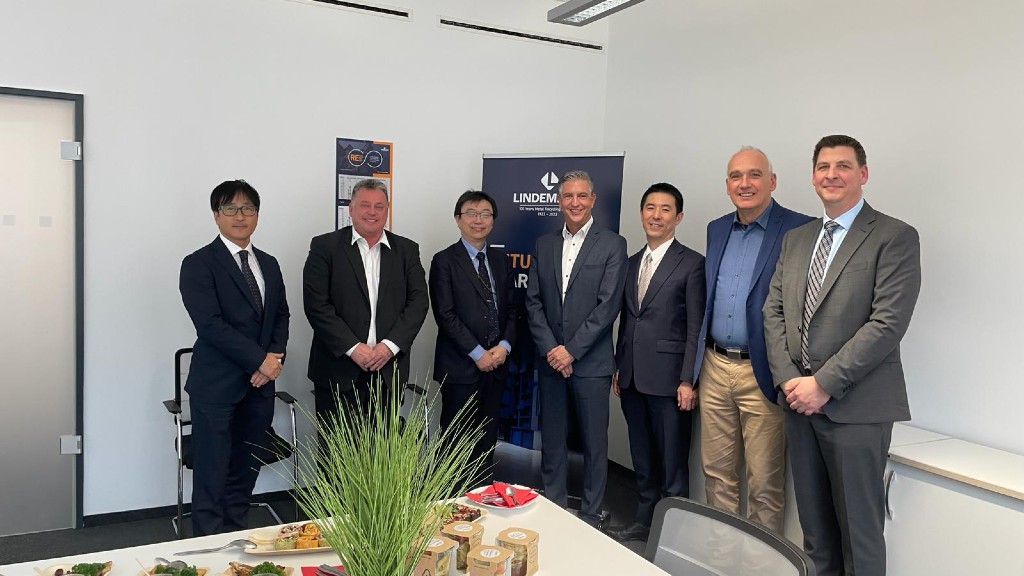
The partnership and collaboration between Lindemann Germany and Mitsubishi Electric has got off to a successful start. The companies say that it has set new standards in terms of intelligent drive solutions and control technology for sustainable metal recycling.
Innovation is needed given the current economic challenges facing the European metal recycling industry. Shredders and the associated downstream systems have high energy requirements. The integration of low-maintenance frequency inverters on three-phase asynchronous motors in existing systems opens up new possibilities. Retrofitting leads to massive savings in energy, wear, and maintenance costs, which increases productivity and availability.
Both companies have recognized this potential and are working together to open up the market. Several projects have already been successfully implemented.
"The partnership is a big win, not only for our two companies but for the entire industry," says Stefan Knauf, division manager of factory automation at Mitsubishi Electric.
"The enormous opportunities offered by the metal recycling market underline the importance of this collaboration," says Carl Gustaf Göransson, CEO of Lindemann.
This is because 45.8 percent of the almost 37 million tons of crude steel produced in Germany in 2022 were already made from recycled steel.