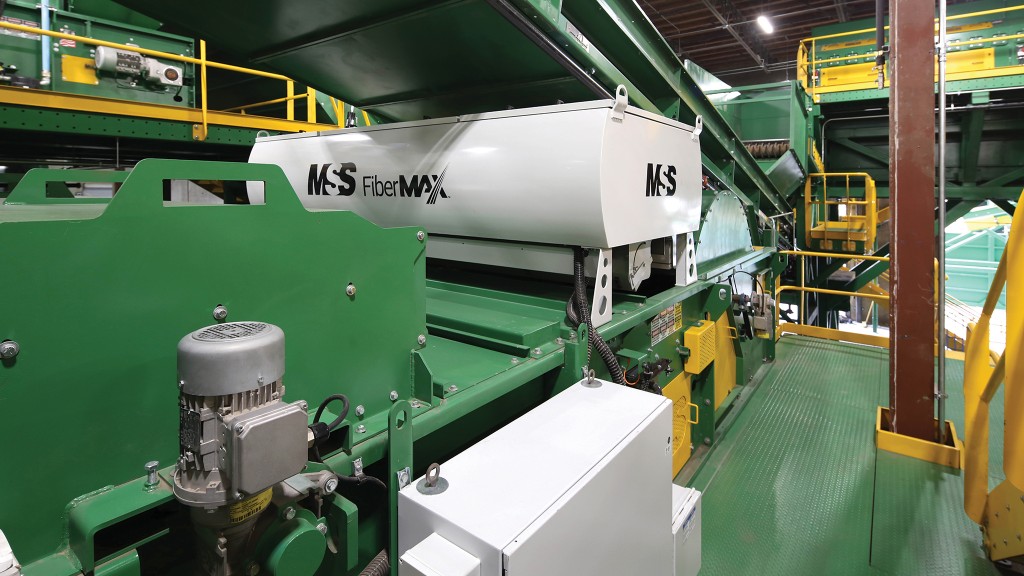
Contamination of incoming OCC and other fibre streams at the MRF has risen significantly over the last several years. The pandemic has had an effect on what is being discarded, how much, and where. Today's MRF's see much more OCC and mixed paper from curbside programs, but far less Sorted Office Paper from businesses, for example. For MRF operators who are having issues with contamination of their incoming streams, resulting in higher sorting costs and lower purity of output, there are technology and strategies that can help.
RPN caught up with Nick Davis, product development engineer at CP Manufacturing, to talk about the nature of contamination in the OCC fibre stream and about some of the best practices and technology currently available for safely and efficiently achieving high-purity output at the MRF.
Keith Barker: Which grades of recovered fibre are most affected by high contamination rates, and what is the main contaminant?
Nick Davis: Most paper contamination is small in size and tends to flow with the mixed paper streams. For example, items such as soiled napkins, straws, and wrappers end up in the small paper fraction. These low-weight, high-pick-count items are difficult to sort without optical sorters. OCC on the other hand tends to be positively sorted and has less contamination concerns.
KB: How has the COVID-19 pandemic affected the amount of contamination in single-stream systems overall?
ND: Overall, contamination has increased due to the COVID-19 pandemic as a result of people being at home more, cleaning out garages, attics and storage rooms. Some items thought of as being recyclable are thrown out erroneously and have created excess contamination that is widespread in all streams, especially mixed fibre.
KB: What is the easiest change, or the first thing a MRF or other recycling facility should consider doing, if they are struggling with high contamination of their incoming fibre stream, but want to take advantage of the current high market prices for clean, recovered OCC, for example?
ND: The type of contamination that appears in a MRF's OCC stream determines how to respond. If the OCC has small items such as glass, grit or small plastics, that means the screening isn't working correctly. The facility can adjust OCC screen parameters or openings to get the grit out. Additionally, adjusting the infeed mechanisms and pre-sort belt speeds can thin out and prepare material hitting the OCC screen.
For larger contamination items, slow down throughput to allow manual sorters to see the impurity better so they can pull it out in a post-sort. If an optical sorter is already in place, a switch from a negative to a positive sort logic should be considered.
Many MRFs have tightened their OCC patterns in the last couple years in an attempt to capture more of the massive amounts of small OCC generated as a result of the "Amazon effect." If a screen is tightened too much, the natural consequence is more contamination in the overs or reduced capacity, which then has to be adjusted in other parameters.
KB: What equipment do you recommend using at a MRF or other recycling facility to produce high-purity OCC from mixed incoming streams, in basic terms?
ND: We use a CP Drum Feeder, CP Auger Screen followed by a CP OCC Screen for large-size OCC. Additionally, we use an Anti-Wrap Screen and CPScreen, respectively, in combination with an MSS FiberMax optical sorter, for small- and medium-sized OCC.
KB: How should the methodology or process change, depending on varying sizes of incoming OCC?
ND: Different sizes of OCC are sorted in different manners. Large OCC is liberated by an OCC screen that prepares the material on high amplitude discs. The large openings on the screen reduce contamination. A drum feeder fluffs and breaks up nested material and layers large OCC on top of smaller items to enhance screening.
We started placing an Auger Screen in front of the OCC screen to remove a significant amount of the smaller fraction in the inbound flow. Lower input to the OCC screen is more efficient because the machine parameters can be finely tuned to liberate OCC from larger items, and there is additional screening from the Auger Screen. After screening has done all it can, any remaining large items are easier to remove at the QC station.
Smaller OCC items that go in the unders of the OCC screen are seen throughout the MRF flows and need to be positively sorted at several locations either by people or optical sorters.
KB: Can you explain the CP Group methodology principle of "fractionate, liberate and separate."
ND: Fractionation is the process of sizing and breaking up inbound material into smaller streams so that each station, screen, automated sorter or person can work more efficiently. By fractionating upstream of the OCC screen with the Auger Screen, we reduce the inbound burden depth and contamination, so a cleaner OCC product is processed.
In the next step of liberation, we use high amplitude, high agitation mechanical devices at multiple stages throughout the process to singulate each item and break up conjoined material. Essentially this process removes 2D from 3D materials, while also reducing grit and small contamination.
Once the prep work is done, we separate with an MSS FiberMax optical screen for positive identification and sorting of OCC to produce high-quality end products.
KB: Should positive sorting of smaller OCC be a key part of a MRFs best strategy for producing clean OCC output from mixed incoming streams?
ND: It is recommended, and really, a necessity, to positive sort for small- to mid-size OCC. In our experience sufficient screening and QC will produce clean OCC, especially if the inbound material is prepared properly and multiple stages of screening are used.
KB: What's next for CP Group in 2021?
ND: CP Group is continuing development in automation, data collection and MRF optimization. Last year we tested our latest development, the patented CP Elliptical Auger Screen. This new machine adds aggressive agitation to the sorting process, fractionates the stream and then liberates the material. This can be used for primary and secondary sorting, and its dual action earlier in the process enhances downstream separation.
As we further roll out development of the CP Elliptical Auger Screen, we are confident that it can reduce or even eliminate the pre-sort in many facilities.
Nick Davis is the product development engineer at CP Manufacturing. He holds a Bachelor of Science in Applied Mathematics and Quantitative Economics, is a third-generation inventor in recycling equipment and development, and holds multiple patents for improving mechanical separation.