive cost compared to traditional fossil fuels. TDF has a higher thermal value than most forms of coal, while also containing around 15 percent iron content in the form of tire wire.
TDF is supplied as a chip, achieved by shredding, grinding and screening, until meeting the required size, which is usually around 2 inches. In some cases, whole tires can be supplied to TDF producers, though there tends to be strict size requirements involved which eliminates the viability of many tires for this method of supply.
For traditional energy customers, TDF with very low steel content is preferred. This is achieved through additional stages of shredding or grinding and by using magnets to separate the wire. This results in a fuel product with energy value around 14,000 BTU/ pound, about 40 percent higher than TDF with wire content.
Industry has responded to the need for higher volumes of low-steel TDF by introducing high-capacity grinders which achieve steel separation much more efficiently than previously achieved simply by shredding. This increased capacity is helping to meet a demand that far exceeds supply in much of North America.
Most scrap tire processors, given the choice, would much rather convert scrap tires into granulate and powder, yielding a far better return on their investment.
However, the reality is that there is inadequate market demand for these granulates compared to the volume of scrap tires generated, necessitating the need in most regions to move more than 50 percent of tire volume into TDF markets. It is not simply a case of "producing the granulates and consumers will come."
One only needs to look at the province of Ontario, where there are no established markets or incentives to produce TDF. All program tires are converted to granulate, which has vastly oversupplied provincial needs, resulting in material travelling south into the U.S. where granulate oversupply and depressed prices impact tire processors in the Northeast, Great Lakes region, and areas much further south. Without TDF markets, many processors would struggle to survive.
By establishing a large alternative fuel demand for TDF, scrap tires get diverted from dangerous tire piles and are kept out of landfills, while allowing processors the opportunity to make substantial investments in TDF and granulate-producing machinery.
This article was provided by Granutech-Saturn Systems, and was originally published in the July/August edition of Recycling Product News, Volume 26, Number 5.