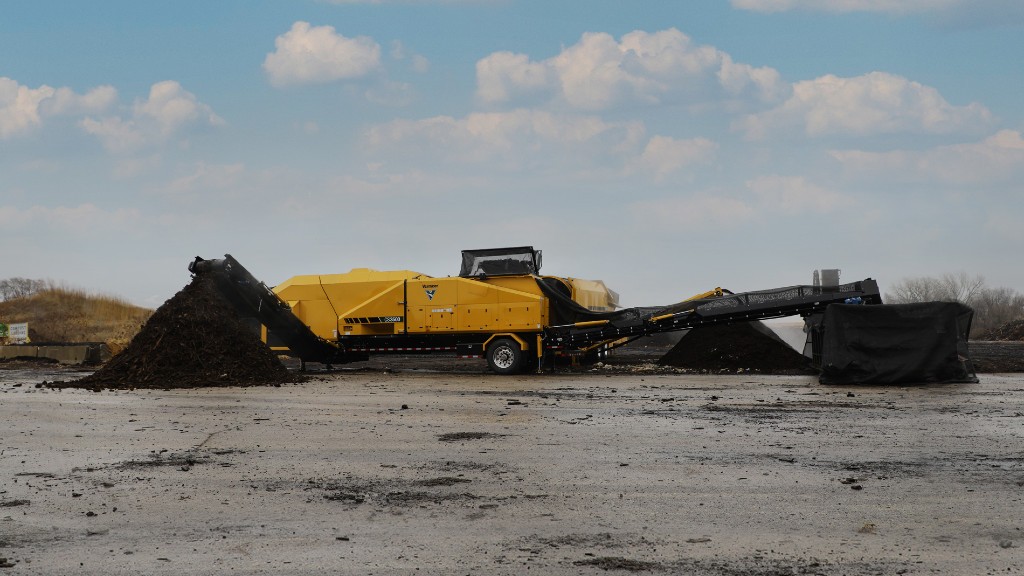
Vermeer has introduced the CS3500 contaminant separator that helps minimize the labour involved in the organic waste recycling industry. Using the combination of grizzly screens, shaker tables, vacuums, an air manifold, and an optional magnetic pulley to remove a wide range of contaminant types, the CS3500 helps recycling operations produce high volumes of quality compost and mulch.
"Organic recycling is important to help keep materials that can be used to make compost, soils, and mulch out of landfills," says Jay Van Roekel, product manager for Vermeer Environmental. "The challenge most recycling facilities face is separating nonorganic waste and other materials that do not break down from their end products. Plastics and other materials are often introduced early into the recycling process, and there have not been effective ways to remove them afterward. Therefore, Vermeer developed the CS3500 contaminant separator. Now, recycling operations can get the most from the material they are working with to produce more end products."
How the CS3500 contaminate separator works
Stage 1: Incoming material from screening equipment is loaded onto the CS3500's nine-foot (2.7-m) high, 36-inch by 60-inch (91.4-cm x 152.4-cm) infeed shaker table. The deck's pyramid design spreads incoming material out across the width of the table before it passes through an adjustable grizzly screen that removes large debris.
Stage 2: After material passes through the grizzly screen, the contaminant separator's infeed belt transports it to the top of the machine, where it drops onto a vibrating shaker table. During the fall, an infeed vacuum removes lightweight debris from the material.
Stage 3: The shaker table agitates the material as it travels across the surface to free the remaining contaminants. In addition, the CS3500 air manifold blows across to the table to remove bulky, lightweight debris like styrofoam and plastic bottles that a vacuum cannot pick up.
Stage 4: At the end of the shaker table, a second organic vacuum pulls the remaining light contaminants from the material as it falls onto the discharge conveyor belt.
Optional stage 5: Users can add a magnetic pulley to the front of the discharge belt to remove small ferrous metals, like nails and screws, from the end product.
Contaminant removal: All contaminants removed in each stage are rerouted to an adjustable trash conveyor. This flexible conveyor adjusts for loading containers, trucks and stacked piles.
Machine design
A 74-hp (55-kW) DEUTZ diesel hybrid electric engine powers the Vermeer CS3500 contaminant separator. Operators also have the option to run the machine directly from an external power source. During operation, the CS3500 maintains a low operator sound level of 79Hz.
The machine's full-function remote control allows operators to make operating adjustments, log machine data, and diagnose fault codes. Users can also make adjustments from the full-colour seven-inch (17.9-cm) touchscreen on the machine. The CS3500 comes with Vermeer telematics for monitoring engine hours, location, geofencing, and over-the-air-programing (OTAP).
The CS3500 is designed with service in mind, with optimal access machine service points. Also, the infeed is covered, and the trash conveyor is covered and curtained to help contain contaminants during operation.