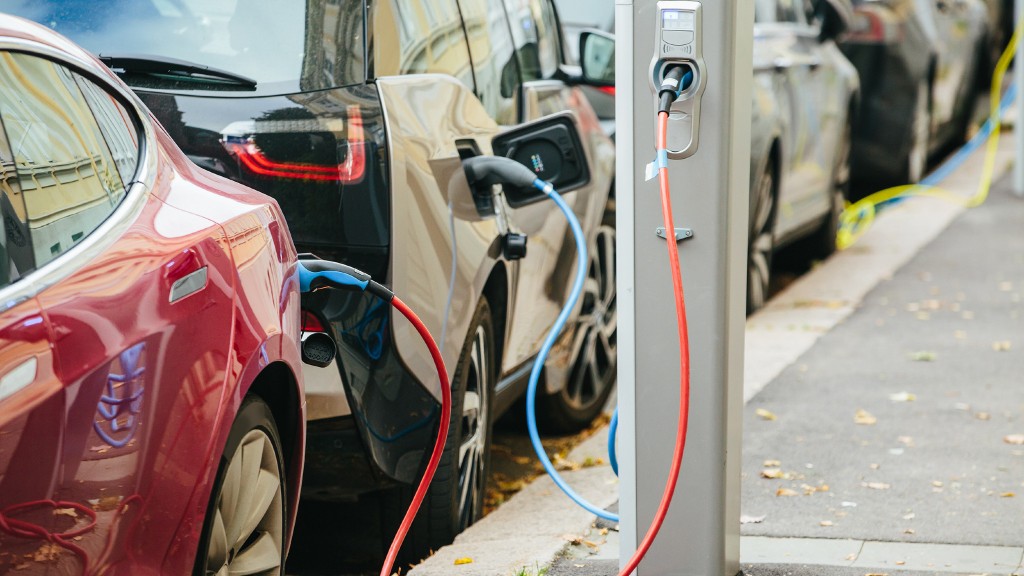
It's no secret that the recycling industry has become increasingly aware (and nervous) about the implications of electric vehicles reaching their end of life. As more of this type of cars approach the ten-year limit awarded to their batteries (of the ever-feared lithium-ion variety), all recyclers should not only be prepared to receive an influx of unwanted material, but benefit from the legislative push and incentives to have more EVs on Canadian streets.
Canadians are buying more electric vehicles than ever, even considering the overall decline in vehicle sales. During the last quarter of 2021, EV registrations showed an increase of 26 percent compared to the same period of 2020. Considering that total vehicle registrations were down by 8.7 percent, it becomes evident that government incentives are working across all provinces.
These batteries were designed to reduce costs – not with recycling in mind. Specific processes, additaments, and adhesives drive up recycling costs, which makes the concept of "design for recycling" essential. It's not enough for product designers and engineers to incorporate a percentage of recycled materials into their designs; they also need to think about what will happen to the product once it reaches its end of life. Cathodes are a valuable component of lithium-ion batteries, containing metals such as cobalt and nickel which are highly valuable to recyclers. A direct recycling method preserves this cathode mixture rather than breaking it down into individual components, making recycled cathodes appealing to battery manufacturers since they don't need to undergo heavy processing.
In the Faraday Institution's ReLib project, researchers from the University of Leicester and University of Birmingham have found a way to recycle cathode and anode without shredding by using ultrasonic waves. With this technology, cobalt, nickel, and manganese cathode powder is recovered from aluminum sheets to which it is glued during battery manufacturing. Graphite powder, which typically makes up the anode powder, is separated from the copper sheet.
It is estimated that using this new technology will save 60 percent over the cost of virgin material. In addition, ultrasonic technology can process 100 times more battery material per hour than hydrometallurgy.
The U.S. Department of Energy is now demonstrating different recycling technologies to refurbish battery cathodes into new electrodes using thermal and solvent methods under a government-sponsored project called ReCell. Due to a lack of cathode production in the country, recyclers must ship their recycled material to other countries to be turned into the cathode and then ship it back. Now, ReCell is investigating different cathode chemistry separations.
As new technologies are developed, it will be more profitable for recyclers to take on lithium-ion batteries, which will help grow our industry.
María Santarini is the communications manager for the Canadian Association of Recycling Industries.