Increase profitability by processing Zurik to Zorba
How to transform a low-value material into a high-value and copper-rich product
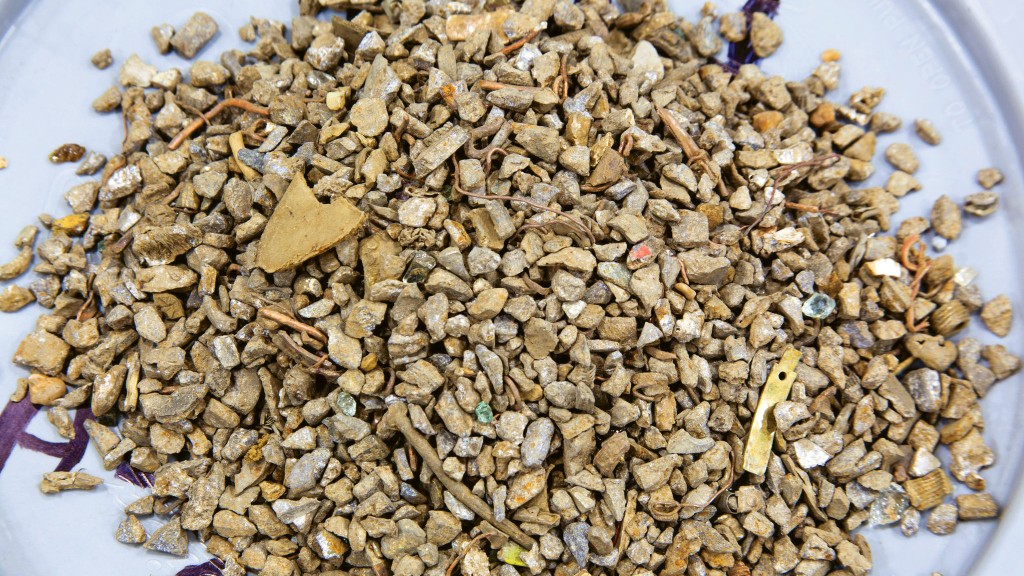
A recent white paper from Eriez highlights separation equipment that efficiently upgrades Zurik to a more desirable and profitable Zorba fraction while also reducing scrapyard fire hazards.
Zurik typically contains many co-mingled metals with a high concentration of non-ferrous metals, stainless steel, and debris. Zurik is also expensive to recover and has little value compared to other products produced at shredder yards. The generally poor grade of Zurik commands a relatively low price, as Zurik needs to be processed further to make a mill-ready product.
The challenges of processing Zurik
In addition to the high cost of recovery and low value of the product, stockpiles of Zurik also generate heat and are widely believed to be one of the main causes of fires in scrapyards due to the hot metals surrounded by flammable debris. For more than a decade, car shredding operations have used sensor-based sorting equipment to detect and reject stainless steel, circuit boards, and other metals missed by upstream eddy current systems from the final waste product before debris is sent to the landfill. This product is what is commonly referred to as Zurik.
The nature of Zurik is created when the sensor machines misplace a sizable percentage of debris along with the desired metal product. The result is a low-grade, co-mingled material which can be difficult to market. By using the Zurik to Zorba process, we can increase the value of the Zurik by transforming it into a high-grade Zorba product without debris.
Another significant advantage is that separating hot metal from the debris reduces the risk of fires originating in Zurik stockpiles.
The Zurik to Zorba process
The process of converting Zurik to Zorba begins with shredding the recovered Zurik down to -1/2 inch. There are multiple benefits of liberation, size reduction, and a smaller size distribution of the product.
First, making all the products close in size allows for better separation and recovery on magnetic separators and eddy current separators. Since the finer non-ferrous material can only "jump" a certain distance when in contact with the eddy current magnetic field, the splitter needs to be brought into a location where the non-ferrous material can be recovered, yet large enough for the largest non-conductive material to pass under.
Second, the size reduction liberates all of the co-mingled metals, specifically copper wires, from small motors and other objects that typically end up in the Zurik product. The additional free copper in the product and elimination of debris increases the value of a Zorba product.
Equipment utilized within the Zurik to Zorba process consists of a ring mill, a small drum-type magnetic separator, a high-frequency eddy current separator, and a stainless steel magnetic separator. The size reduction and liberation of Zurik is key to ensuring this process provides the highest return. Additionally, it has been determined that a ringmill shredder offers the best results for this process by providing a uniform size of -1/2 inch material. The liberation of this material at this size fraction ensures that ferrous and non-ferrous separation are of the highest recovery and grade once all material fractions are produced.
As the material has been liberated, a significant fraction of ferrous material is easily captured, producing a high-grade material. Due to the abrasiveness and quantity of ferrous products, a drum-type permanent magnetic separator is best suited. This self-cleaning, magnetically effective separator offers the highest recovery and grade of ferrous with minimal maintenance required and no downtime for manual cleaning.
Although the ferrous fraction is smaller in size, a professionally designed barium ferrite magnetic circuit provides the magnetic separation required for this process. The non-magnetic material fraction from the magnetic drum separator contains non-ferrous metals, weakly magnetic stainless steel, and residue. This material is introduced to an ultra-high-frequency eddy current separator. This separator is designed to operate with a high rotor speed, providing the quantity of pole changes necessary to repel the smallest conductive non-ferrous metals, including bare copper wire.
In this case, material down to 1 mm is introduced to the machine and repelled. The recovery and grade of the Zorba (+95 percent) produced by the ultra-high-frequency eddy current separator produces material that sells at a premium price. This material can only be produced utilizing the technology found in this type of eddy current separator. Standard eddy current separators are only capable of recovering material coarser in size due to less frequency changes found in this type of magnetic circuit design and the larger size distribution.
The last step of the process is to recover the liberated and weakly magnetic stainless steel fraction. When a non-magnetic stainless steel material is work hardened, such as when ground or shredded, it can become paramagnetic (weakly magnetic). A magnetic separator with an exceptionally high, specifically designed magnetic circuit can produce a clean stainless steel fraction because of the magnetic susceptibility of the material. This type of separator incorporates a vibratory feeder that transports the material onto a small conveyor with a highly wear-resistant belt. As the material reaches the end of the conveyor, a magnetic head pulley holds the stainless steel material to the belt as it continues around the end of the conveyor.
The non-magnetic fraction continues its normal trajectory, while the magnetic fraction is discharged as the belt peels away from the magnetic head pulley. The waste fraction from this separator is residue that can be disposed of with the automotive shredder residue produced in the non-ferrous process.
Overall, by processing Zurik into Zorba, a processor transforms difficult-to-market, low-value Zurik that generates fire hazards into a high-grade, highly sought-after, and copper-rich Zorba. This copper-rich Zorba commands a higher price than standard Zorba, while also creating a fine saleable stainless steel product.
Mike Shattuck is the recycling market manager at Eriez.