Testing materials before investing in sorting technologies reduces risk, validates process
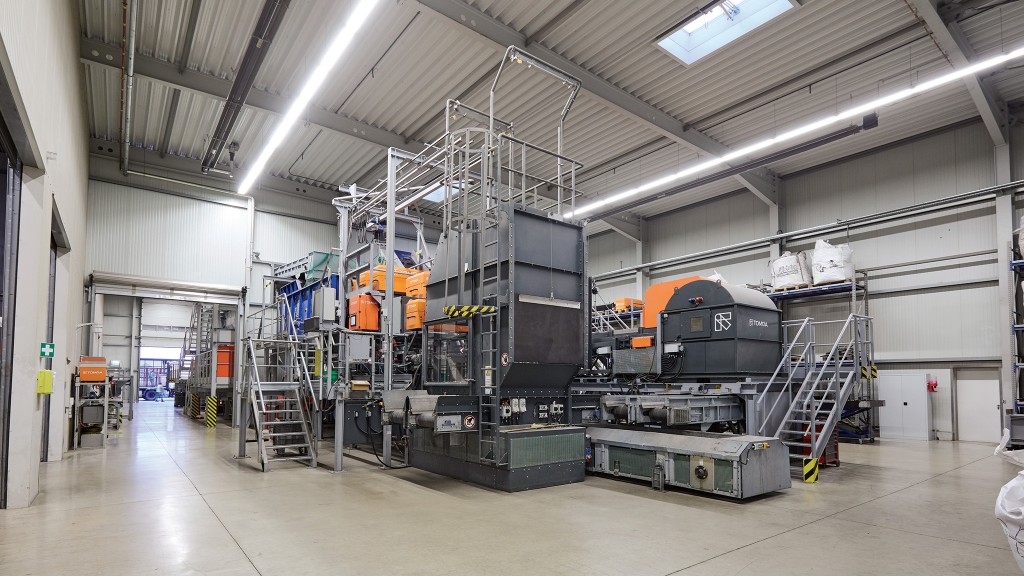
As the recycling industry grapples with increasing purity standards and a dwindling labour pool, automation and advanced sorting technologies are key to delivering a high-quality recycled product at the desired profit margin.
It is important to install the right equipment to sort the planned material stream to optimize return on investment (ROI). It's also critical to configure a flexible system that can adapt to future material stream changes and legislation mandates.
"The industry must think about material recycling similar to a manufacturing environment," comments Bill Close, business development manager for Wendt Corporation. "We establish well defined practices that automate handling at each station to deliver a finished product with consistent results every time."
Material analysis and testing play roles in purchasing the right automated system to provide these results. No matter the operation's size, all companies can benefit from partnering with the right provider.
"We conduct roughly 600 tests annually at our test centre in Germany," says Andre Lehmann, test centre manager, recycling, Germany for TOMRA Recycling in Mülheim-Kärlich. One of seven facilities worldwide, this main TOMRA Test Center is configured with the full array of the company's latest sorting technologies.
A key supplier of TOMRA optical sorters for North America, Van Dyk Recycling Solutions operates North America's largest test centre in Norwalk, Connecticut. It is newly equipped with five different TOMRA optical sorters, offering a "try before you buy" tool for waste processors as well as industry stakeholders.
"Our test centre can simulate many processes within a material recovery facility that you would find anywhere in North America," says Alex Wolf, technical director for Van Dyk. "We run tests to validate results, open our facility to associations, brand owners, and packaging manufacturers, and test with high-volume plastics processors."
The industry has matured to the point where not all materials and applications need to be tested.
"We don't need to test materials like plastic bottle sorting, since we have a vast amount of data, experience, and installations handling the material," says Lehmann. "However, new applications or difficult-to-process materials need process validation."
Testing evolution
Over the last two decades, companies like TOMRA and its plant building partners have evolved their testing facilities to reflect the challenges of the time.
"We have one test plant for automobile shredder residue (ASR), but it has gone through six different generations," says Close. "Today, our facility is set up like a lab."
The company's lab has stations that include the TOMRA FINDER for recovering non-ferrous metal fractions from ASR; X-TRACT using X-ray technology to sort Zorba to Twitch for furnace-ready recycled aluminum; and COMBISENSE for colour sorting heavy non-ferrous metals.
"Today, we can conduct our testing with four super sacks of material," adds Close.
There was a time when sorting automation with sensor-based sorting was new. "In 2007, we had to convince our customers they needed to purchase optical sorters to reduce manual sorting," recalls Wolf. Truckloads of material were shipped to testing facilities to validate the process and justify the investment.
Today, technology providers and plant builders have many installations where customers with similar waste streams can visit. As a next step, customers can send samples of their materials to a test facility to validate the process. Machines with high-resolution sensors include a myriad of technologies - near infrared, camera, X-ray, electromagnetic, laser, and deep learning - all designed to validate even the most complex sorting challenges with more accuracy.
