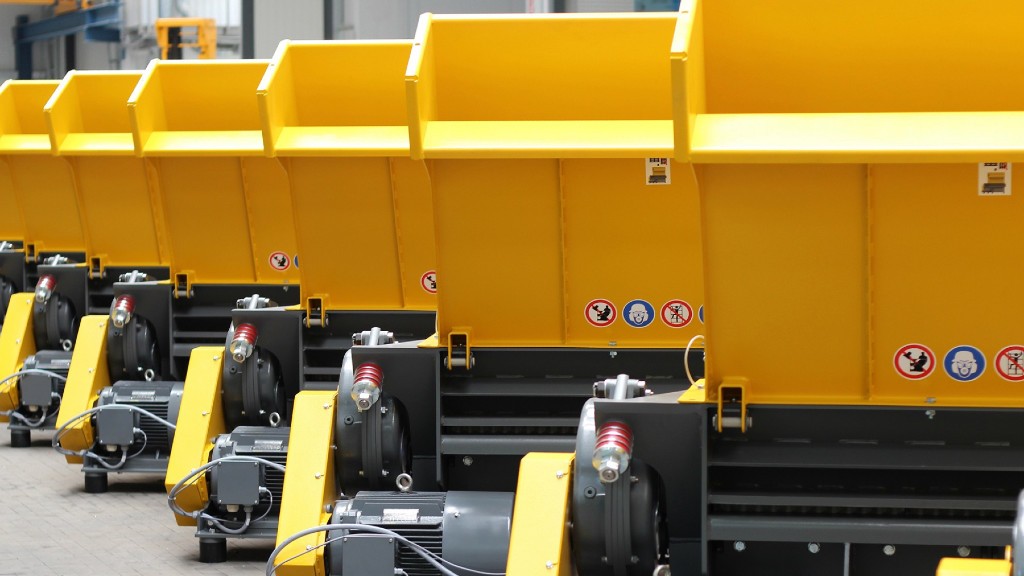
For waste and recycling professionals within the sector, machinery – in its many guises – often forms the backbone of their operations. And when it comes to specifying the requirements of a new industrial shredder, price is almost always at the top of the priority list. But how much should an industrial shredder really cost?
Outlining business objectives
The first thing for sector professionals to consider is that the cost of an industrial shredder is going to be very different to that of commercial shredding technology that's intended for use in an office. Industrial machines refer to heavy-duty equipment that's capable of tackling an array of different and difficult materials – often at high volumes – to achieve what are typically very specific objectives.
Therefore, before investing in any kind of plant equipment – be that an industrial shredder or otherwise – operators should dig into the how and why behind the investment. What benefits will the new machinery bring to current operations?
It's only once these aims have been outlined that the search for the right tools for the job can begin effectively.
It may sound obvious, but the best place to start is with the type of material the organization needs to shred and why. This could be anything from metals, plastics, medical waste, and high volumes of documentation to mattresses or tires.
Outlining the waste streams that will be fed into the machine will help to determine which models are appropriate for the job in hand, but the kind of price-point a firm is looking at.
Once a model and a cost are given, efforts should be made to break down such figures, beyond the more obvious price tag. This can help to pinpoint the return on investment and, ultimately, how long the machine may take to pay for itself.
In truth, operators need to know that their investment will boost operational performance not solely in the present but in the long term too – especially when it comes to maximizing throughputs, capacity, efficiency, and uptime. This helps to ensure the shredder is a value-adding asset within a facility.
When operators start to build a business case for industrial shredders, this is when the numbers matter even more. These are high-value assets which can transform what a waste, recycling, or alternative fuel specialist can do. They're not insignificant investments – and that's why they have to be right.
Looking beyond the initial outlay
When evaluating the cost of such machines, it's important to also consider the ‘hidden' variables that influence the true financial commitment required to run the equipment. This includes the ongoing fuel consumption and energy efficiency and how much will it cost to run the shredder.
Further to this, it's crucial to consider whether the wear costs include the cost of servicing and maintenance, spare and wear parts, and unplanned downtime.
Operators should also think about the speed and quality of the vendor's user support, as well as the availability of parts that will inevitably be required. Could the operator afford to keep some parts in stock, so the capacity of its facility is never jeopardized? Could the shredder's cutters be rebuilt when worn, so operators don't have to buy new?
It's vital to ask these questions so that a plant isn't left stuck if anything unexpected happens further down the line.
These factors, and more, will all affect the whole life running costs of an industrial shredder, which means a seemingly affordable initial purchase could soon not be the case. Conversely, slightly more ‘expensive' equipment can quickly shape up to be a far savvier investment – with shorter payback periods, either due to the revenue streams achieved from the sale of on-specification output material, and/or the energy savings recouped from electric-driven machines.
With so many choices on the market, it can sometimes feel like a daunting and overwhelming task for businesses to source the industrial shredding equipment that's right for them. But when it comes to cost, while it's certainly an important driving factor, it shouldn't be viewed in isolation – otherwise, this could jeopardize the ongoing financial performance of not just the machine, but the organization too.