New Shredder Feeder Conveyors from Bunting designed for plastics recycling
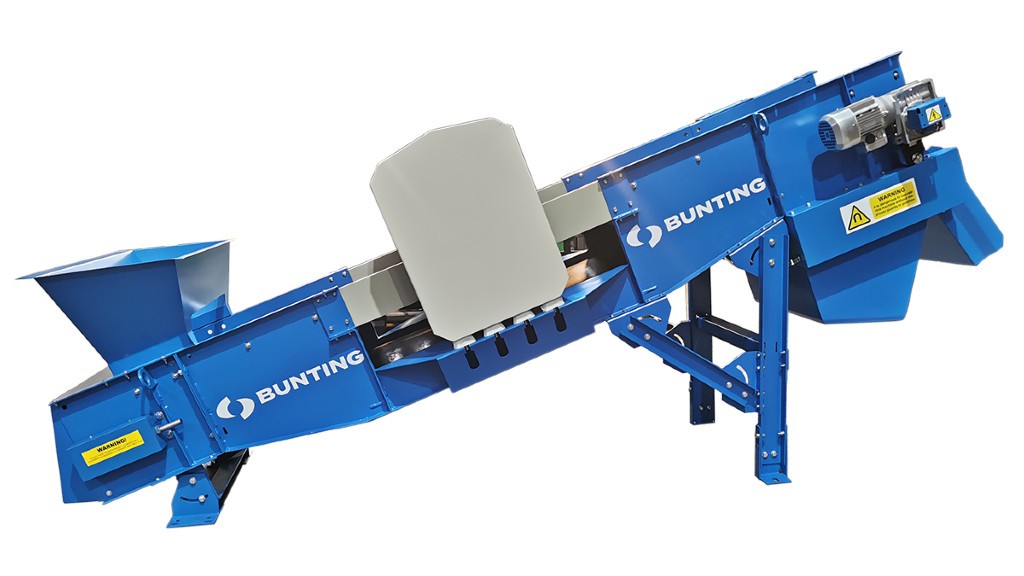
The new Shredder Feeder Conveyor from Bunting-Redditch combines with either a magnetic separator or metal detector to protect a shredder or granulator from metal damage. Specifically designed for recycling plastics, both in-house regrind and from secondary sources, this new Shredder Feeder Conveyor provides an even and controlled feed into a shredder or granulator, and the design specifically accommodates a metal detector or magnetic separator.
According to Bunting, shredder damage from metal contamination is costly in both repair and production downtime. Materials fed on the Shredder Feeder Conveyor pass through a metal detector or under a magnetic separator to find and remove such metal. Such protection prevents shredder damage and metal contaminants being reduced into smaller particle sizes, which become more difficult to remove.
Shredder Feeder Conveyors are also located post-shredding and prior to feeding the material into a granulator or extruder. Identifying and removing metal at this stage both protects the granulator and extruder from damage, whilst also ensuring the quality of the regrind prior to internal use or external sale.
The Shredder Feeder Conveyor design accommodates different designs of magnetic separator including Overband Magnets, Suspension Magnets, Plate Magnets, and Pulley Magnets. The design of the conveyor limits potential magnetisation of the supporting frame to ensure clean discharge of captured ferrous metal.
Different conveyor designs often detrimentally affect the performance of a Metal Detector. The Shredder Feeder Conveyor specifically includes design features to minimise any metal detector interference and ensure optimum detection at all times. The application and nature of the metal contamination determines the selection of either an Underbelt or Tunnel-type Metal Detector. The optional extra of an automated reject system enables the removal of metal contamination without disrupting the material flow. On identifying metal in the material, the metal detector transmits a signal to a reject flap mounted at the end of the conveyor. The reject flap redirects the contaminated material into a separate collection area.