Machinex and Canada Fibers partnership to result in two of the most technologically advanced single-stream facilities in North America
Collaborating on the future of automated recycling
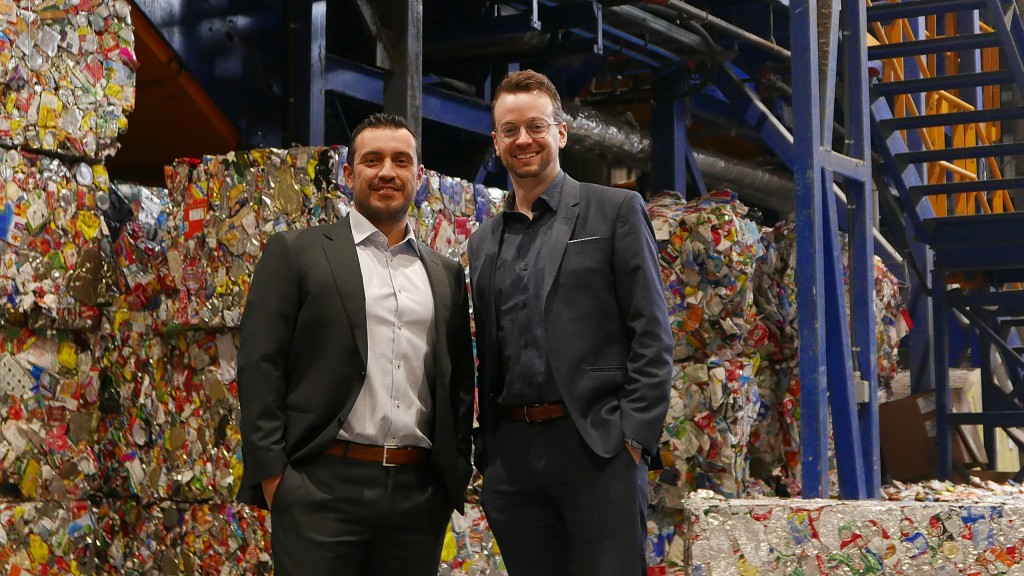
Toronto-based Canada Fibers Ltd. (CFL) is building two single-stream recycling facilities in 2019 that will include the most advanced, high-tech fibre and plastics sorting and recovery systems in Canada. In Winnipeg, Manitoba, a completely new 30-tonnes-per-hour facility (approximately 80,000 square feet) is currently under construction and scheduled to open in the fall. In the Region of Peel, Ontario, the existing Peel Integrated Waste Management Facility MRF, owned by the Region, will be retrofitted for 31.5-tonnes-per-hour capacity, with the updated facility (approximately 85,000 square feet) scheduled to open in the first quarter of 2020.
Canada Fibers' design, build and startup partner for both plants, Quebec-based Machinex, is currently in the process of manufacturing nearly 100 percent of the new system components, including seven optical sorters and a SamurAI artificially intelligent robot that will be installed in Winnipeg, as well as 10 new optical units for Peel. In total, through both plants, there will also be two kilometres of conveyors and almost three quarters of a million pounds of steel structure on the ground by the time installation is finished.
"We have a very long history with Canada Fibers," says Jonathan Ménard, executive vice president of Sales and Strategic Positioning at Machinex. "We have worked with CFL for more than two decades through various projects and are delighted we could connect on these two projects knowing they fit nicely into our business development strategy and align with our continuous desire to implement new sorting technologies and techniques."
According to Stephen Miranda, Canada Fibers' vice president, Material Sales and Operations, the Winnipeg facility and Peel retrofit will bring different successes to the company. "In Peel, the upgrade that the Region is investing in, and which CFL and Machinex are collaborating on, represents the faith that the Region has put in Canada Fibers' experience and expertise in maintaining and operating material recovery facilities in the province of Ontario," he says. "In Winnipeg, this will be CFL's first MRF outside of Ontario and represents our growth path as we continue to look for good partners and exciting opportunities. This facility will also boast one of the first robotic sorters in the country.
"Using more optical and robotic technologies, as we are in both facilities, aligns with the interests of Canada Fibers," Miranda continues. "Specifically, as the dimensions of different fibre grades alter, so too must the approach of separating them from one another for maximum value."
Miranda says part of the reason Canada Fibers chose Machinex for the two projects, scheduled for startup so close together, is because they wanted a single partner that could deliver both plants, from design to manufacturing to startup in a quite aggressive time-frame without sacrificing quality.
The geographical proximity of Machinex to these projects will also assure maximized flexibility and response time on all aspects of the projects' phases.
