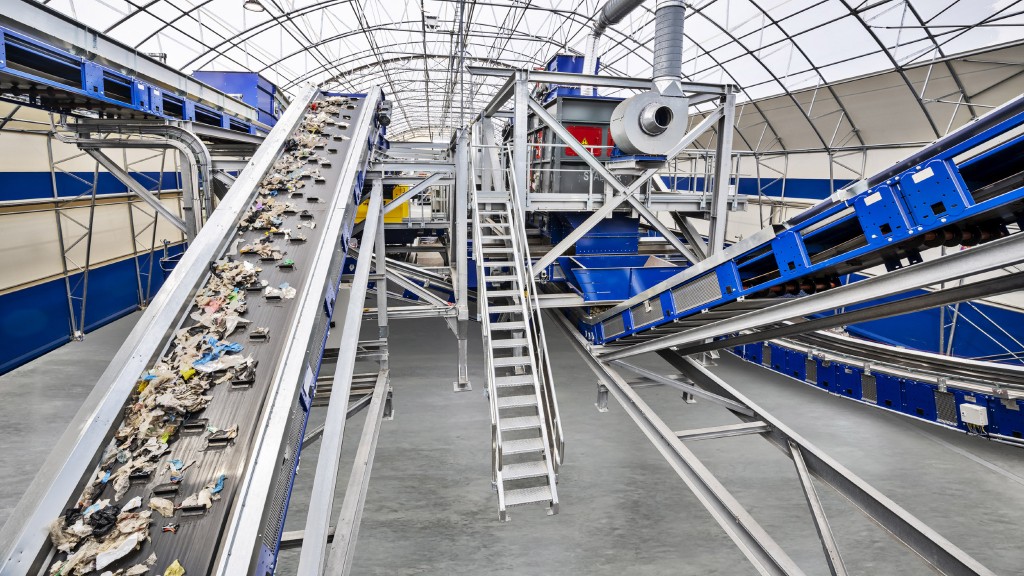
STADLER inaugurated its Test and Innovation Center in Krško, Slovenia, in 2020 to deliver user demonstrations and training, as well as conduct research and development activities. The 1,200 square metre temporary structure has since been extended to 2,000 square metre and houses most of the machines needed to demonstrate the complete sorting process. The machines are laid out within the facility in this sequence so that it is possible to conduct tests on individual machines or on the whole process as it would be implemented in a sorting plant.
The full sorting process in action
The sorting line, which has a capacity of five t/h of light packaging material, is set up to carry out six sorting processes: dosing with a screw doser, label removal – which can be bypassed with a moving conveyor belt – followed by ballistic separation for 2D, 3D, and fines. Reversible and movable conveyors below the ballistic separator determine which 2D and 3D fraction proceeds to the magnetic and non-magnetic separators. The optical separation process was recently upgraded with a second NIR sorter so that 2D and 3D fractions can be sorted in parallel, or either fraction can go through a double extraction in the two machines. A further upgrade is planned for 2022, with the addition of the latest TOMRA AUTOSORT with NIR technology and STADLER's new PX acceleration conveyor.
The value of user tests
The Test and Innovation Center is a valuable tool to ensure that the design developed for a user will deliver the desired results with their material.
"Testing our customer's material enables us to see how to plan our technology," says Nejc Božič, STADLER project manager. "We can also test new machine settings for a specific input and set up the unit for a specific function or material from the beginning. We can test for a variety of parameters: most often we measure throughput, recovery and purity, but also energy consumption of individual units or the whole plant, compressed air consumption, or data from the different sensors. We also run tests to show our customers how the designed plant will work for them and deliver the desired results."
A valuable resource for research
The ability to perform tests on both individual machines and the full process, together with the expertise of STADLER's team at the Test and Innovation Center make it a valuable resource for research projects.
"These tests enable us to assess different aspects of the process, such as the effect of throughput rate and input composition on machine performance, or to research the potential of machine parameters and the machines' digitization," says Dr. Bastian Küppers, engineer for digital business development at STADLER. "They give us insights into the potential and limitations of our machines and our plants, enabling us to improve our process and plant designs."
The centre has recently been conducting research into adaptive machine control, which is becoming increasingly relevant with the growing digitization of plants.
"Adaptive control of the processes enables an improved and more stable sorting performance. This can lead to higher purity levels, yields and throughputs, while keeping downtime to a minimum," explains Bastian Küppers.
STADLER's Test and Innovation Center is increasingly in demand for participating in research projects such as EsKorte. This project, in collaboration with Montanuniversität Leoben and RWTH Aachen, is looking into the development and testing of a sensor-based material flow monitoring system. Multiple tests were conducted at the centre for the project.
"It is great to have the possibility to simulate characteristics of real sorting plants without being restricted by the plant operation. The collaboration with STADLER has thus been enriching for our research work in the field of improving the performance of plastic packaging waste sorting plants," says Dipl.-Ing. Sabine Schlögl, chair of waste processing technology and waste management, Montanuniversität Leoben.
STADLER has also participated in a research project aiming to recover waste paper from mixed waste streams. The members of the EnEWA project – Universität Siegen, RWTH Aachen University, LEIPA Group, PROPAKMA, TOMRA, and STADLER – set clear objectives: increase recycling rates in paper production and reduce primary energy requirements and CO2 emissions. STADLER is developing a concept for a sorting plant for processing paper fractions from lightweight packaging, residual, and industrial waste, so they can be used as raw material to produce new paper. The validation process will be done through trials conducted at the test centre. This project received the European Paper Recycling Council Award 2021/22 in the "Innovative Technologies and Research & Development" category.
"Test results can have a direct impact on process designs, as our machines are pushed to the limits repeatedly," adds Bastian Küppers. "For example, the results of the tests we performed for the EsKorte project have already allowed for significantly improved sorting performance in one of our customers' plants. More generally, I believe that through adaptive plant control we will be able to improve further the quality of a number of product fractions in our lightweight packaging plants. Also, our findings in the EnEWA project can help us streamline today's processes and enhance sorting performance, achieving higher purity and yields."