The state of Tire Recycling in Ontario: Q&A with Andrew Horsman
WITH ONTARIO TIRE STEWARDSHIP'S PENDING DISSOLUTION, WHAT WILL HAPPEN TO END-OF-LIFE TIRES IN THE PROVINCE?
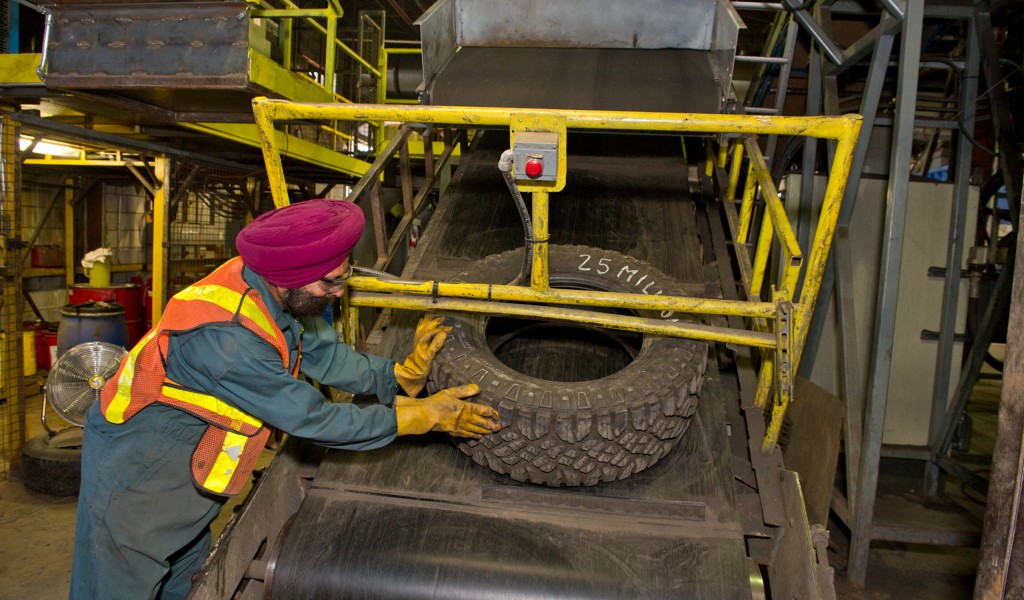
Earlier this year, it was announced that Ontario Tire Stewardship's Used Tires Program had reached a significant milestone: the recycling of its 100 millionth tire since the program began in 2009. Alberta is the only other Canadian province to achieve this milestone.
Before the implementation of the Ontario program, many of the province's tires ended up in landfills or accumulated in tire piles. Because of Ontario Tire Stewardship's (OTS) Used Tires Program (UTP), 100 percent of scrap tires generated in Ontario are currently recycled into high value, sustainable products - and importantly, no tires are burned, disposed of in landfills or illegally dumped.
OTS has also established a tire recycling network of over 700 stewards, 7,000 collectors, almost 100 haulers, and a group of 30 processors and recycled product manufacturers with the goal of building a sustainable future for Ontario and supporting the circular economy. Used tires in the province are now being redesigned into eco-friendly products including patio tiles, rubber landscaping mulch, gym flooring, playground surfacing, floor underlay and more. OTS has also invested more than $100 million into the Ontario economy through research and development, and into new markets that have led to the creation of hundreds of jobs. Additionally, through the OTS Community Renewal Fund (CRF) grant program, a total of 60 projects have been awarded over $1 million in funding for new and need-to-be-renewed public spaces, like playgrounds and fitness tracks.
Despite all of their success, OTS will cease to operate as of the end of 2018.
In November 2016, the Government of Ontario passed the Waste Free Ontario Act (WFOA, Bill 151) which began the process of revising the waste diversion policy framework in Ontario by repealing the Waste Diversion Act and setting the stage to transition existing stewardship plans to an Individual Producer Responsibility (IPR) model under the Resource Recovery and Circular Economy Act (RRCEA).