Tale of two facilities
While Canada Fibers has very similar performance expectations for both facilities, and there will be many similarities, there will also be significant differences.
"Both facilities will have complete emphasis on recovering products from single-stream recyclable materials to an unprecedented level, while yielding high purity in all of the recovered products," explains Miranda.
"In Winnipeg, however, we will have a little more operational flexibility to adjust to market demands, working in partnership with the City of Winnipeg, as they have also entrusted CFL with the responsibility of marketing all of their recyclable material. This will allow us to explore process changes that may ultimately yield higher revenues based on minor modifications to the recovered product."
One of the key similarities between the two plants is the use of what Jonathan Ménard calls a two-stage newspaper optical unit setup. He explains that the newspaper stream will be extracted and purified by Machinex' latest optical sorting units, arranged in a cascade formation.
"What this means is that either CFL can focus on what they want to keep, which is the newspaper, and positively eject material, or they can focus on the contamination any time they want in any configuration, negatively ejecting undesired materials," says Ménard.
From a design standpoint, there are definitely unique aspects to each project. "There were a set of parameters in Winnipeg which were different from Peel," explains Ménard. "Winnipeg is a smaller facility being built from the ground up. It's a single line, with 30-tonnes-per-hour capacity, using the widest equipment in Machinex' product portfolio, but less units. For example, the OCC screen is a combined 4-deck OCC/scalping unit to maximize the use of the available space and to keep the operation as lean as possible. We also use optical units up to 3.2 metres wide (which are the widest units available on the market) and only one ballistic separator, a larger model with 10 paddles."
The Winnipeg facility will be able to process approximately 100,000 tonnes of material yearly and will also be equipped with a state-of-the-art education room, allowing a view of the system from an integrated platform and video feed. The Peel facility - with capacity up to approximately 115,000 tonnes of material yearly - is an upgrade or retrofit of a currently operating MRF. As such, it includes a major dismantling phase of redundant equipment, and the complete conversion to a near-100-percent Machinex system makes it extra exciting, according to Ménard.
"It is clearly one of the most ambitious retrofit projects in our company history," he says. "Peel will have one of the most high-tech, advanced paper sorting systems in North America, including the 10 new optical sorters, with positive or negative ejection patterns on the newspaper and numerous other steps of fibre recovery," continues Ménard. "There will also be a recovery optical unit at the end of the process to maximize the overall recovery of all types of recyclable products."
The SamurAI robotic sorter
As a key part of the Winnipeg system design, Machinex will implement its SamurAI robotic technology, using artificial intelligence (AI) developed in partnership with AMP Robotics. Featuring a unique four-articulation robot, the SamurAI robotic sorter employs AI technology to identify materials for accurate, positive product recovery or as a precise quality control function.
The AI operates according to a predetermined order of task hierarchy to maximize financial return while continually improving and learning from operating experience to assure maximum recognition efficiency. Compared to a human sorter, who achieves an average of 35 to 40 picks per minute, Machinex says the SamurAI manages to almost double this average by reaching 60 to 70 picks per minute.
According to Ghislain Thivierge, specialist in robot cells integration at Machinex, a key standout feature of the SamurAI is the power of its gripping tool. "We pushed its development to obtain a very powerful suction tool that offers an excellent rate of success in gripping," explains Thivierge.
"The force of the suction lifts the containers while minimizing the movement of the surrounding material on the belt. The combination of this phenomenon and a success rate of 60 to 70 manipulations per minute give the equipment very satisfactory results. Our current experience shows us that the SamurAI performs very well in grabbing the most difficult containers like large HDPE that have irregular shapes."
"It's another great example of how Canada Fibers wants to be ahead of the curve," adds Ménard. "They have a great interest in robotics. After consultation regarding the Winnipeg project, Machinex and Canada Fibers determined that the best way to get maximized results using the SamurAI technology would be on their HDPE QC line."
Flexibility in design for changing markets
According to Ménard, Canada Fibers definitely has a unique way of looking at MRF design. "Knowing that they have a unique way of operating a MRF, and they also have proven their ability to maximize their performance, it allows us as a plant builder to be more innovative. We know that through CFL's experience they will be able to manage the innovation effectively.
"Both companies share the value of how a MRF should be designed and how it should perform." Miranda adds that CFL and Machinex spent many hours planning and discussing the design and process flow of both facilities. "One thing was always evident," he says. "Someone would ask: ‘what happens if. . .' so we spent a lot of time addressing these kinds of questions. We have come up with designs that give both systems the flexibility to perform and maximize values of recovered products given current compositions, and adjust to new demands of domestic and international fibre end markets."
