A robotic future for recycling: optimizing the sort at the modern MRF
Machinex Sales engineer Matthew Smith provides insight on the latest artificially intelligent robotic sorters and how to optimize their efficiency at the MRF
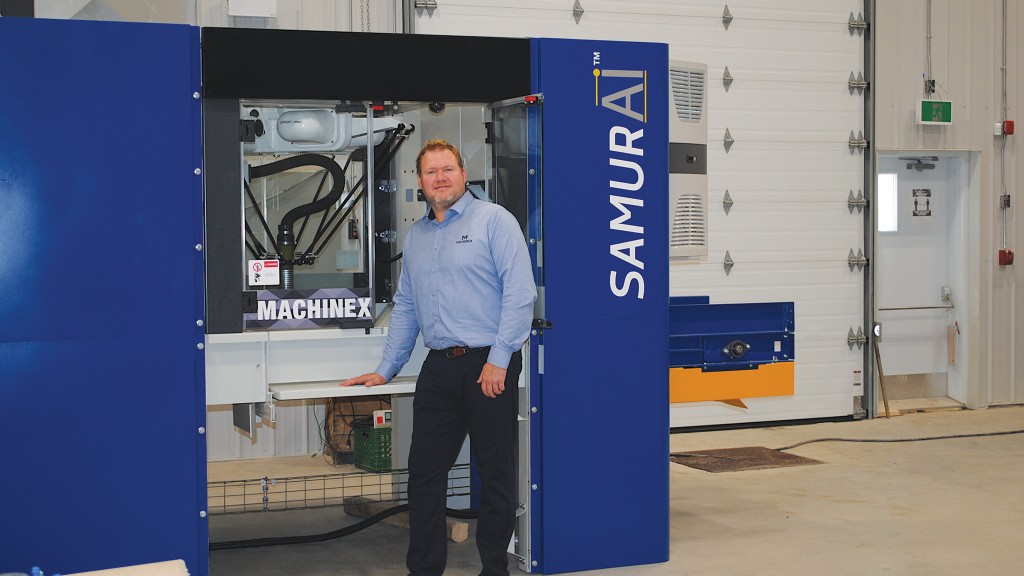
Artificially intelligent, high-speed robotic sorters are now commonly considered to be the future of large-scale recycling. They are one of many technology-based options that can help recyclers adapt to both changing practices in our industry, and changing commodities markets worldwide.
Currently, there are only a handful of manufacturers of robotic sorting systems for recycling applications, with available machines offering as much as 70 picks per minute (on a recovered fibre or plastics line in a MRF or other recycling facility). Robotic sorters use the latest optical vision technology, learn as they go with artificial intelligence, and can recognize and sort (either positively or for quality control) a wide range of plastics, cartons and paper, including film, and in some cases hard-to-detect black plastics.
The cost-efficiency and safety benefits of automated pickers as an addition to, or replacement for, human pickers is catching on. Every month, more and more recycling facilities and MRFs around the world are adopting these high-tech systems into their plants, all with the goal of maintaining and increasing profitability in especially challenging times.
Canadian-built robots
Born from roots in the agriculture industry Machinex, the Plessisville, Quebec-based MRF and turnkey recycling systems provider, is 50 years old in 2020. Machinex is the only large-scale manufacturer of optical and robotic sorting technology for recycling in Canada and currently offers two robotic sorter models. The SamurAI 800 series is tailored toward a wider belt and the smaller SamurAI 650 model is ideal for anywhere with tighter space constraints for installation or operation.
According to Machinex Technology Sales Engineer Matthew Smith, the 800 model is primarily targeted at the North American market, while the compact 650 model (which fits pre-assembled in a single container for shipping) is more geared for the European market.
"Normally, in Europe, the sorting line is in an enclosure, with conveyors that are about one metre wide, so based on the enclosure restrictions you need a smaller robot," explains Smith. He adds that wherever it is located, the Machinex' SamurAI robotic sorter is particularly ideal for paper, plastics and aluminum recyclers looking to purify their streams and reduce output contamination.
The robotic sorter at work
The SamurAI robotic sorter is taught to recognize various materials via its camera and its AI (artificial intelligence.) Smith explains that different materials are labelled according to their size, shape and composition, and then loaded into the AI of the robot. Based on this information the robot recognizes various materials.
Key features of the SamuraAI include its unique multi cyclone vacuum system and its ability to positively pick and remove plastic film from a line. Other robotic sorters on the market currently use compressed air to induce their vacuum.
"The way our system uses a blower to induce a vacuum works similar to a multi-cyclone," explains Smith. "Many would know this concept from Dyson vacuum cleaners. It's a similar principle to that. Our system sucks the objects through the tubing into the multi cyclone, which causes the heavy material to go to the sides and then drop down. The clean air exits, and thus efficiently removes film from the line."
The recipe for success
In today's MRF, materials can be sorted for quality control (picking out what should not be in a stream) or positively sorted (picking out the desired material for capture).
"We can pick all different types of plastics, cartons, film or aluminum," explains Smith. We can do a positive sort or we can do quality control.
"We've got some robots doing the QC sorting on different plastics. They're removing unwanted materials and purifying the plastics stream. We've also got one that's processing aluminum cans, doing QC on an aluminum line. It's picking anything that is not an aluminum can and removing it to get a purer stream; this is quality control."