On February 17, 2017, the Ontario Minister of the Environment and Climate Change (MoECC) issued direction to OTS to develop a wind-up plan for the Used Tires Program. This plan is to be submitted to the Resource Productivity and Recovery Authority (RPRA) by October 31 this year, with the UTP to be fully wound-up on December 31, 2018. In consultation with various stakeholders, including an industry consultation session at the recent Tire and Rubber Recycling Association summit in June, OTS is now working on developing the wind-up plan as directed by the MoECC.
We talked to Andrew Horsman, OTS executive director, about the organization's successes and mandate for the UTP wind-up and closure, and about what it means for tire recycling in Ontario.
RPN: Tell us more about your milestone of 100 million tires recycled in Ontario.
Andrew Horsman (AH): It really is a testament to our commitment to making sure we maintain used tire diversion rates at the current high level, and that consumers are buying into the notion that there is a life for scrap tires, and that they are an important part of the solution.
Back when we launched this program in 2009, consumers' interests were really about ‘How do I get rid of my scrap tires? What is OTS going to do about the tire piles? And how are you going to eliminate new illegal dumping?' And so, we focused on those issues very early. More and more, what we saw through our engagement with consumers, either through social media or industry events, is that they are interested in what happens to the scrap tire. Where does it go? How does it get recycled? And what is my opportunity to participate as a consumer of those products?
And so while the hundred million is an impressive number, I think the story that is even more interesting is really about the growth of a domestic manufacturing industry that is using recycled tire material to make high-value, sustainable, high-performing products that consumers are interested in.
RPN: What can you tell us about OTS' success in end market development for recycled tires?
AH: In the early days, it was about building capacity, but for some time now it has been about developing markets that have the capacity and wherewithal to stand on their own.
Our focus at OTS has always been on developing markets that are beyond the commodity stage. When we launched our program, we had a number of goals. Our first goal was to make sure all of Ontario's tires were getting recycled; none of them were being sent for tire-derived fuel or alternative daily cover and landfill. We did that fairly quickly by setting up service contracts with both in-province and out-of-province recycling suppliers.
Our next goal was to really start moving tire recycling in Ontario up the value chains. That started with us working with the Ontario industry to develop enough capacity to manage all of Ontario's tires, which meant we had to double capacity, more or less, in the province. We hit that milestone in 2012, when capacity was enough to manage all of Ontario's scrap tires.
Our focus since then has really been on building markets domestically for recycled rubber, and that takes a number of forms. We work with Ontario-based manufacturers - companies that take recycled rubber and either mould it or blend it with plastics or other rubbers to make finished goods in the province - and have supported further innovation for the use of scrap tires through our research and development grant program.
We're focused right now on trying to develop the rubber-modified asphalt market in Ontario. And we've also got a number of programs, such as our Retailer Rebate Program where we work with retailers, and others, in trying to incentivize consumer behaviour, to encourage Ontario's consumers to buy Ontario-made recycled rubber products.
As well, through the OTS grant program known as the Community Renewal Fund, 60 community projects across the province have been awarded funding for new and need-to-be-renewed public spaces, like playgrounds and fitness tracks, further encouraging environmentally friendly building while boosting the Ontario economy.
All of those initiatives are about trying to maximize the value of recycled material to create a self-sustaining industry. We have also worked to develop the wherewithal within the recycling industry in Ontario to be able to supply those markets, which means building capacity. That means improving the tire recycler's efficiency and supporting them to be able to invest in their own operations, to make better, more consistent product, and on a more consistent basis. Because that is what those markets demand. It's also about creating manufacturing industry consumers as well.
Our mandate has always been very Ontario-centric. We've tried to create solutions in the province to manage recycled tire material, but the reality is that recycled tires is a North American market, not only for commodity material, but also for manufactured goods. So when we have a manufacturer that makes outdoor living products, whether it's flooring or planting pots, for example, their customers are all over the continent. You want diversified markets, but we also want to benefit in the province by using recycled rubber product wherever possible.
RPN: How will Bill 151 (the Waste-Free Ontario Act) affect the tire recycling industry in Ontario?
