Maximizing the Energy Production Capability of Anaerobic Digestion Plants
D:MAX dewaters and classifies inorganic material allowing for maximized potential for biogas creation from anaerobic digestion
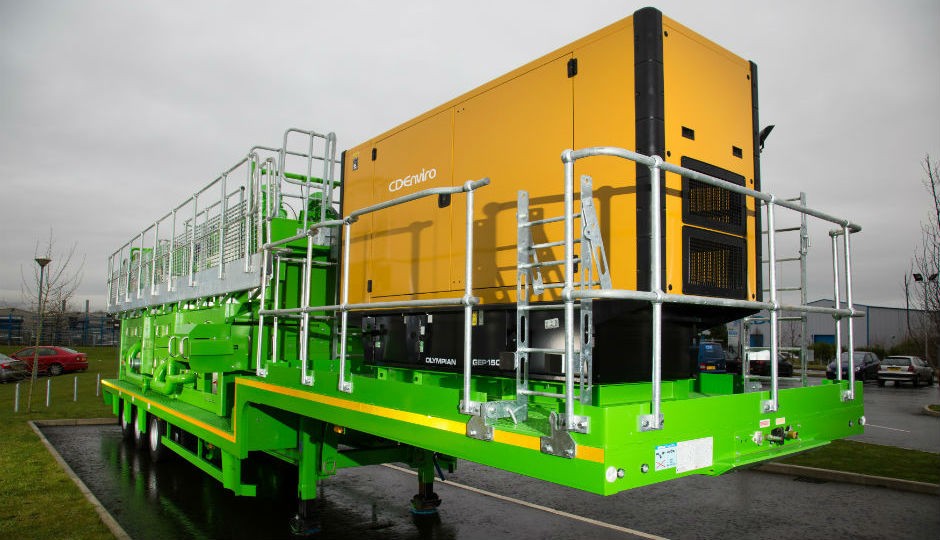
The cost of establishing an AD facility is widely accepted to be one of the main barriers to more widespread adoption of anaerobic digestion. The main adoption of AD technology has been in the wastewater treatment sector to date although there is ongoing work to expand adoption in the agricultural sector. Given the relatively high costs associated with setting up an AD plant it is essential that once operational the plant is optimized for maximum performance – which in this instance is measured by the volumes of biogas which can then be used in the generation of heat and power.
In order to ensure the anaerobic digestion plant works at maximum efficiency it is essential that the feedstock to the AD vessels is as close to 100% organic material as possible. If this is not the case the available area within the vessel is reduced, thus reducing the capability of the plant to produce the highest possible volumes of useful biogas. There are several types of inorganic material that can be removed from AD vessels in order to improve efficiency.
Mineral material – stones, pebbles, sand – serves no useful function in an AD vessel and simply builds up in the tank, thus reducing the potential for production of useful biogas. In addition, this material also causes unnecessary wear on pumps and pipework leading to increased maintenance costs and reducing plant availability.
Plastics and packaging also need to be removed – these are more commonly found in applications where food waste is being delivered to an AD plant. Plastics can rise to the surface of the AD vessel and this creates an insulating layer which prevents methane from being harvested. As methane is the required output from the AD plant this reduces the return on investment capability of the operation.
Glass from bottles and jars – also more commonly found when food waste is the feedstock to the AD plant.
In Sewage Sludge digesters material there can be a build-up of rag, litter, ear buds, baby wipes and sanitary towels.
If any of this material is building up inside an AD vessel, it can be removed by introducing CDEnviro's D:MAX system. Once fluidized, material can be delivered directly to the D:MAX which will dewater and classify the inorganic material allowing for maximum potential for biogas creation from an anaerobic digestion plant. While the above option will allow users to systematically remove the inorganic material from AD vessels, the best solution is to introduce a D:MAX or PRO:DEC system in-line. Feedstock is then processed through one of these units prior to delivery to the AD vessel, allowing for the effective removal of inorganic material in the most efficient way.
One of the main issues with having to clean out the digesters is that the micro-organisms need to be re-seeded and it can be three to four months before the AD plant is back to full production. This represents a huge cost and investment. A system which eliminates this ensures that composters are maximizing return on investment in the AD plant by ensuring maximum plant availability.
According to CD Enviro, by introducing their waste handling and classification systems to intercept the feedstock before delivery to the anaerobic digestion vessels, users will maximize availability of their AD plant and thus maximize the potential for production of useful biogas. This approach also serves to eliminate unnecessary downtime as there is no longer a requirement to shut down the plant to facilitate removal of the inorganic material.
Anaerobic Digestion (AD) is the process whereby bacteria break down organic material in the absence of air to produce a biogas containing methane. The products of this process are biogas – principally methane (CH4) and carbon dioxide (CO2).
The biomass is delivered to a sealed vessel (or a series of vessels) where naturally occurring micro-organisms digest the biomass which produces the methane rich biogas. This biogas is captured in a Combined Heat and Power Unit (CHP) and can subsequently be used in the generation of renewable heat and power – reducing the reliance on fossil fuels and subsequently reducing greenhouse gas emissions. The material left behind in the digester is rich in nutrients so it can be used as a fertilizer.
There are many forms of biomass that are suitable for anaerobic digestion – food waste, slurry and manure as well as crops and crop residues. Although anaerobic digestion has been used since the late 1800’s it has been more widely adopted in recent years as a result of the focus on renewable energy.