Investing in wet processing is part of a sustainable future for C&D recycling
Harford Minerals is headed in a new direction following the addition of a multi-million-dollar CDE wet processing plant
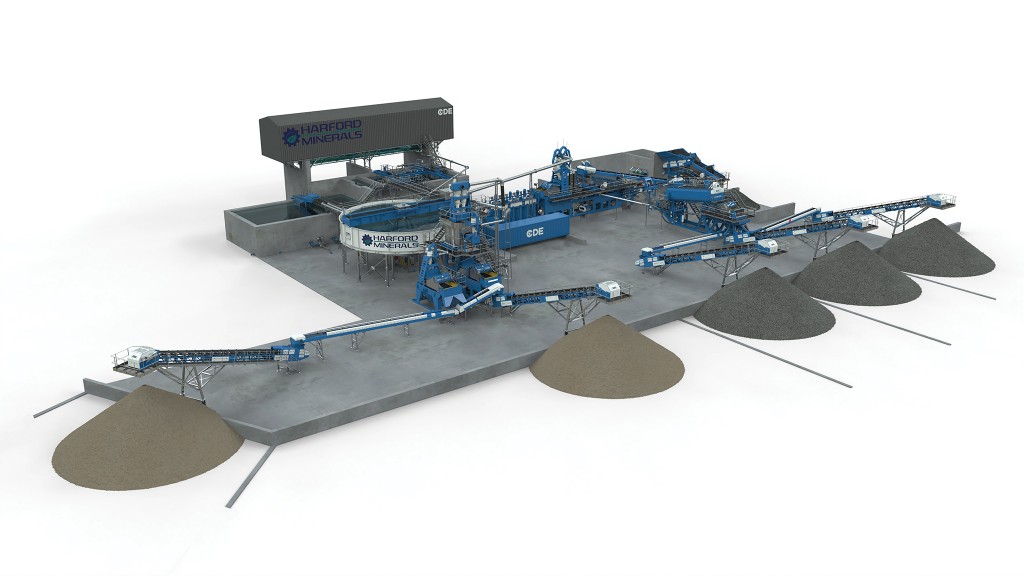
Harford Minerals, which operates a reclamation facility in Maryland, USA, has reinforced its commitment to sustainability and a full life cycle approach to materials usage with a multi-million-dollar investment in a new state-of-the-art wet processing plant from CDE Global, for construction, demolition and excavation (CD&E) waste, representing the largest single investment in the company's history.
Founded in 1965, Harford became renowned for its premium silica sands, which it supplied to the golf industry. In more recent years, the company diversified and established one of the region's leading reclamation facilities. In 2014 it began producing recycled aggregates, and in 2016 it introduced crushing operations to recover saleable materials from incoming inert waste.
When commissioned later this year, Harford's new wet processing plant will be utilized to accept CD&E waste from various sources and produce a range of recycled sand and aggregate products that can be reintroduced to the local construction industry as sustainable alternatives to virgin quarried materials. Among the materials the new plant will produce are washed coarse and fine sands as well as various sized, multipurpose aggregates. As it can be adjusted, the final product output can be fine-tuned to meet the market's needs and customers' own specifications.
According to Northern Ireland-based CDE Global, Harford's new CD&E processing set-up will also enable the company to partner with public and private entities to process material from local construction and infrastructure projects. Over time, these recycling efforts will help establish a full-cycle materials economy, thereby moving the industry and region toward a more sustainable future.
Harford says their 80-acre campus is dedicated to supporting the circular economy by providing a one-stop facility for local construction companies to responsibly dispose of CD&E waste and back-load their fleet with valuable recycled materials that can be reintroduced to the construction industry for use in high-value applications.
"Wet processing is a new direction for our company and one that we're very excited about as we see great potential for growth in the recycling sector with the support of CDE technology," commented Miguel Lambert, president at Harford Minerals. "We first encountered CDE at CONEXPO. . . and were extremely impressed with its technology and the potential to apply it back home to local CD&E waste."
Lambert continued, "We're passionate about sustainability and minimizing our environmental footprint. With a partner like CDE, we can better embody our core values and pioneer new technologies in our region. It's this type of technology and investment that will stimulate progression in our industry, steering it toward a more sustainable future."
According to CDE Business Development Director for North America Darren Eastwood, consultations on this project were facilitated virtually.
"What makes this project unique is how it has progressed despite the challenges caused by the pandemic," said Eastwood. "Very soon after CONEXPO [2020] concluded, strict restrictions came into effect so our negotiations and consultations over the past year with Harford have been conducted remotely. This is a huge endorsement for CDE as it demonstrates great confidence in our solutions for helping Harford to achieve its commercial and environmental aims."
According to the U.S. Environmental Protection Agency (EPA), 600 million tons of C&D debris was generated in 2018 with concrete representing the largest fraction (67.5 percent). The second largest end destination for C&D debris after aggregate (52 percent) was landfill (24 percent). This means that a quarter of all C&D debris that could otherwise be repurposed is simply discarded.
Investment in sustainable solutions is important for the future viability of materials processing companies, explains Eastwood.
"The industry needs to fundamentally transform its practices. Every day we see significant volumes of CD&E waste being sent to landfill, but with the right technology and the willingness to adapt to new ways of working this material can be recycled to recover high-value construction sand and aggregates and returned to good use in the industry. What a business does now could define its future, either creating opportunity for sustainable growth or restricting its potential due to not addressing its environmental impacts."
Eastwood adds, "We're very pleased to partner with Harford to deliver our latest recycling project in North America. Harford's management team not only recognizes the urgency of the issues affecting the industry but responds to it with the ambition to act and invest in new technology to drive positive and transformational change."
This article was originally published in the May/June 2021 edition of Recycling Product News, Volume 29, Number 4.