AH: The legislation that's been passed - the Waste-Free Ontario Act, Bill 151 - will fundamentally change how tire, as well as paint and electronics, packaging and printed materials stewardship works in the province of Ontario. Under the old legislation - the Waste Diversion Act - it led to the creation of one entity, OTS, to manage diversion services for the province.
In today's system, OTS is the entity responsible for diverting tires, managing tire recycling for all of the tire producers and other suppliers of tires and delivering these programs in a centralized fashion. We are the ones who are accountable to the Minister and our oversight body.
The new legislation will fundamentally change that, so the obligation to divert material will not rest with one entity, like we are today. It will accrue to the individual companies supplying the manufactured products [the source of tire waste]. In the new legislation, individual companies such as Bridgestone, Michelin, Ford, Toyota, Canadian Tire, etc., will be the ones who are legally responsible for achieving diversion. How they choose to do that, whether on their own or by joining some sort of collective group, will be up to them.
And so the consequence of Bill 151 for OTS is that as of December 31, 2018, our used tire program as we currently deliver it will cease to operate. Tire manufacturers will take over the responsibility as of January 1, 2019. It means OTS will cease to exist. Sometime in 2019, when we finish our remaining work, Ontario Tire Stewardship, as a corporation, will be wound up.
This last legislative review and change is basically the government's third attempt at reworking waste diversion on Ontario. It's not entirely surprising to us that it went this way. They're certainly charting new territory. No other jurisdiction in Canada is pursuing this kind of legislative approach. To my knowledge, no other jurisdiction in the world has done what they're doing here: where they've built one system, and then they're going to tear that down and mandate the building of a new system.
This change is creating uncertainty in the market. The finalization of the Regulation, followed by the producers beginning to develop their approaches to diverting tires, will eventually reduce this; however, at present, in the absence of these important elements there is a disruptive impact. Our job at OTS is to work to ensure stability and continue our high diversion rates from now until the end of 2018.
RPN: What will happen with end-of-life tires once the OTS wind-up is complete?
AH: My personal view is that of course tire diversion will continue to happen in Ontario. There will probably be two or three smaller versions of OTS out there, as well as some individual companies who might decide that they can do it on their own. They will contract directly with recyclers to ensure that tires get recycled in accordance with their legal obligation.
My concern is that there's a lot of uncertainty in terms of how this transition is going to happen. As we talk to our stakeholders, as we're developing our wind-up plan, the number one concern we hear is: ‘How is this going to work once OTS is gone?'
How will some of our larger, more strategic market development initiatives - like rubber-modified asphalt, consumer rebates, and our research and development branch - be delivered in an environment where you have multiple, competing programs? That's not clear. It's also not clear what the obligations will be around this. Because the government hasn't yet written the new regulations. But that will come, and they are starting to consult on it.
From the government's perspective, they are not trying to lay out a prescriptive path. They are trying to give choice to the Michelins, the Goodyears, the Toyotas and other tire producers. At a high level, that's not a bad thing. Giving them choice in terms of how they meet their obligations is a tough thing to argue against. I think they should have a choice.
I think the concern from OTS's perspective is that we've been a highly successful program with essentially 100 percent diversion. We've doubled recycling capacity, tripled manufacturing capacity, focused on developing domestic markets, and all through that we've also reduced our costs significantly. Our fee on passenger and light truck tires is the second lowest in the country, and over 40 percent reduction over the last four years. We've reduced our fees on other categories like commercial truck and off-road tires by almost 6 percent over the last couple of years. And so, I think it's fair to ask the question: ‘What problem are they trying to fix here?'
I think the government's view is that if the producers, the tire producers, tire stewards, decide that they want to create one company on the other side to which they'll all subscribe, that option is not precluded to them. I think what they may have underestimated, although they're getting more immersed in it now, is the degree to which going from OTS to that new framework might create uncertainty and disruption in the market.
But, that is the nature of this beast. Any time you're going to alter framework legislation, there's going to be change that's required. Our goal and the tire stewards' goal will be to make sure all the best things about the current used tire program are preserved and perpetuated going forward. RPN
This article was originally published in Recycling Product News, September 2017, Volume 25, Number 6.