Black Bear raises 11 million Euros towards solving the global waste tire problem while slashing CO2
Dutch company aims to scale up unique "Tire to Carbon Black" technology
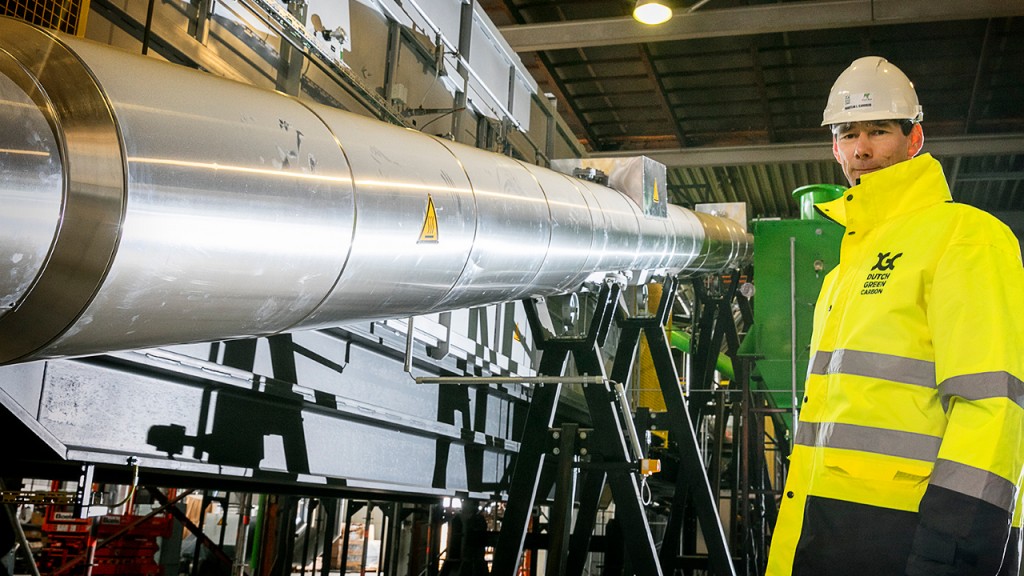
Every year, 1.5 billion tires reach the end of their life. The vast majority get dumped or incinerated, releasing massive amounts of CO2 and destroying highly valuable resources. To solve this waste tire problem, Netherlands-based Black Bear has developed a unique carbonization process to transform used tires into recovered Carbon Black (rCB). The company has now successfully closed a growth funding round of 11 million Euros to refine the environmentally-friendly process and to start the worldwide roll-out of the technology. This brings the Dutch cleantech company a crucial step closer to bringing the circular economy to tires.
Recently, four new partners have become stakeholders: the largest Dutch banking corporation ING Group; two Netherlands-based investment firms 5square and Social Impact Ventures; as well as the conglomerate SCG from Thailand (Asia).
"This new consortium means much more than just fresh capital", says CEO Martijn Lopes Cardozo, "they are strategic partners, who will play a key role in the development of our technology and who will speed up our international roll-out." Existing investors, including the original funders Chemelot Ventures and DOEN Participaties (Ventures), have also contributed to the round.
Black Bear's industrial-scale prototype plant is located in Nederweert, The Netherlands. It is capable of processing more than 1 million waste tires annually, producing 5000 tonnes of Carbon Black, 5000 tonnes of bio-fuel, 3000 tonnes of steel and one megawatt hour of green electricity. The plant is operated in partnership with Kargro, one of Europe's foremost recyclers of tires.
Carbon Black is vital for the production of tires, technical rubber goods, inks and coatings. It is found in the ink of pens, smartphone covers or in anything painted black, but, unfortunately, Carbon Black is traditionally produced by burning oil. However, tires contain about 30 per cent Carbon Black — and an opportunity. Black Bear now offers the first Cradle-to-Cradle Certified™ recovered Carbon Black to customers worldwide. One of more than 30 clients is AkzoNobel: The coatings company is one of the plant's earliest customers and uses the raw material to make powder coatings.
"It is remarkable that Black Bear is capable of making old tires into a very high-value product that can replace a polluting raw material," said Mark Weustink, ING Group's ING Sustainable Investments. "During the process, they also generate energy, which means the production process is highly energy-efficient. With its pioneering circular model, Black Bear creates durable change, and it has already won some large clients such as AkzoNobel."
"We are highly committed to the circular economy and Black Bear is addressing a global problem, especially in significantly improving the carbon footprint of Carbon Black production," said SCG President Cholanat Yanaranop. "As an integrated petrochemical company that focuses on creating sustainability along with innovations, we are highly interested in the success of Black Bear's solution."
"We believe in the huge positive environmental impact of the technology — especially since the Black Bear product can compete with virgin Carbon Black in terms of cost price and quality," commented Helmer Schukken of Social Impact Ventures. "Another reason for our investment is the great management team, which consists of not only talented engineers but also seasoned professionals in sales, finance and other functions required for global roll-out."
"When you really think about it, it's unbelievable that only 10 per cent of our resources are currently part of circular economies," added Mark Gitsels of 5square. "That's why we full-heartedly support the outstanding management team of Black Bear: Their disruptive technology is an opportunity for us to help make the world that bit better and at the same time yield attractive returns."
Founded in 2010, Black Bear Carbon BV's unique CO2-negative process has been developed for producing the world's first Cradle-to-Cradle certified Carbon Black from tires. The sustainable Carbon Black produced is used by clients worldwide for the production of tires,technical rubber, coatings, plastics and inks. The company plans to roll out more than 1,000 plants all over the world, in cooperation with local partners, commenting that this would have a huge environmental impact, resulting in CO2 emission reductions equivalent to the planting of more than 1 billion trees, and potentially reducing the world's annual oil consumption by more than 215 million barrels.