He continues by describing positive sorting. "If you've got a stream with many different types of material, and you're going for natural HDPE, you can target and pick out this material first, resulting in a very pure stream of that material. We can also positively sort a second material. So, if the robot is programmed for natural HDPE, but doesn't see any, a second priority can be set, such as coloured HDPE, and it will automatically pick the second material on its list and place it in the desired chute."
Currently, positive sorting of plastics in North America focuses largely on HDPE or PET. The SamurAI will also sort PP (polypropylene tubs and lids), but Smith says this choice would depend on the market. Recyclers currently are getting a better price on HDPE than they do for PP.
"We create different recipes according to customers' needs. The type of material a robot is programmed to pick at a given facility is best determined based on the market prices of certain materials.
"Natural HDPE is currently the highest priced recovered plastic, so if a facility is picking both HDPE and PET, they may not want to set the robot at a recipe to pick 50:50.
"If the market dictates, and there is enough material, it might be better to pick 70:30 (natural HDPE:PET). The SamurAI would then be programmed to pick 70 percent of the natural HDPE from the line and only 30 percent of the PET. This way, recyclers will get a better return than if they were to pick at a rate of 50:50."
Alleviating labour challenges
Currently at most MRFs, there's a policy in effect for keeping a 2-metre distance between colleagues.
"It's about making sure that you can actually get the staff in to do the job and have enough space to do it." Smith says that normally a robot can do 70 picks per minute, while an average person does 35 to 40 picks a minute. "With one robot, you've almost doubled your manpower." It also helps avoid the risk of having employees in close quarters, inside a dusty, very-hard-to-sanitize environment.
Smith agrees that the industry has been moving toward increased automation for decades now, and that in the future it's going to become almost completely automated.
"A recycler can get $75 per ton for a certain quality or purity, or spend a little bit more money to automate and produce very pure output. Then the return can go up to $120 per ton. That is a huge impact."
He also agrees that levels of purity demanded by the market for MRF output are challenging for current systems to achieve.
"You need a high level of quality control. To do that with a person who has a limited pick rate, you then have to employ two people to do the job. With a robot, maybe you only need one. And they're just going to get faster and more efficient. The current status is that our robots are doing 70 picks per minute. In a year, we might be up to 80 or 85 picks per minute. This could be done with the same equipment bought today. It's just a case of software upgrades and programming in better recognition.
According to Smith, with 80 to 85 picks per minute, you're definitely replacing two people. "The robot doesn't need a break and maybe it works two shifts. Social distancing in the workplace could be around for some period of time. In this scenario, one robot can potentially free up two people to work in other areas of the MRF where manpower is now needed."
Keeping up with an evolving Stream
A unique feature of SamurAI robots is that they are connected to the MACH Cloud, through which Machinex updates the system on an ongoing basis. MACH Cloud is offered free for the first year, and then it's cost is based on a subscription.
"With this system, any new developments made in regards to improvements in the software (adding better recognition capability for example, or programming in new types of materials to be recognized, or different flight paths that the robot takes toward the bin) can be updated simultaneously, for all new users and subscribers, wherever they are located.
"For new packaging materials entering the market, the robot won't recognize it until it is programmed in," continues Smith. "You could have a recycler in Quebec who notices something new. We teach their robot about the new item, generate all the data, and then through MACH Cloud, everyone that is signed up receives the new data. As part of the MACH cloud, all our customers benefit off each other."
Financing the robot
For most MRFs and other recycling facilities, an automated robotic sorting unit is an add-on piece of equipment. "It's not like you're building a complete new MRF from scratch, which costs millions, but it is a big investment," says Smith. "For those with an existing MRF, generally they are adding a robot to their system. The opportunity to find the capex [capital expenditure] in the current market can be really tough. There's also the fact that the value of the end material being sold is down compared to what it used to be. So, for MRF owners to go out and get that capital investment to invest in a robot can often be difficult."
Machinex now offers leasing options for their robots to help make the technology viable for more recyclers. "To add a robotic sorter to a MRF using a leasing program and spread the cost out to three, four or five years, can be really beneficial," he says. "The expenditure per month is based on a fixed rate, so there's no big surprises."
Smith agrees that leasing is an interesting, newer strategy which may well extend to other types of equipment in the near future and become a more regular way of doing business in the recycling industry. "Many big companies can just go ahead and buy what they need. But other ones, maybe a smaller MRF, or small privately owned facility, it's a really good option to go for a leasing program.
"It's also a case-by-case situation," he continues. "One MRF might want to lease just the robot, but immediately pay off the costs for installation and any upgrade to their structure. When it comes to that, we're flexible. It all depends on what the customer requires."
When asked if Machinex is working on any new recycling equipment that will incorporate AI, Smith says Machinex now offers a vision system that was first installed this past spring in a U.S. facility operating their equipment. This unique device is powered by AI and uses a combination of a hyperspectral infrared camera and a high-definition RGB camera to identify and label items on the belt into material categories. The unit will ultimately generate real-time information in regards to the stream composition.
Smith concludes by emphasizing, "We're not just a robot manufacturer here at Machinex. We understand the whole process of recycling. We see the robot as a unique piece of equipment, but we can also see the start and the end of the entire recycling process. We make sure a robot, as a piece of specialized equipment, is integrated in with the rest of the equipment in a MRF or other recycling facility. If needed, we're also going to tune a facility's optics or ballistics.
"We can change a lot to best suit the robot, so we get the very best out of the MRF." RPN
This article was originally published in the September 2020 edition of Recycling Product News, Volume 28, Number 6.