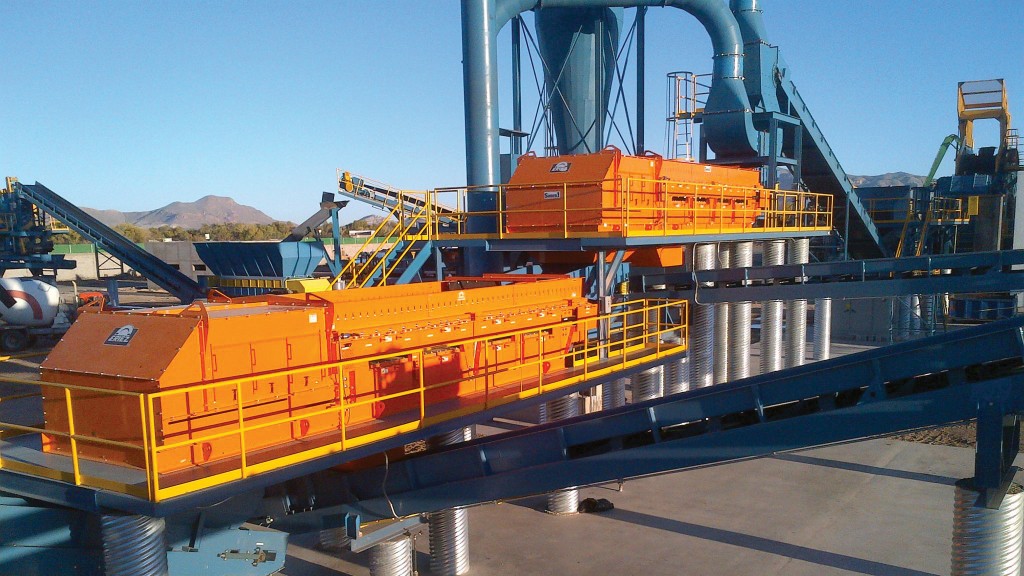
A method for upgrading shredded scrap has been developed and optimized using the Eriez Shred1 ballistic separator coupled with magnetic separation equipment. The resulting upgraded shredded scrap will lower the amount of copper-bearing material (typically less than 0.2 percent) and increase the grade of the scrap. This is accomplished by removing the misplaced non-ferrous materials typically found in shredded scrap, thereby increasing yields in the steelmaking process.
This process allows shredder yards to provide a more desirable scrap to steel mills seeking a low-copper scrap. These steel mills gain a competitive cost advantage by using less pig iron/DRI (direct reduced iron/sponge iron) and pre-consumer scrap, and more low-cost, low-copper shredded scrap in Electric Arc Furnace (EAF) sheet steelmaking.
Regular shredded scrap provided to steel mills ranges in copper content from 0.26 to 0.56 percent, depending on the infeed material to the shredder and the downstream process after the shredder. After assays of shredded scrap from many different shredder sites, the determination is that the nominal copper content of shredded scrap provided to a sheet steel mill is usually about 0.31 percent copper.
Sheet steel mills use a blend of pig iron, DRI, and pre-consumer scrap. Typically, only about 25 percent of lower cost shredded scrap is used in the blend, with the remaining 75 percent consisting of a mix of the higher-cost pig iron, DRI and pre-consumer scrap. With the higher cost of pig iron, DRI, and premium scrap, combined with the limited availability of these commodities, using a higher percentage of low-copper shredded scrap will allow steel mills to reduce the cost per ton of steel produced.
Processing the scrap
In a scrapyard, the Shred1 ballistic separator is positioned after the primary scrap drums and a shredder, placed just before a picking station. Shredded material is fed to the ballistic separator and accelerated up to 1,000 feet per minute. A unique magnetic element at the end of the separator attracts the more magnetic pieces of steel and drops them behind a splitter. The magnetically stronger steel is typically a bit smaller in size and has more points of contact on the magnet with less non-magnetic material entrapped. This is the low copper stream (referred to in this paper as material #1) and accounts for about 75 percent of the overall material stream. This material is conveyed to the stacking conveyor with no further action required.
The material that is less magnetic - usually heavier pieces that have non-magnetic material entrapped - is more affected by the ballistics of the belt speed than the attraction of the magnet. This material is presented over a splitter, which is then discharged from the separator and conveyed to a polishing drum. This less magnetic material, which is known as the copper concentrate, represents the remaining 25 percent of the feed.
Copper concentrate (referred to as #2 material) is presented to a magnetic drum with a reduced magnetic field or a polishing drum. This drum is set to "cherry pick" the best ferrous of the #2 material, which is liberated from any copper-bearing materials. This material, typically making up 10-15 percent of the #2 fraction, will be blended back to the #1 stream and sold as low copper shred, increasing recovery.
After the polishing drum, the #2 material is presented to a picking station where copper-bearing materials and any non-ferrous material are ready for manual picking. This material can be sold to mills that do not require a low-copper product or sent for further processing to advance the liberation of copper from steel.
Testing materials
Material was collected from multiple scrapyards and processed under a Gamma Tech analyzer to verify copper content of the feed material. With over 1,000 tons of material, the average copper content was 0.29 percent.
The Shred1 ballistic separator was set to produce a 75/25 split of material. Seventy five percent of the material would be the low copper #1 material, and the remaining 25 percent would be the copper concentrate #2 material. After processing the 1,000 tons on the Shred1 ballistic separator, the #1 fraction was sent back under the analyzer for assay where copper content was recorded at 0.16 percent. This represents a significant reduction in copper.
The #2 shred was sent under the polishing drum where an additional 10 percent of shred was recovered. This product was also sent under the analyzer for assay. The results showed the copper content was recovered at 0.18 percent. This shred can be blended back into the #1 material without adversely affecting its copper content, all while increasing recovery.
The #2 material not recovered at the polishing drum was conveyed to a picking station where any copper-bearing materials and/or non-ferrous material can be manually removed. The reduced flow to the picking station (15 percent of the infeed) requires fewer pickers. The decreased feed allows pickers to work more quickly and efficiently since the material is lightly burdened and copper-bearing materials are easy to spot. Copper picking at a typical yard averages 5 to 7 pounds per ton of shred. After installation of the ballistic separator, the copper picking will typically rise to 12 to 14 pounds per ton of shred.
By installing a ballistic separator and a polishing drum, scrapyards can now provide premium low-copper shredded scrap to steel mills while reducing labour and increasing copper pickings. In many instances, the lower copper scrap commands a premium of more than $40 per ton.
Mike Shattuck is the recycling market manager at Eriez.