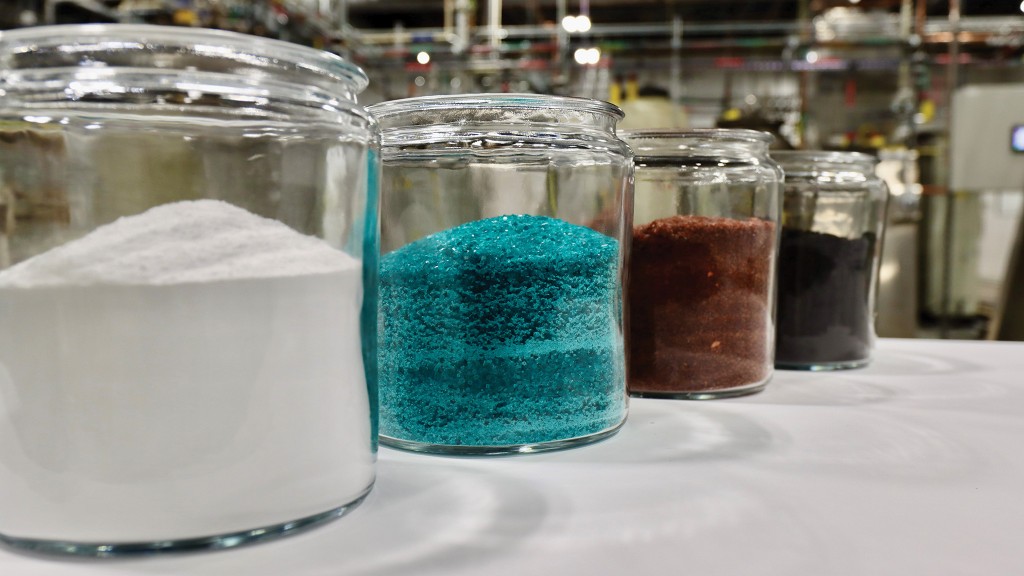
There exists a general perception that a product made with recycled materials is not as good as one made with raw materials. When it comes to recycling electric vehicle (EV) lithium-ion batteries, Ascend Elements is changing that view.
I met with Roger Lin, Ascend Elements vice president of Global Marketing and Government Relations, to discuss his company's recycling technologies that are cost effective, environmentally friendly, and yield the highest-quality materials.
Arturo Santiago: Can you give me a brief history of Ascend Elements?
Roger Lin: Ascend Elements is an engineered materials company that makes lithium-ion battery materials from recycled lithium-ion batteries. It was founded in 2015 under the name Battery Resources. We've been working on this process for quite a while. The original work was done at Worcester Polytechnic Institute, WPI, here in Central Massachusetts. Initial patents were filed in 2012 on this unique, innovative, and efficient process to turn spent lithium-ion batteries back into new battery "active materials." Right now we're on the cusp of scaling up the technology with what we call Hydro-to-Cathode and are putting in large-capacity commercial operations in the United States. The first phase is in Covington, Georgia, which, once it's operational, will be processing 30,000 metric tons per year of spent lithium-ion batteries and scrap. It's big. And it has to be big because there are a lot of batteries that will be coming at us.
AS: Where do you get your materials from?
RL: The two major sources of input for our Covington facility will be end-of-life lithium-ion batteries and lithium-ion factory scrap. The most obvious source is batteries from electronics devices, electric vehicles, or other battery-powered products which have reached their end of life. But the other lesser-known source we're getting batteries from is manufacturing scrap from gigafactories. These gigafactories produce a fair amount of scrap material. It's all the stuff that doesn't meet specifications during the manufacturing process. That all needs to be disposed of and handled in the right way. We're going to be taking that scrap and returning it back into the battery supply chain to make it a truly circular manufacturing process.
Somewhere between 8 and 10 percent of all the output of a lithium-ion battery factory ends up as scrap. That is going to be the majority of our feedstock for a number of years. But later in this decade, the end-of-life batteries that are coming off EVs that are being retired or scrapped will begin to overtake the manufacturing scrap side.
The materials we process are a little different depending on what stage they're coming out of. Manufacturing scrap takes many forms since it spans the entire production process of lithium-ion cells. Cells are comprised of cathode active materials and anode active materials coated onto either aluminum or copper metal foils. These foils are stacked or rolled up into an electrode stack or a jelly roll. They are then packaged inside a pouch or a metal can. The can is either a cylindrical metal can or a rectangular shaped can we call a prismatic. These are then formed into lithium-ion cells. Those cells then get turned into batteries by connecting them in series or in parallel, or a combination of both. That battery is then packaged in a strong housing, which then ends up going into the electric vehicle.
At any point in the above process, something can fall out of specification and be scrapped, and thus need to be recycled.
AS: What is the Hydro-to-Cathode process?
RL: This Hydro-to-Cathode process is the most efficient way to turn a lithium-ion battery that's reached end of life back into the cathode active material, which is probably the single most important component of a lithium-ion cell. Not only does the cathode active material define the lithium-ion battery type - NMC, LCO, NCA, LFP etc., it is also the single most valuable part of a lithium-ion cell, representing about half of the total cost. This is why it is so important to a lithium-ion battery.
Our process takes that end-of-life battery and transforms it into brand-new cathode active material - it's essentially a grave-to-cradle process, where we're taking it at the end of life and returning it back to a new life. The path that we take is the shortest and most efficient, and thus the most economic path back to that critical cathode active material. The output of our Hydro-to-Cathode process is indeed the cathode active material, and it is not only more sustainable, less carbon intensive, and less polluting, it is also more economic.
