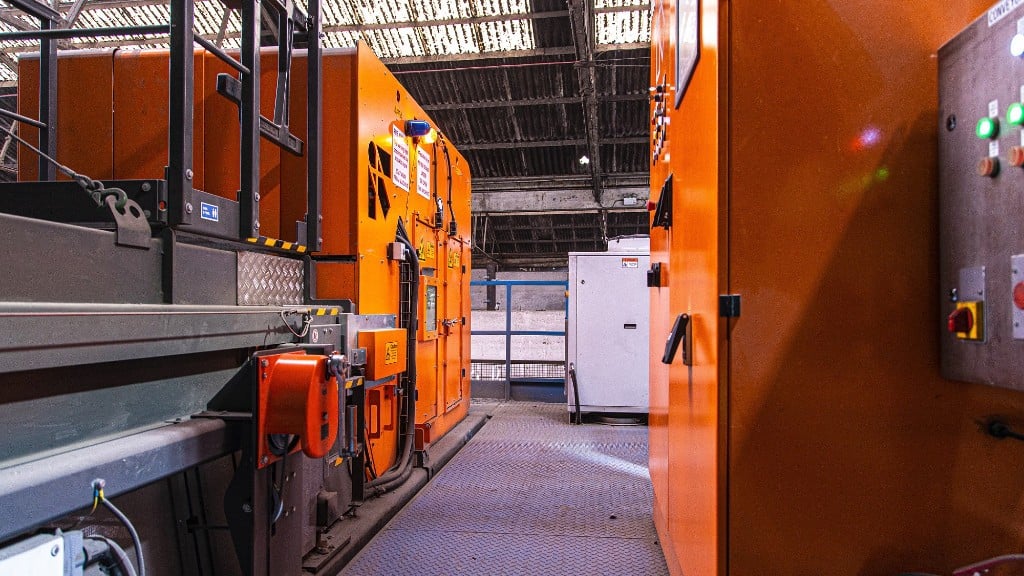
TOMRA Recycling has launched the next generation X-TRACT x-ray aluminum sorting machine with a new design and updated innovations. TOMRA's X-ray transmission (XRT) technology uses metal recovery technology.
The next-generation X-TRACT's capabilities and machine intelligence offer advancements in the high-throughput sorting of complex mixed metal streams to produce high purity, furnace-ready aluminum fractions. With a multitude of new and updated features, the next-generation X-TRACT helps with the production of circular metals.
Faster detection in metal recycling applications
The new X-TRACT features dual processing technology, which increases the machine's capacity per foot-width. Its simultaneous single object and area processing allows operators to choose between high purity and high recovery sorting. Even adjacent, overlapping, and composite materials can be identified and separated using data-driven decision-making.
The high-throughput sorting system features a next-generation DUOLINE XRT sensor with two independent line scans positioned close to the input material for high precision detection and faster processing. Due to its close proximity to the material, the sensor also effectively detects copper wires and ultra-thin objects to reduce material loss and maximize profits. Its new X-ray source offers variable power with up to 1000w supply for high-throughput processing of multiple applications and grain sizes, from large fractions to fine materials less than 0.20-in (5-mm) in size.
Updated capability and flexibility
The new X-TRACT is now capable of sorting with higher belt speeds ranging from 7.5 to 12.5 ft/s (2.3 to 3.8 m/s) to maximize throughput and yields at the same time. To accommodate the faster belt speeds and higher throughput, TOMRA designers extended the sorting chamber and added new extraction ports to remove dust and reduce air turbulence.
With improved image capturing, the new X-TRACT delivers ideal sorting accuracy, and its new intensity scale feature measures the relative thickness of objects. This eliminates the need for additional sensors and improves the detection of specific material groups like printed circuit boards.
While the previous generation of XRT metal sorting systems from TOMRA offered models that varied by application, the new X-TRACT is based on a modular machine concept. This gives operators the choice between high resolution or high sensitivity sensor systems and different valve blocks but also enables more operational flexibility and easy upgrades to minimize long-term capital expenditures.
Machine trials in a production environment produced 0.40- to 1.20-in (10- to 30-mm) sized aluminum fractions with 99 percent purity levels. Alutrade Ltd. was the first company to pilot the new X-TRACT and compare its results to the previous model.
"New X-TRACT gives recyclers and smelters opportunities to increase their revenues with high-purity aluminum fractions while lowering their carbon footprint and having enough material on hand to meet market demand," says Terence Keyworth, segment manager metals at TOMRA Recycling. "The automotive and construction sectors rely on recycled aluminum to lower their carbon footprint. It's a matter of being fast enough to supply the surging demand."
How the new X-TRACT sorting machine was designed
"When our in-house team set out to design a new generation of X-TRACT, it was absolutely clear that it should be sustainable, connected and built for long-term performance to reduce operational costs," says Matthias Winkler, product manager at TOMRA.
Developing a new machine to meet the future needs of the industry involved collaboration with customers, design engineers, aluminum processing experts, metal application specialists, and service teams.
To extend the lifetime of the machine, the designers added enhanced sensor shielding in addition to its top-mounted X-ray source to protect its most valuable components and provide extra stability. The new sorting system that separates aluminum from heavy metals and super lights in a single step. Plus, the machine comes with a 4-year extended warranty on the X-ray source and XRT sensor to meet standards and service levels.
"Our partners in the aluminum industry rely on the lowest downtimes and long-term performance," says Tom Jansen, segment manager of metals at TOMRA. "X-TRACT's new design makes it faster and safer for plant operators to replace parts due to normal wear and tear with as little downtime as possible."
The machine's new catcher hood allows for easier access for maintenance, whether performed by a service team or on-site staff that have been trained by TOMRA.
The new X-TRACT is also enabled for cloud-based monitoring, data-driven optimization tools, and remote access with the add-on TOMRA Insight service. With the ability to connect to the machine through online monitoring and digital services, TOMRA's service team can identify potential issues before they arise and provide remote support to ensure low downtimes.