"Before, material recovery facilities could get by with a higher percentage of contaminants in the final product, but that has changed with the end-market situation," explains Wolf.
Ty Rhoad, regional director Americas for TOMRA Recycling adds, "This is why it's critical to invest in the right sorting technologies to meet the desired purity goals in the required number of steps."
The Van Dyk test centre includes two TOMRA AUTOSORT units, AUTOSORT FINES, FINDER, and X-TRACT, along with a new technology to meet the emerging interest in flake sorting. "We are seeing a higher demand for plastic flake in North America, so we have added a new AUTOSORT FLAKE unit to our testing line," says Wolf. In its short tenure, multiple tests have been run on the unit for customers.
The global increase in demand for flake sorting prompted TOMRA Recycling to open its new test centre in Parma, Italy. The facility is dedicated to plastic flake sorting and the development of new applications and solutions in the fields of polyolefins (PO) and polyethylene terephthalate (PET) flake sorting.
"With our new Parma centre, we continue to advance solutions for recycling plants targeting to successfully upgrade plastics. The sorting line includes AUTOSORT FLAKE and INNOSORT FLAKE, which recover plastic flakes (PET, PO, PVC) as small as 0.079 inches (2 mm)," explains Rhoad. "AUTOSORT FLAKE excels in applications where contaminant levels are low, but quality standards are high. INNOSORT FLAKE will sort more contaminated streams and is available with a PO-specific sensor to sort polyolefins."
Getting the right mix
"We had a small shredder operator once ask for a FINDER to recover more non-ferrous fractions from the ASR stream," says Close. Wendt Corporation ran material samples at its test centre and found that the sorter alone would not help the company reach its goals. "FINDER was a part of the solution, but the company needed other components as well," he adds.
With the most recent technologies, recyclers should not go into plant upgrades or new system installations thinking that one component will be the solution. Rather, companies must take a holistic approach to designing a circuit that includes the right mix of equipment and technology. Testing with a trusted technology provider can help to maximize ROI.
"Just as we are experts with sorting technology, recyclers must be aware that they are the experts with their materials, what products and impurities make up their stream and the desired outcome," mentions Lehmann. "They must advise us whether they need 98 percent or 99.5 percent purity. We will test the material with different sorting technologies to get the best equipment for the desired number of handling steps."
The process usually starts with meetings between sales and the customer. Depending on the material, the plant builder and/or technology provider may recommend visiting a plant with similar material flow, recommend a material test or do a mixture of both.
"Often, the test is a confirmation of what sales is recommending," says Wolf. "However, we are seeing an increase in the amount of unusual material and non-standard applications, so in these instances testing is a must."
When testing material, recyclers are responsible for proper material preparation. "We recommend that customers pre-treat the material with upstream processing equipment prior to sending it to TOMRA, so it will be similar to what our equipment will sort in the plant," says Rhoad.
Plant builders like Wendt Corporation and Van Dyk often offer more upstream processing equipment as part of their test facilities, so less material preparation may be required.
"In addition to TOMRA machines, Van Dyk's test centre includes an elliptical screen along with other mechanical 2D and 3D material separators," says Wolf.
For processing end-of-life vehicles, "our test lab includes magnets, screens, and eddy currents in addition to the TOMRA FINDER, X-TRACT, and COMBISENSE," adds Close.
Regardless of where testing occurs, all recommend in-person visits to the facility when their material is running. "It is beneficial for customers to see their material being tested and how the different technologies are employed to help reach their goals," says Lehmann.
Close adds, "We know it works. It's best if the customer can see, learn, and understand how the testing works."
TOMRA process engineers examine the material and consider the customer's objectives to determine the necessary technology or blend of technologies required. They measure production capacity, determine air demands, and evaluate the material recovery and purity. Generated reports consist of flow charts with the recommended sorting technologies and the required steps to reach goals.
"Depending on material complexity and objectives, it can take as little as a day or up to a week or longer to conduct testing," explains Lehmann. On average, it takes between 8 to 10 weeks from first meetings to test completion and reporting.
Push to automate
As the industry advances automation, testing is key to success. "We are always pushing the boundaries, and we now have plants that sort to furnace-ready aluminum," says Close. "There is a vision of full plant automation with workers in a control room that receive and react to data, where quality control hand picking is handled by robots."
Deep learning and artificial intelligence are assisting the industry to advance this sorting automation. "With TOMRA GAIN, we use deep learning to sort more complex material fractions, and we can tie the entire system - or multiple systems from different locations - together with TOMRA Insight data reporting," says Rhoad.
Wolf agrees, adding that the industry has always set its sight on reducing labour through more automation. However, he sees limitations with today's technology in reaching the fully autonomous plant.
"Full automation drives up the investment, which may negatively impact the ROI of the overall project," says Wolf. "We have seen this with the advent of robots. They are not the silver bullet answer to everything as originally thought, and it's all application dependent."
Rick Zettler is a technical writer based in Cedar Rapids, Iowa.