For Ménard, at both of the new facilities, designing in flexibility to adapt to changing market conditions was paramount. In Winnipeg, CFL was tasked to plan for numerous specific future-proofing options.
"There's space for it, it's planned in the design, and we know where it's going to fit," says Ménard. "Any modernization will be focused to maintain or increase the general efficiency of the plant in terms of recyclable recovery or purity. We know which parts of the system are going to be upgraded. It's how we design. We think about how the system can evolve."
Miranda notes that for many years CFL has embraced the increased demands of recycling end markets. Their approach of implementing annual capital upgrades in its facilities has allowed the company to cope with changing material streams, and to process and effectively market fibre products both domestically and internationally, without disruption during times of market volatility. At their approximately 140,000-square-foot Toronto MRF, this has been proven. Since the facility opened in 2013, CFL has spent an additional 15 million dollars in upgrades, ensuring their recovery system remains just as efficient and on par with new, leading systems.
"We have a new upgrade planned for this facility as well that will include three new opticals, and the exciting addition of three robots," Miranda says. "This adds to the 13 optical units which are currently in the facility.
"We continue to respond to the rapidly changing environment and material streams, ensuring the facilities we operate are at the cutting edge of technology," Miranda continues. "This allows our customers to continue to look to our organization as an example of a responsible leader in the industry."
He adds that their two current projects are in line with this strategic approach to recovery. "We are very pleased to work with such partners as the Region of Peel and the City of Winnipeg, who also realize the necessity of keeping up with the demands of the recycling industry, and have entrusted CFL with the responsibility to advance their programs," he says.
"It has also been a pleasure working with Machinex on these projects as they have truly accepted and implemented Canada Fibers' vision, while adding their own progressive concepts," says Miranda. "It has been a very good, collaborative approach on the evolution of sorting technologies." RPN
This article was originally published in the January/February 2019 edition of Recycling Product News, Volume 27, Number 1.
Flexibility in design for changing markets
According to Ménard, Canada Fibers definitely has a unique way of looking at MRF design. "Knowing that they have a unique way of operating a MRF, and they also have proven their ability to maximize their performance, it allows us as a plant builder to be more innovative. We know that through CFL's experience they will be able to manage the innovation effectively.
"Both companies share the value of how a MRF should be designed and how it should perform." Miranda adds that CFL and Machinex spent many hours planning and discussing the design and process flow of both facilities. "One thing was always evident," he says. "Someone would ask: ‘what happens if. . .' so we spent a lot of time addressing these kinds of questions. We have come up with designs that give both systems the flexibility to perform and maximize values of recovered products given current compositions, and adjust to new demands of domestic and international fibre end markets."
For Ménard, at both of the new facilities, designing in flexibility to adapt to changing market conditions was paramount. In Winnipeg, CFL was tasked to plan for numerous specific future-proofing options.
"There's space for it, it's planned in the design, and we know where it's going to fit," says Ménard. "Any modernization will be focused to maintain or increase the general efficiency of the plant in terms of recyclable recovery or purity. We know which parts of the system are going to be upgraded. It's how we design. We think about how the system can evolve."
Miranda notes that for many years CFL has embraced the increased demands of recycling end markets. Their approach of implementing annual capital upgrades in its facilities has allowed the company to cope with changing material streams, and to process and effectively market fibre products both domestically and internationally, without disruption during times of market volatility. At their approximately 140,000-square-foot Toronto MRF, this has been proven. Since the facility opened in 2013, CFL has spent an additional 15 million dollars in upgrades, ensuring their recovery system remains just as efficient and on par with new, leading systems.
"We have a new upgrade planned for this facility as well that will include three new opticals, and the exciting addition of three robots," Miranda says. "This adds to the 13 optical units which are currently in the facility.
"We continue to respond to the rapidly changing environment and material streams, ensuring the facilities we operate are at the cutting edge of technology," Miranda continues. "This allows our customers to continue to look to our organization as an example of a responsible leader in the industry."
He adds that their two current projects are in line with this strategic approach to recovery. "We are very pleased to work with such partners as the Region of Peel and the City of Winnipeg, who also realize the necessity of keeping up with the demands of the recycling industry, and have entrusted CFL with the responsibility to advance their programs," he says.
"It has also been a pleasure working with Machinex on these projects as they have truly accepted and implemented Canada Fibers' vision, while adding their own progressive concepts," says Miranda. "It has been a very good, collaborative approach on the evolution of sorting technologies." RPN
This article was originally published in the January/February 2019 edition of Recycling Product News, Volume 27, Number 1.