Time to rethink what can be accomplished with catalytic converter recycling data
Auto catalyst reaches the data age
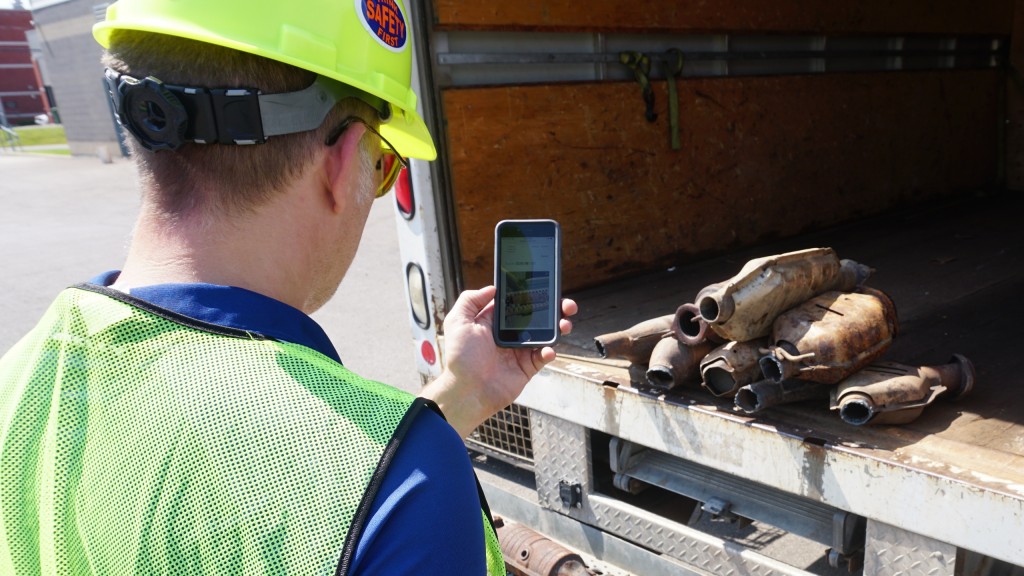
In the automotive recycling world there is endless data produced and studied by companies large and small. Being able to make sense of that data has been the preoccupation of business owners, managers and the people behind the creation of data for many years. With respect to recycled auto catalyst data, the focus has primarily been on the average value per unit. For those who are serious about data tracking and catalytic converter profits however, it's time to rethink what is possible to accomplish with data.
To look at how to begin with a new approach it is best to consider those that are the most successful in getting more from converter recycling. The best cases are the recyclers that have been able to perform separate assays of the various types of auto catalyst and have a long history of toll refining.
Five types of auto catalyst
There are five types of auto catalyst that should each be looked at differently.
1.) OEM Ceramic Converters
Original Equipment Manufacturer or the converter that was put on the vehicle from the factory. The base material of these converters is cordierite ceramic that has been wash-coated with precious group metals (PGM: platinum, palladium and rhodium.) These converters make up roughly 95 percent of all auto catalysts and have the highest precious metal loadings.
2.) OEM Metallic Converters
These converters are also original equipment from the manufacturer but have a different internal composition. The guts are made up of 409 stainless steel, also wash-coated with precious metals. They represent the other five percent (approximately) of converters in the marketplace and must be processed differently for recycling than ceramic cordierite units, but have similar precious metal loadings.
3.) DPF (Diesel Particulate Filter)
Currently, this material can be split into two categories. High-Grade that is worth the effort to recover the PGMs, and Low-Grade that costs more to recover the PGMs than the returns are worth. Also noteworthy is that many smelting facilities are having difficulty processing this material as the high silicone carbide content is causing issues with arc furnaces, resulting in extra fees for recycling.
4.) Aftermarkets
These converters are replacements for when the OEM Converter fails. The PGM loadings of aftermarkets are 90 percent less than OEM materials, but while the loadings of precious metals are one tenth of the OEM, they are made from the same cordierite ceramic base.
5.) Beads
These converters were the first on the market and were most commonly found on light-duty trucks. While there not that many left to recycle, they are typically processed separately as the loadings of precious metals are closer to aftermarket levels, offering an accurate assay value.
Until very recently it has been difficult for most auto catalyst recyclers to have enough volume of material to run each of these materials in separate assays. This is due to the fact that most refiners are set up to process 2,000-8,000 pound lot sizes. This has forced most auto catalyst recyclers to mix the various types of catalyst. While this has been an acceptable means of operation for payment, it is not the best way to track data or provide precise compensation for each of the converter types.
Getting into the Mix
First let's look at why processing a combination of materials fails on the compensation end. Toll refining as a whole is largely a mystery to many of the clients that use the service. One of those mysteries is how refiners arrive at the contained and recoverable precious metals value in a given lot. Most savvy customers know that the analysis is done by systematically sampling a lot, and using both XRF and ICP machines to determine the PGM contents.
What most do not fully understand is that both XRF and ICP machines need to have complex formulas to accurately read samples. The formulas have been developed over time to look for very specific elements contained in the five different types of catalyst, and the materials are very different from each other. As outlined in the descriptions of each type of catalyst above, some have a completely different base construction, while others have very different PGM loadings. If the substrates are mixed for assay, the laboratory machinery is delivering results based on improper scientific assumptions.
