Goudsmit builds magnets for iron-free carbon black
Conductive carbon black for lithium ion batteries must be iron-free
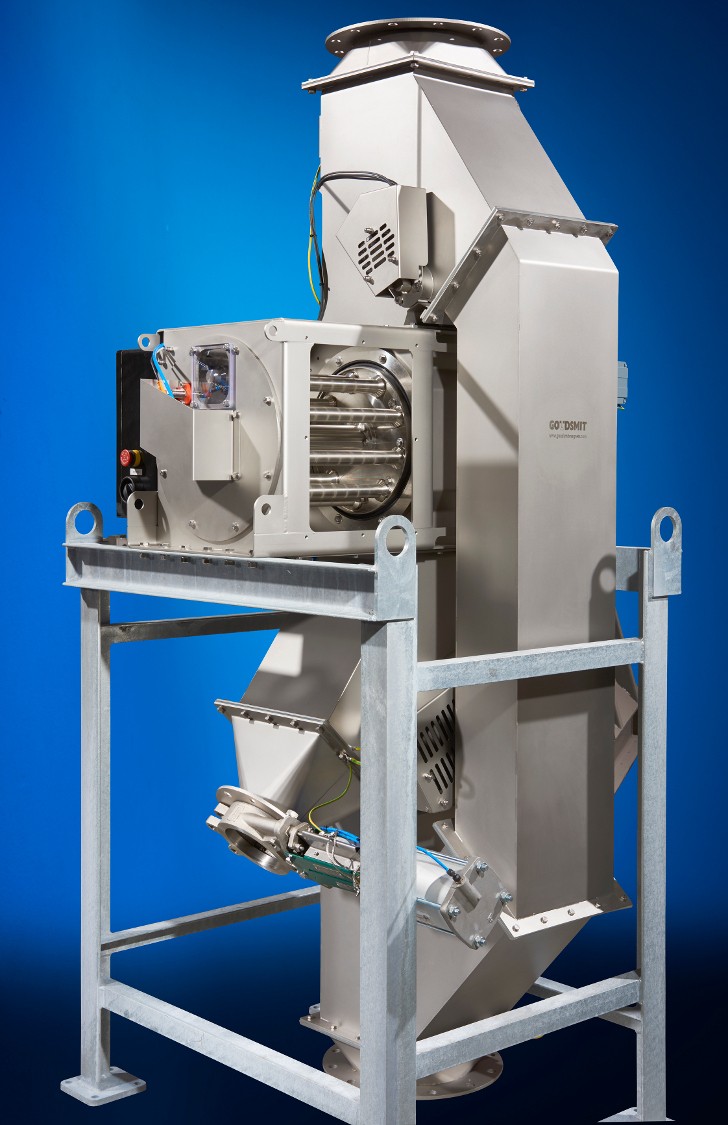
Goudsmit recently built two magnets to be used for the production of iron-free carbon black by a large European manufacturer. These self-cleaning, rotating magnets remove iron particles as small as 30 microns from the very dry, poorly flowing conductive carbon black used for lithium-ion batteries.It is essential that this product is 100% metal-free, because metal particles would change the conductivity. In this line, the rotating magnets process at a relatively low capacity of 1500 kg per hour. If necessary, however, such magnets can process at capacities of up to 40 m3 per hour.
The magnets are compliant with the ATEX standard and are resistant to temperatures of up to 70 °C. Higher temperature resistance is also possible. The rotating design ensures that the poorly flowing powder does not accumulate on the magnetic bars and they come into better contact with the material, thereby improving the separation rate. In this case, the production of carbon black is a continuous production process that must not be interrupted.
Therefore, two self-cleaning magnets - each with a bypass - have been placed in this production line. This means that at least one magnet is in operation during cleaning and both magnets are in use 99% of the time.
CARBON BLACK
Carbon black is a very dry, poorly flowing product that is used in sealing and insulation materials, rubber, batteries, electrodes, and paint and coatings. Iron particles are obviously undesirable in seals and products such as batteries, so they must be removed. The magnets are located in a pneumatic (vacuum) pipe, and the rotating movement prevents bridging and clogging of the magnet. The use of neodymium-iron-boron (NdFeB) magnets, with a flux density of 9140 gauss at the bars, ensures that even very tiny iron particles of ± 30 microns can be removed.
CLEANING
For cleaning, the continuous product flow is redirected by means of a bypass. This consists of two valves that completely isolate the magnet from the process. Then automatic cleaning of the bars takes place in the product chute and the trapped iron particles are sucked out of the product chute using an even lower vacuum of 0.8 bar.