Powerful optical sorting technologies, artificial intelligence and robotics reduce contamination for recycling operations
TOMRA's Regional Director Americas talks about the ins and outs of new AUTOSORT advanced optical sorting for recyclers
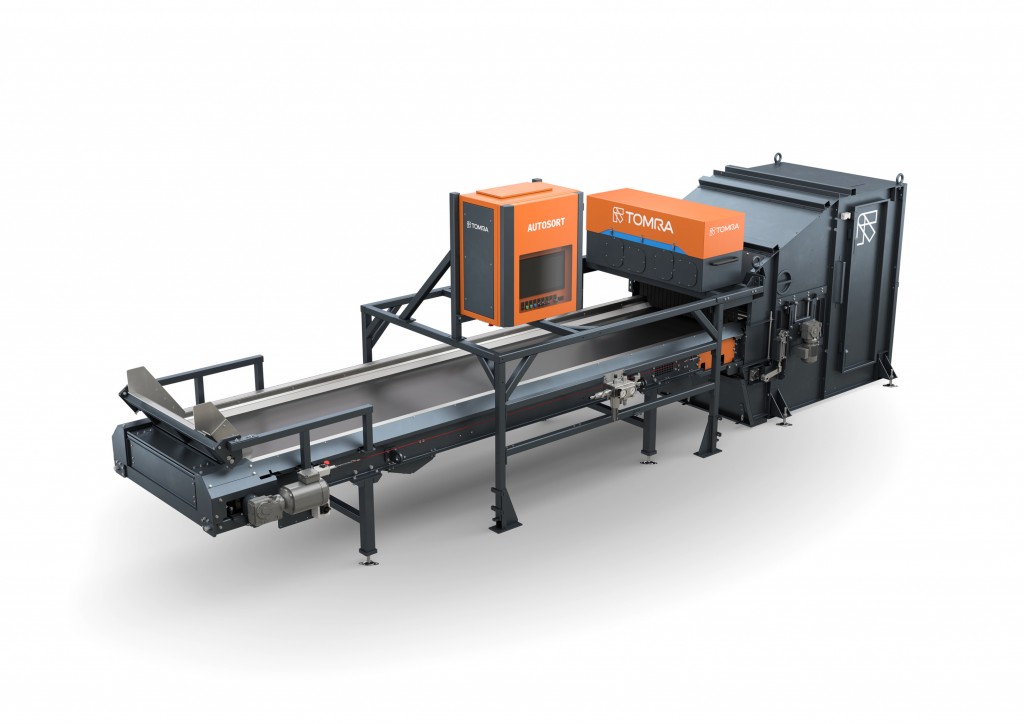
TOMRA Sorting Solution's next generation AUTOSORT optical sorting system, launched at a worldwide digital event in June, is designed to provide a new level of efficiency for MRF operators and other recyclers tasked with creating highly pure output streams. According to TOMRA, their new AUTOSORT is compact, highly flexible and upgradable, bringing together multiple technologies to deliver complex, artificially intelligent (AI) sorting of recovered paper and plastics at very high throughput rates.
The new line, now available worldwide, includes the AUTOSORT optical sorter, AUTOSORT SPEEDAIR a 6m/second high-speed belting system, and AUTOSORT CYBOT robotic sorting. Also new to the line is a DEEP LAISER add-on component which enables detection of hard-to-detect materials, including black plastic and glass, as well as updated Intelligent Object Recognition.
RPN caught up with Carlos Manchado Atienza, TOMRA Sorting Recycling's Regional Director Americas to talk about the key implications of their next generation sensor-based sorting lineup for the recycling industry.
According to Atienza, who has worked at TOMRA for 20 years, and is currently based out of Charlotte, North Carolina, the AUTOSORT is already one of the leading systems worldwide for automated sensor-based sorting, with more than 6,000 units installed. The new generation is based on the previous version, incorporating a high level of material detection accuracy, robustness and compactness, but also combines multiple technologies into one.
The new generation optical sorting system uses a combination of TOMRA's latest FLYING BEAM NIR (Near-Infrared) optical sensing technology and SHARP EYE which increases light efficiency while maintaining the same energy consumption, enhances sorting sharpness and improves the separation of difficult-to-target fractions. Both are now standard on the new machines.
Plus, this new generation includes updated Intelligent Object Recognition (IOR) software together with a new DEEP LAISER add-on, which enables detection of black plastic, glass and everything that NIR cannot see.
The result of all of these technologies working in tandem, for recyclers, is that the range of materials that can be detected and the speed with which they can be sorted, can be significantly increased, creating highly pure, highly valuable end product with very low contamination.
"With the combination of technologies in the new AUTOSORT, we are able to see a different kind of chemical (makeup) of the same material," explains Atienza. For example, for different PET bottles and trays, "It's all PET for NIR, but combined with the other technologies, we are able to see the difference.
"We are able to identify and sort, for example, different kinds of PET, such as trays, bottles, etc., which is very important for recyclers, because the quality of the end product can change when you have a lot of trays on the PET line. We definitely see more and more PET trays on the market," which he points to as one of the drivers for the development of this technology. Key to taking material detection to the next level is DEEP LAISER, which is an optional add-on to the system.
According to TOMRA, the DEEP LAISER is one of the first fully integrated systems of its kind, and stands out for its compactness and flexible range of uses, with object recognition that enables a deeper sorting sharpness. This includes the use of Artificial Intelligence (AI) via Deep Learning which TOMRA first introduced in 2019.
