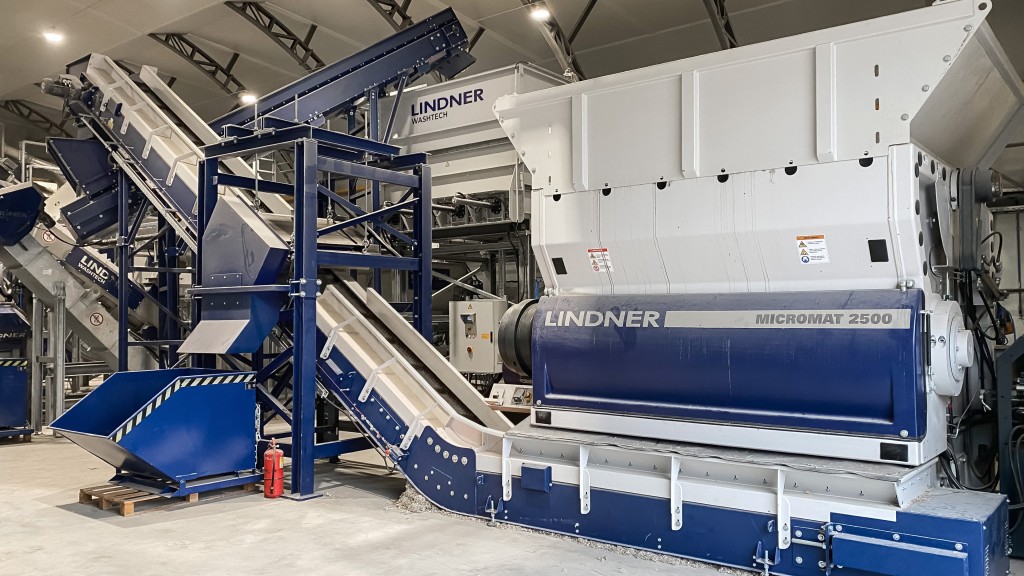
Since 2001, the Lithuanian recycling company Virginijus ir Ko in Plunge has been collecting, sorting, and processing recyclable materials from trade, commerce, and agriculture. In 2023, the company commissioned a Lindner Washtech facility to turn big bags into high-quality pellets that can then be reprocessed back into big bags as part of the circular economy.
The Virginijus ir Ko recycling plant in western Lithuania has been active in waste management and recycling for more than 20 years, processing around 35,000 tonnes of potential recyclables annually. The majority of the materials to be recycled are waste products from agriculture.
"We have been working with materials from the agricultural sector for years, including agricultural film and large amounts of big bag waste. Back then there was no recycling facility for big bags in Lithuania or nearby countries. That's what motivated us to invest in this area and recycle these materials locally. However, we soon realized that recycling big bags is a very complex issue," explains Virginijus Skublickas, managing director at Virginijus ir Ko, "but we didn't give up and found the right partner for this task in Lindner Washtech."
Big bags are usually made of polypropylene (PP) and are tear-resistant, hard-wearing, and cut- and scratch-resistant – these are all properties that make the recycling process very demanding. The entire process chain must be precisely coordinated to keep the fine particles content, which would result in material loss, as low as possible and to guarantee a high level of material purity.
"As with many plastic recycling processes, the first shredding stage is the most important for big bag recycling. Thanks to its robust drive and safety clutch, the Micromat series shredder is particularly powerful and resistant to non-shreddables. The Micromat's cutting system is also specially designed for big bag shredding. Special knives and an easily adjustable counter knife ensure high productivity," says Tomas Kepka, head of sales, Eastern Europe, at Lindner Washtech GmbH. "In the subsequent process steps, the main focus is on gently removing any remaining impurities and drying the material."
The ‘Rafter‘ pre-wash system from Lindner Washtech, with its speed of approximately 60 rpm, is ideal for removing stones and sand. Up to 90 percent of all dirt and contaminants can be extracted in this first washing step. In the subsequent processes, the pre-washed and opened big bag flakes can be processed much more gently, avoiding material losses due to fine particles.
Following the cleaning, the material must be prepared in the drying unit for the extrusion process.
"When drying big bag materials, we use the mechanical dryer from the Loop Dryer series. It is equipped with special tools that prevent high stress on the material due to friction. The dryer also has a frequency converter so that the speed can be adjusted and controlled accordingly," explains Kepka.
The big bag facility at Virginijus was commissioned in 2023 and has now been producing high-quality PP granulate since. The entire facility consists of a shredding and washing system, a process water treatment system, and an extrusion system with odour decontamination