So by making that as efficient as possible, and as high-value as possible, we're hoping to drive recycling rates for lithium-ion batteries, not just EVs, but for all lithium-ion batteries, up to as close to 100 percent as we can. Because when the recycling is economic, then the recycling becomes inevitable. It will happen.
When the batteries come in, whether it's electrode scrap like coated foils that come out of the gigafactory from the beginning of the production process, or the electric vehicle with a big battery pack from the end of the process, those can all go essentially into that same front-end process by which we take in the input scrap material or end-of-life lithium-ion battery, and then process it through our Hydro-to-Cathode line.
Sorting is not required. But it can help. We want to make it as efficient as possible. And by sorting up front, it can help with the efficiency. However, even without the sorting up front, the process is still more efficient than what's traditionally done out there, which is to use either high-temperature incineration processes known as pyrometallurgy processes, or traditional hydrometallurgy processes, which then basically create only commodity metals and don't go all the way back into these important cathode active materials. Our process is still incredibly efficient. But we're always looking to squeeze out even more inefficiencies.
AS: Are the recycled materials you produce and use to create new batteries just as, if not more, efficient than raw materials from mined sources?
RL: There was a very interesting result from a study that was done by a third-party consortium called the USABC, which is comprised of companies like GM, Ford, and Stellantis, to look at advanced batteries for automotive purposes. USABC did a study on batteries made using cathode material from our Hydro-to-Cathode process and compared it against cathode material of the same composition but made using traditional cathode processes.
What they found was that on all the important parameters they performed similarly, whether they were made from our Hydro-to-Cathode materials, or made using a traditional cathode process. In two cases they found the performance of the Hydro-to-Cathode materials from recycled feedstock actually exceeded that of the traditionally made cathode materials from newly mined, virgin feedstocks.
Those two areas were in cycle life (how many times you can charge and discharge a battery before it fails to hold charge anymore) and in power capability. The cycle life was seen to be between 30 and 50 percent longer than the traditional cathode materials. And the power capability was upwards of 80 percent greater.
It turns out, the porosity inside the particles of the cathode active material enabled the lithium to travel more easily through the cathode material and thus enabled higher power capability. The porosity also better accommodated the stress and strain of charging and discharging the materials so that it would not be damaged as much with every charge and discharge cycle as a traditionally made material would be.
What's important to note here though is that the porosity is just one aspect of the material that we can control using our technology. However, we can also modify things like the composition of the material - changing the ratio of nickel to manganese to cobalt, for instance, manufacturing an NMC 811 cathode active material from NMC 111 input scrap batteries. We can also control particle size and particle size distribution, the crystallinity of the particle, the shape or morphology of the particle, in addition to the porosity. It is a very versatile material engineering technology.
AS: Why is there the general perception that recycled materials are not as good as raw or mined materials?
RL: I think it's just a common conventional wisdom that a recycled product is always going to be inferior to a pristine or virgin made product. I think most of that experience comes from dealing with recycled paper or plastic, other things that go through a process. And then when you come out the other end, you find that it is not as high quality as before. That's not true with what we do with the battery materials because we focus on the battery elements. The ones that are so valuable to us, the lithium, the nickel, the cobalt, are elements - meaning they cannot be destroyed and can be infinitely recycled. Paper and plastic are not elements - they are compounds. So is cathode active material. It's important to note we are not doing what's called direct recycling of lithium-ion batteries either. We're not taking the old battery materials and just trying to wash them or rejuvenate them, and put them in new batteries as if they're new. We're breaking down all those battery materials to their core elemental components, into individual atoms, the most basic building block of matter. We're then rebuilding those atoms back up into new cathode materials, engineered for high performance, which is why we can have the results that rival or, in some cases, exceed that of the traditionally made cathode materials.
AS: As more vehicles are becoming battery-powered, is Ascend Elements planning for an influx of more feedstock?
RL: Yes. We've got expansion plans to increase capacity in the U.S., over in the EU, and the U.K., and even parts of Asia because we know electric vehicles will grow in those regions going forward. EVs, especially the light-duty passenger EVs, are going to be the largest demand for lithium-ion batteries, surpassing what consumer electronic devices like laptops or smartphones consume.
But we're also looking at applications in ESS, or energy storage systems. These are very large batteries that could be thousands of times larger than an EV battery. They are installed in the electricity grid for instance to help store solar power that's generated during the day for use at night after the sun goes down. That's another growing segment of application for lithium-ion batteries.
So there's a lot of demand and there will be a lot of lithium-ion batteries coming from not only vehicles, but from other applications. The one tenet is that these lithium-ion batteries will all wear out at some point. We have not yet invented a way to make them last forever. They will all need to be recovered and recycled at some point.
AS: What will be your focus for 2022?
RL: 2022 is the beginning of our capacity build out to accommodate the growing number of lithium-ion batteries that will need to be processed. By 2025, we're expecting over a million metric tons of lithium-ion batteries to be available for recycling globally, from both end-of-life batteries as well as manufacturing scrap.
We're expanding our capabilities now at our plant in Covington, GA. This 154,000-square-foot facility will be focused on producing the black mass and extracting lithium, nickel, and cobalt. That's what we call a Base-class facility, and Covington will be known as "Base 1."
In our next phase, which we will begin this year, we will open a new facility where we process the outputs from Base 1 back into new cathode active material. That's really where the heart of our Hydro-to-Cathode process will be, at this facility. We will call this our Apex-class facility, and this new plant will be "Apex 1." This is where we will raise critical battery elements to the highest level, or "apex value," in the lithium-ion battery supply chain. Our mission is to elevate the value of recycled elements by engineering sustainable materials for the global transition to clean energy, and provide sustainability without compromise.