In basic terms, FLYING BEAM's NIR/VIS (Visual Spectrum) technology makes an overall determination of what kind of plastic and colour is on the belt, and SHARP EYE looks more closely at the chemical composition, to give a deeper sort, differentiating between different types of PET, for example. When you add on the DEEP LAISER component, it detects material that other optical sorters cannot detect.
"It is a laser combined with an artificially intelligent camera, using our IOR software," explains Atienza. "With DEEP LAISER we are sorting material on the conveyor that the FLYING BEAM and SHARP EYE cannot detect, such as black plastic or glass." He says it detects and sorts these materials out as an impurity, and that due to the IOR, the system sees, and is able to learn about, a very wide range of different types of material, detecting chemical composition, shapes and colour.
"With our AUTOSORT technology we can see types of materials that many other technologies cannot see. For example, our machine can differentiate LDPE, (low density polyethylene) from linear LLDPE. It's mostly the same material, because it is all LDPE, but they have differences, and we are able to see it, even at 6m/second."
Another example is LDPE and HDPE film, he says. "With films, you have low-density and high-density polyethylene, and we can see that difference, because our sensor has very high detection sensitivity."
In addition to its vastly increased sorting capacity overall, the new AUTOSORT ValveBlock geometry system is also 25% more powerful, with a reduction in air consumption of about 15%, compared to the previous version. This contributes to lower operating costs, including less electrical consumption, and notably this new generation AUTOSORT also auto calibrates every millisecond for optimal operation through changing conditions.
"This is very important," says Atienza, especially because NIR is very sensitive to temperature. "The auto calibration every single millisecond allows us to operate efficiently through a wide range of temperatures during a day," he says.
AUTOSORT SPEEDAIR
AUTOSORT SPEEDAIR is a highly customizable system designed to stabilize light materials such as plastic films or paper on a high-speed conveyor, thus generating higher throughput and enhancing sorting quality. "Throughput is important but so is detection," explains Atienza, adding that previously, with most optical sensors, the belt is moving at around 2.8 m/second, or maybe up to 3.2 m/s.
"With SPEEDAIR we are doubling the belt speed and average throughput to about 6 metres/second. However, detection at the end of the day is the most important, because you want to have the best sorting performance. AUTOSORT technology is able to identify and provide exceptional sorting performance at high belt speeds."
TOMRA collaborated with a company specializing in high flow air systems when designing this component of the AUTOSORT system, which uses an open, uncovered belt. Atienza explains that basically the open belt concept is a unique selling feature for the AUTOSORT SPEEDAIR.
"Others have a covered belt to keep light material on the belt and avoid losing material when conveying at high speeds," he explains. "The SPEEDAIR uses an open-belt concept combined with recycled airflow from the top and back, to keep material from floating off the belt when travelling at higher speeds."
He says the open concept allows operators to see exactly what is on the belt at all times, minimizes the chance for material blockage, and enables service technicians to quickly accesss maintenance items to reduce machine, and circuit, downtime.
Due to its adjustable air recirculation capability, SPEEDAIR also provides the benefit of increasing overall flexibility at the recycling plant. "We can adjust air recirculation depending on the density of material," Atienza says. "We don't waste air, and you can control the circulation on the belt. It's flexible, so depending on the type of film, or paper, or the type of application, operators can play with the air recirculation to optimize throughput."
AUTOSORT CYBOT
The third technology introduced by TOMRA this past June is the AUTOSORT CYBOT robotic sorting system, which features a new generation AUTOSORT scanner with all extra technologies, an electromagnetic sensor and a robot arm. According to TOMRA, it is the first robotic sorter for the recycling industry that combines four technologies: Near Infrared (NIR) and Visible Light (VIS) spectroscopy, DEEP LAISER, and if required, induction for ferrous and non-ferrous metals recovery.
Atienza adds, "Depending on the application, we can customize AUTOSORT CYBOT with our other optional sensor like GAIN (deep learning) and SUPPIXX (image processing.)
TOMRA says the CYBOT's robotic arm is capable of simultaneously sorting material into four different streams or fractions depending on the infeed material size, colour and criteria of the target fractions.
"With the CYBOT, we are very, very happy about the test results that we have," commented Atienza. "The system combines camera detection and artificial intelligence, among other technologies, which is partly why it took us a little bit longer than some to develop our robotic sorting technology."
He explains that the addition of the CYBOT to the AUTOSORT line, used as quality control at the end of the line, provides another level of separation capability. For common items that the robot will sort, like plastic laundry detergent bottles, for example, Atienza says two bottles can be the same colour, the same shape, the same brand, it can be exactly the same bottle of detergent, but one is HDPE and one is PET.
"This happens frequently," he says. "This is why we decided to go with a robotic platform that not only has the artificial intelligence, but which is combined with our AUTOSORT ‘heart.'"
In the end, he says it is the combination of all the different material detection technology incorporated into the AUTOSORT system that makes it so effective, adding that data capture and machine monitoring performance is another important element. When it comes to data capture and machine monitoring, all the components in the AUTOSORT line are compatible with TOMRA Insight.
"We know every single material that goes through our system, even if we don't sort it," he says. "The data that we can capture is super important for the customers, so that is why we implemented TOMRA Insight for all of our systems. All systems can be linked to TOMRA Insight so that customers can better control their facilities. It is not only unit by unit control, but it works for all units from our line. We can connect it to our SPEEDAIR or FLAKE SORTER, providing a comprehensive view of what's going on in the entire plant. And the Insight platform provides capability to see not only one machine, or one MRF, it delivers the ability to preview production data from multiple locations simultaneously." RPN