For example, for material with a mixture composed of primarily OEM Ceramic, but which has more than 20 percent aftermarket and some DPF, the reading will be tainted as the lab formula will only be reading for the regular auto catalyst cordierite ceramic base. There is no way for the machinery to register the DPF and its silicone-carbon base properly. Then, if the lower content readings on the aftermarket material are added, the results will skew lower. This practice is not uncommon in the industry and does not do any favours for the businesses selling auto catalyst material.It should also be noted that no supplier of recycled auto catalyst is paid on what comes out of a furnace, so an accurate pre-furnace assessment of the catalyst is vital.
While there is no way to say exactly how much loss is generated from mixing materials, we can say two very clear things about keeping materials separate. First, when performing an assay on like materials, auto catalyst labs are exceptionally accurate when identifying the recoverable PGM content of a given lot. And secondly, the data that is created by these separate material assays gives the automotive recycler a very clear picture as to the value of each material, so they can generate more profit and have better control of their inventory, both when acquiring converters and when selling.
On another very important side note, there needs to be special attention paid to DPF material. Since 2006 this material has been produced with a silicone-carbide additive or SiC. While this addition to the filters makes them run cleaner by trapping the carbon emissions from diesel fuel, it has created significant challenges in recycling the material.
The biggest challenge high carbon DPF poses to recovering precious metals is that the trapped carbon (if not treated properly) can ignite and cause an explosion in an arc furnace.Presently, smelting facilities are dealing with the problem, but must treat high carbon content DPF differently to avoid potential disaster. This new and growing issue has increased fees relating to the processing of DPF, and in some cases loads are being rejected outright by some catalyst smelting facilities.
Further, this problem will continue to become more and more evident as the increase of DPF, made after 2006, is just now fully entering the recycling stream. This, combined with the increased sales of diesel-fuelled light-duty trucks and passenger vehicles in the last 10 years, will put mounting pressure on the need to separate materials properly. Recyclers who have been mixing small amounts of DPF into regular auto catalyst will experience increased financial loss when their lots are charged additional fees for high carbon content or rejected outright by their processing partners due to increased carbon levels.Armed with this information, it is best to separate DPF right away to avoid losses and to increase profits.
Trained, knowledgeable staff
Another real challenge for recyclers dealing with catalyst materials is having the trained, knowledgeable staff on hand to do the sorting, especially if they are cutting converters and dealing directly with a smelter. If auto catalyst recyclers are not doing their own decanning they are relying on their processor to separate the materials. Currently there are very few processors in North America that process lot sizes small enough to guarantee the proper separations of materials.
If the lots do not contain enough ceramic weight to meet the minimum requirement of 2,000 to 8,000 pounds, many catalyst processors are mixing the lots. A common practice is to process aftermarket material with regular auto catalyst. While the base of the material (ceramic substrate) is the same, the precious metal loading is so different that it becomes difficult for an auto recycler to quantify the results. So what can be done by a business owner who relies on auto catalyst sales when there are so many challenges in getting the most accurate and reliable results for their material? The answer is simple. Find a processor that is able to assist you with the correct information to identify and separately assay the five different types of converter materials. Your bottom line will begin to look brighter as your company is able to interpret the data more precisely.
Smaller lots, better data Getting compensated more precisely for your converter material is always a good thing. Having the ability to track the consistency of results based on the type of catalyst material coming from multiple locations or departments is even better. However, the only way to accomplish this, for most companies, is to look for a converter processor that is able to offer assay results on small lots of converters.
This raises the question: "What defines a small lot of converters?"
Traditional converter processor/refiners have kept lot sizes to between 2,000 and 8,000 pounds of ceramic substrate, or roughly 1,000 to 4,000 automotive converters. As newer converter processing companies press the traditionalists there are now accurate assays being done on as few as 100 automotive converters or 200 pounds of ceramic. This is really changing the way data can be analyzed and managed. With a lot size of 100 converters, just about any size auto recycler can manage to separate each of the five different converters types, gaining access to better returns and better tracking of assay data. Companies that have multiple facilities can look at smaller lot data to make decisions with respect to the purchase of vehicles to recycle.
What is the competitive advantage? If the majority of companies are using converter processors that don't separate materials and blend the aftermarkets with small amounts of DPF, the inaccurate information could end up resulting in an average converter worth $60 U.S. In reality, the average OEM converter is worth closer to $80 or more, and the average high-grade DPF can be $150 or more - based on accurate sorting and count information from the converter purchaser/processor.
If working with a company that offers small lot assays of, for example, 100 converters, a supplier is able to turn material faster. Instead of waiting, sometimes months, to collect 1,000 or more converters, material can be shipped out much sooner and a company can insulate itself from PGM market changes. When you can separate all the various categories of converters in smaller lots, the data feedback will keep you one step ahead of your competitors and provide real control over this highly valuable inventory.
Separation of materials and small lot assays makes it much easier to spot data spikes that can act as profit/loss indicators. Furthermore if a company is also purchasing converter units across the scale and is not separating the lots between production converters and purchased material, there is an even bigger potential for lost profit. In the marketplace today there is a lot of information available regarding the value of converters. If a company doesn't have a ready source for that information it could be at risk for dumping of low-grade material. Partnering with a converter processor that is able to provide instant converter information feedback will end this practice and provide the opportunity to make converters a higher profit core.
This article was submitted by PMR, Inc. and was first published in the November/December 2018 edition of Recycling Product News, Volume 26, Number 8.