Expeditious adaptation is the name of the game for recycling in the age of COVID-19
Letter from the Editor
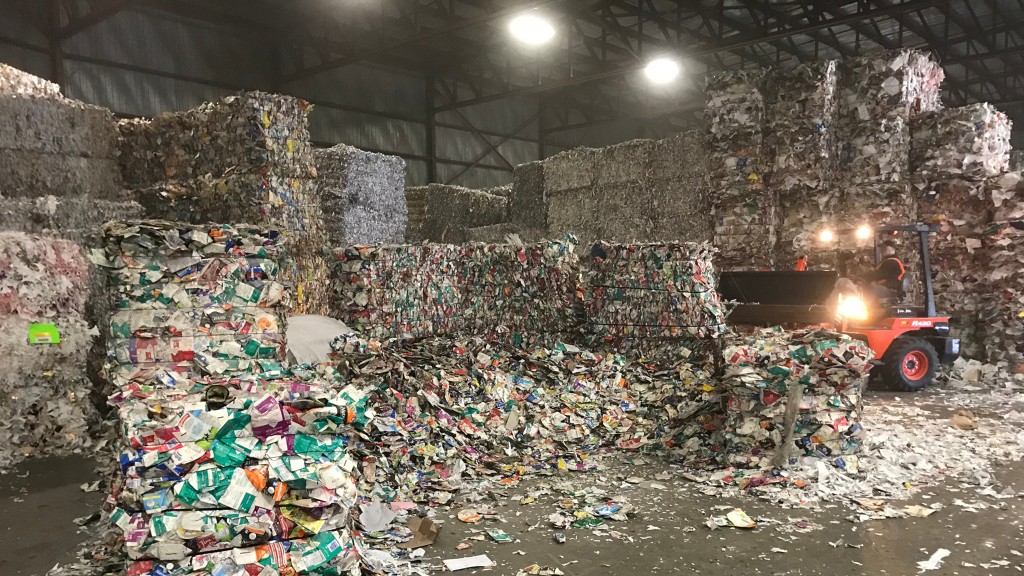
Monumental change is afoot since the COVID-19 outbreak began. We can all see it in so many aspects of our lives, from education to social conventions, to business practices. Certainly, the recycling and waste management industry has felt the effects, and it is adapting swiftly.
The Sustana Fibers paper mill in Quebec (inside the mill shown above) is a poignant example of a business that has revised a portion of its business incredibly quickly to accommodate completely unforeseen circumstances brought about by the pandemic.
According to Isabelle Faucher, managing director of the Carton Council of Canada, there are two factors since March that accelerated Sustana's decision to be the first mill in Canada in over 20 years to accept recovered cartons as feedstock. Firstly, there is a renewed demand for products made from recovered paper, such as paper towels, toilet paper and grocery shopping bags. Secondly, SOP (sorted office paper) streams have all but halted due to widespread office closures. Cartons, as it turns out, are a great, direct replacement for SOP.
Our feature byline: "First Canadian mill in decades to accept cartons a positive step for the circular economy," digs into the implications of this news based on an in-depth interview with Isabelle Faucher.)
The COVID-19 pandemic has resulted in different scenarios around the world for different materials. In Europe, there are reports about serious shutdowns in the plastics recycling and processing sector, but in North America, there is now a huge demand for plastic screens and shields for retail and other businesses. This has to bode well for multiple plastics categories. Similarly, the high demand for fabric face masks will be positive overall for textiles recycling, eventually, if not right away, providing a much-needed, likely sustainable end market.
Besides significant changes to demand for recycled materials, it is interesting to see how quickly manufacturers in the industry are reacting to our new reality. Some examples of rapid reaction recently include major truck manufacturers Mack and DTNA, which are among the first to adjust their businesses to accommodate the increased demand for online remote troubleshooting, support and parts ordering, as well as online education options for customers and potential customers.
For MRFs and recycling facilities, Van Dyk Recycling Solutions has introduced augmented reality technology that allows recycling industry customers to receive guidance and customer service remotely, hands-free and safely during the COVID-19 crisis and beyond. Buffalo Turbine is another quick adapter, revising its industrial sprayer systems to accommodate demand for site, facility and equipment disinfection. (See Spotlight this issue for more details.)
Machinex is one more example of a company that has reacted since March by being one of the first recycling technology and systems providers in the industry to offer a leasing option as a way to help recyclers and governments make large, capital-heavy infrastructure and equipment purchases. The leasing option is available for the company's artificially intelligent SamurAI robotic sorting systems to start. This is very likely a financing trend that will increasingly take hold in recycling and waste management.
Indeed, our industry is evolving from every angle, and due to the pace and scope of the change, it can be overwhelming for many. Still, it's not out of the ordinary for the recycling industry to display such affinity for adaptation. Only two years ago, global markets shifted considerably, with the advent of China's National Sword Policy restricting imports of anything other than highly pure recovered materials.
Case in point, TOMRA (our May/June 2020 Recycling Product News cover story) has introduced a modification to its automated sorting technology which directly opens up needed domestic markets for auto shredders producing Zorba (the nonferrous, mostly aluminum byproduct of shredding).
This new sorting technology upgrade is designed to allow scrap recyclers, for the first time, to efficiently and profitably turn piles of unsellable Zorba material into highly pure low-magnesium aluminum Twitch, which is in great demand from domestic secondary steel mills.
Whether it's evolving technology to produce material that fills a new demand, re-shaping the equipment supplier relationship, or revising a business strategy to accommodate changing incoming streams, expeditious adaptation is surely the new "name of the game" in recycling and waste management.
This article was originally published in the May/June 2020 edition of Recycling Product News, Volume 28, Number 4.