USTMA report finds that recycling of end-of-life tires has slowed
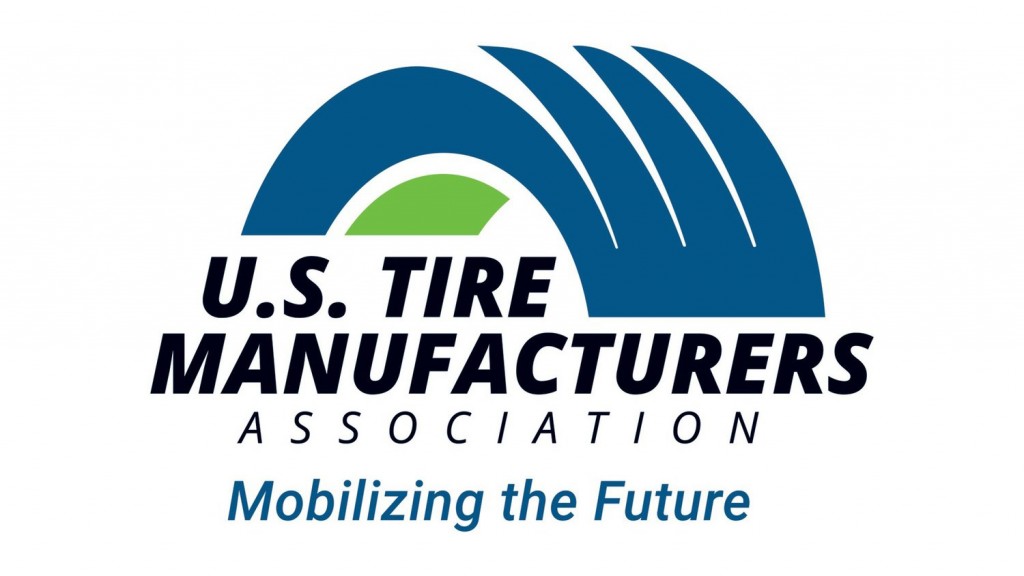
While tires remain one of the most recycled products in the U.S., end-of-life markets are not keeping pace with the annual generation of scrap tires, a new report released by the U.S. Tire Manufacturers Association (USTMA) reveals.
The 2019 Scrap Tire Management Report reveals that almost 76% of scrap tires were recycled in products such as rubber modified asphalt, the manufacturing of automotive products and mulch for landscaping and other products, and tire-derived fuel in 2019. This is down from 96% in 2013, when scrap tire recycling peaked.
"Three decades after we successfully eliminated 94% of the over 1 billion scrap tires stockpiled around the country, this report reveals that efforts to find and develop new uses for scrap tires have stalled," said Anne Forristall Luke, president and CEO of USTMA. "We must take immediate steps to grow new and existing markets to recycle 100% of scrap tires. This not only protects our health and the environment - it drives innovation and jobs."
While the number of scrap tires generated each year grew by almost 7%, the total number of scrap tires recycled or reclaimed has not significantly changed since 2017. The report found that 56 million scrap tires remain in stockpiles, mostly in Arizona, Colorado, Michigan, New Jersey, New Mexico, Texas, Virginia and Washington, half of which-New Jersey, New Mexico, Texas and Virginia— do not have active stockpile cleanup programs.
USTMA and its members work closely with state regulators, recyclers and other stakeholders to manage scrap tires and develop recycle and reuse markets.
Michelin, Bridgestone and Continental use recycled carbon black (rCB) to produce new tires. Michelin also partnered with Scandanavian Enviro Systems to increase end-of-life tire recycling using a pyrolysis process which converts scrap tires to new raw materials. Bridgestone joined with Delta-Energy Group to bring at-scale use of rCB to the tire market, and Continental works with Pyrolyx to help tire manufacturers scale up the production of rCB from scrap tires for use in products ranging from mobile phones to ink pens.
USTMA urges state regulators and federal law makers as well as recyclers, industry and environmental groups, and academic partners to do more to advance a circular economy. Specifically:
- States must resist the urge to shift scrap tire funds away from their intended purpose: to grow scrap tire reuse and recycle markets, clean-up piles and enforce state laws. USTMA supports reasonable fees on the sale of new tires to manage state programs, like those collected in 35 states.
- New public and private sector investments are needed to create innovation challenges, research the lifecycle impacts of scrap tires in different end use markets, and create a national portal for states to share data.
- State and federal policies should encourage the growth of reuse and recycle markets including investments in sustainable infrastructure like rubber-modified asphalt and stormwater infiltration galleries, changes in state transportation specifications to allow the use of rubber modified asphalt, and consideration of scrap tires in climate policies.