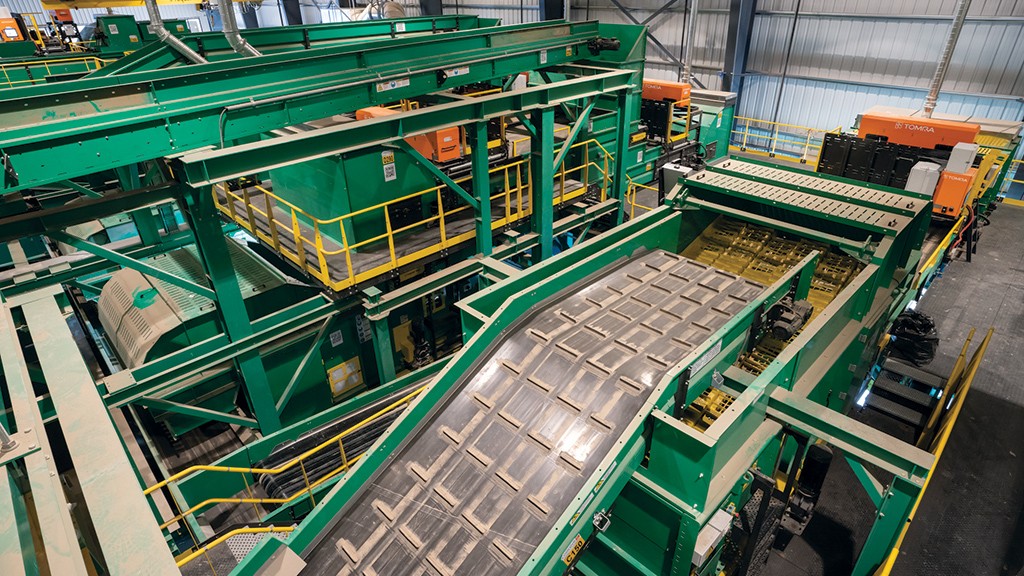
In recent years, there's been a trend of replacing screens with ballistic separators. Ballistic separators come with a major advantage: They do not have any stars or discs. This means they do not wrap like traditional disk screens and they do not incur wear that requires costly star changes. But ballistics have their optimal place, and trying to employ them at certain junctions in your system could be a mistake.
How do you avoid that mistake? First, let's clarify how ballistic separators work. They have long paddles that undulate at alternate intervals to separate 2-dimensional materials from 3-dimensional materials. 2D materials walk up the paddles and fall over the screen, and 3D items bounce back and off the screen onto a conveyor. Plus, you can separate out fines as well by adding holes to the paddles. Ballistics seem to perform the same function as a starscreen, but without the wrapping and the star replacement. Sounds like a win-win, right?
Potential risks associated with ballistic separators
The catch is that ballistic separators are picky when it comes to their "diet." They are very sensitive to the composition of the materials they are fed and prefer a mix that contains a high percentage of 3D materials (bottles and cans) and a low percentage of 2D materials (the last bits of fibre and film). They do not perform well with the opposite ratio. When a high percentage of fibre hits a ballistic screen, there is not enough agitation created to properly clean the fibre from prohibitives. For this reason, putting ballistic separators too early in the system is a risk. Big piles of fibre, film, and other lightweight flattened items can overload the screen and compromise its separation ability.
To run the system when a ballistic separator is overloaded and struggling like this, the operator has two choices:
- Slow the system down to lighten the load.
- Send the 2D fraction that carries over the struggling screen directly to residue, because it's a jumble of unsellable paper mixed with film, bottles, and cans.
Most operators don't have the time to slow down their systems and lose capacity. So, most will go with option two.
It's tempting to use ballistic separators early in a system or to install multiple ballistics - there's no wrapping and no stars to change. In efficient system designs, a larger cut of the materials is taken early on in the system with a 440 non-wrapping screen (with larger shafts). Due to its resistance to wrapping, this screen offers the same benefits of less wear and tear, fewer star changes, and increased production. Plus, it is specifically built to handle the larger amounts of 2D materials that are present at the front end of a system.
Proper placement of separation devices
Once the 440 screen removes a high percentage of the 2D materials, operators should examine the amount of fibre still left in the back and under the remaining 3D stream. Is the volume of remaining fibre small enough for a ballistic to handle, or would fibre be more effectively removed by an intelligent device such as an optical sorter, robot, or human?
At this stage, most MRFs need an intelligent separation device (in this case an optical sorter) to recover the remaining fibre. This is where a screen's limitations start affecting the sort line. Sure, recent developments in screening technology like ellipticals and non-wrapping screens have alleviated some of the worst problems related to contamination. However, think about everything a starscreen or ballistic separator still cannot do. A ballistic cannot tell the difference between a milk jug or a 3D box. It cannot tell the difference between a piece of fibre and a super thin-walled PET water bottle that has been flattened. And, it definitely cannot tell the difference between a piece of newspaper and a film grocery bag. Anything flat is going over the screen, and anything 3D is bouncing off.
Placing a ballistic at this juncture in the system will likely result in two very imperfect streams: the overs being, yet again, a mix of fibre, flat PET, flat aluminum, and film, and the unders being a mix of containers and 3D fibre. Little is accomplished here. The materials will not be in any better of a position than before, and will need significant cleanup on both sides to achieve optimum recovery of all materials.
On the other hand, an intelligent separation device placed at this juncture in the system can make significant progress in sorting these materials. Because optical sorters have the capability to recognize items by shape, colour, or specific material composition, they are essential in dealing with the highly variant and problematic materials in today's stream. An optical sorter placed directly after a 440 screen can strategically eject the fibre that has made it into the container stream without letting film and flattened containers go with it. Opticals can identify and eject all types of fibre at this point and send it to a quality control line.
After the optical sorter ejects the fibre remaining in the container stream is where the elliptical screen comes in to do what it is good at: "polishing" up your container line by removing the last bit of remaining film and fines. This screen is perfectly designed to walk any remaining film up and over its paddles while simultaneously screening out 2-inch minus materials via holes in those paddles. Remember, it needs a higher percentage of 3D materials to function properly.
When it is in the right place, it's wonderfully efficient. Those 3D items will bounce back and off the screen onto a conveyor headed for container separation. Now you will have a container stream with homogeneous materials that are able to spread out on the belt, unencumbered by floating paper and boxes. You'll get more accurate performance from your optical sorters, robots, and manual sorters, and you will see fewer valuable containers and fibre lost to residue.
The bottom line
The importance of the placement of new equipment cannot be stressed enough. You cannot simply drop a new piece of equipment wherever you think is most convenient and expect it to work seamlessly. If the placement choice is the wrong one, it will greatly affect the entire plant throughput, the quality of your fibre, the fibre capture rate, and the quality of the 3D containers passing to the container sort.
Make sure you physically audit your inbound material stream constantly. Be specific: Take pictures, note sizes and shapes, and study the trends and changes that could affect your equipment placement. If you decide to upgrade from outdated screens and are enticed by the ballistic design, make sure your supplier knows the best strategy for applying the latest screening technology. Sometimes what sounds too good to be true is exactly that. Your supplier should be realistic in assessing the inbound materials that you have and honest about the retrofit layout you need to accomplish your goals. Otherwise, you could end up spending money on a retrofit that solves one problem but perpetuates another.