Carbon Black going ‘Green’
Black Bear Carbon produces carbon blacks through pyrolysis using end-of-life tires as feedstock
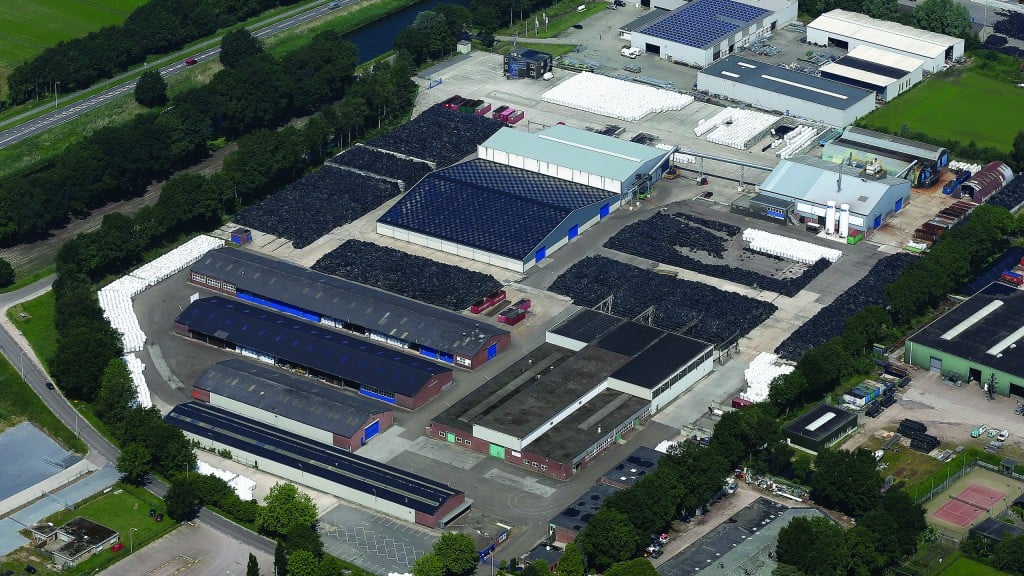
Currently, the world faces an immensely problematic waste stream: tires.
Every year approximately 2.4 billion tires are produced on a global scale. Additionally, with approximately 1 billion tires reaching the end of their life annually, millions of tonnes of tires become waste that is incinerated, dumped or landfilled in many places in the world.
These ‘solutions' do pose not only a major environmental concern but also a health risk. When tires are landfilled, they can become breeding grounds for malaria-bearing mosquitos, with still-standing water accumulating in the tires providing perfect conditions.
Moreover, 4.5. million tons of carbon black, which can be re-used, is squandered.
Carbon black can be used in many applications, including: as a reinforcing agent in new tires or a pigment in coatings and inks. Traditionally, most carbon black (about 95 percent) is created through burning crude oil, using the ‘furnace' process, with an average input of 2.5 litres of oil to manufacture 1 kilogram of carbon black.
Current production of carbon black uses ± 31.751.465.900 litres of oil and is highly polluting, emitting more than 35 million tons of CO2 per year, to fulfil the global annual demand for carbon black of ±14 million tonnes per year.
The bulk of this carbon black is consumed in the tire industry, and is also used in various other industries (as illustrated in Figure 1, top right).
The Black Bear alternative
Black Bear Carbon, based out of the Netherlands, produces high-quality carbon blacks through an innovative pyrolysis process using end-of-life tires as feedstock. Pyrolysis uses heat in the absence of oxygen to decompose granulate to yield volatile gases (10-15 percent), oil (45 percent) and carbon black (40 percent).
The gases can be used to generate electricity for the pyrolysis process, and with every plant, Black Bear saves more in CO2 emissions yearly than one million trees can consume.
Additionally, the carbon black that is produced by Black Bear is comparable or superior to various carbon black grades for numerous applications, besides having unique product characteristics and distinctly low PAH values, making the product safe for human touch and food applications.
This ‘green' carbon black can be used for various applications in polymers, plastics, and rubber manufacturing and acts as a sustainable alternative to products existing in these industries. Plus, the product quality has been verified by various major companies in all applications through an extensive testing process.
In Nederweert, the Netherlands, the first production plant is now operational and commercial shipments have started. With the success of the first plant, Black Bear hopes to expand on this success by the roll-out of more factories worldwide. In fact, there are enough waste tires in the world to build 1,200 plants of roughly the same size as the Nederweert plant.
Applying a ‘green' carbon black circular economy business model has great advantages for companies active in tire processing and rubber manufacturing - for example, by reducing waste processing costs, use of and expenditure on resources and by drastically reducing negative environmental impacts.
"Tens of millions of tires are burned annually, wasting massive amounts of valuable carbon black," says Martijn Lopes Cardozo, CEO, Black Bear Carbon. "Petroleum is used to produce new carbon black. With Black Bear Carbon we have shown that circular business models are the way to go, and we hope that other business and industries will follow suit to transition to a circular economy."
This article was originally published in Recycling Product News, Volume 25, Number 4, May/June, 2017.