Cortec's VCI plastic recycling service shows a circular economy in action
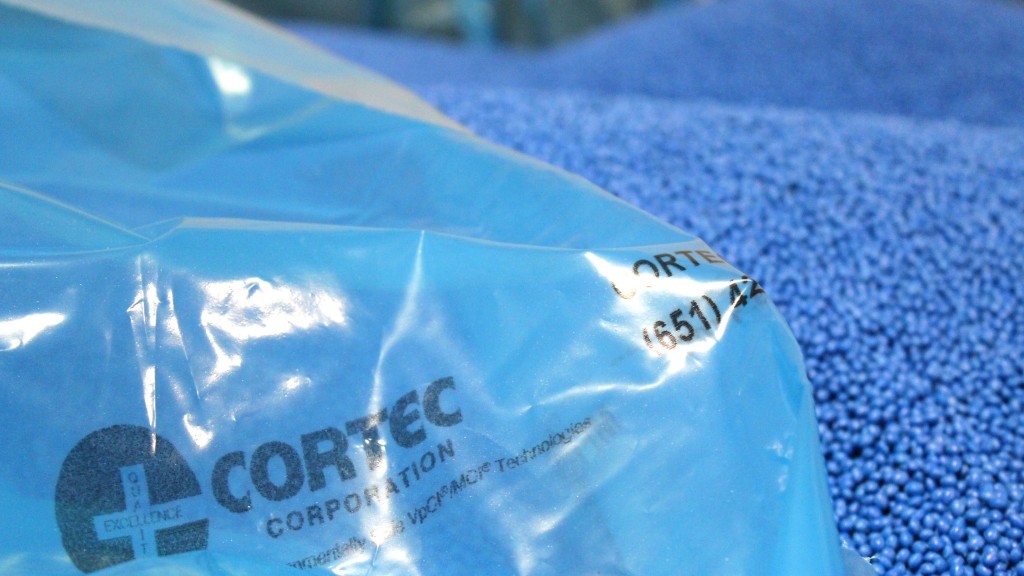
As the U.S. plastic bag industry seeks to increase the percentage of recycled content in shopping bags to 20 percent by 2025 for greater sustainability, Cortec Corporation is already familiar with the field of VCI packaging.
More than 20 years ago, Cortec patented the technology for making anti-corrosion film using recycled plastic resin. Today, Cortec has a recycling program that produces VCI film with up to 20 percent recycled film content.
On average, Cortec regularly manufactures its VpCI-126 film with 15 percent pre- and post- consumer recycled content, outpacing recent ARPBA milestone goals of reaching 10 percent recycled content shopping bags by 2021 and 15 percent recycled content bags by 2023. Cortec's VpCI-126 film can be extruded and converted into many different formats and sizes depending on the needs of the end user—from the manufacturer who wants to protect a small metal gear in a VpCI-126 Top-Seal bag, to the plant manager looking for a way to preserve a large industrial asset in VpCI- 126 film during storage or shipment.
Cortec has been able to minimize its own plastic film waste for decades by recycling in-house VpCI-126 scrap at its Cortec Advanced Films(CAF) plant in Cambridge, Minnesota.
Several years ago, Cortec was able to extend this recycling opportunity to a major off-road equipment assembly plant that receives engine components from dozens of suppliers across the U.S. and the world. After assigning a Six Sigma Black Belt to study the proposal, the manufacturer adopted the recycling program and eliminated its outdated specification of adding oil to VpCI-126 packaging, since testing showed no impact on corrosion protection.
This in itself saved the customer several hundred thousand dollars per year by reducing chemical liability insurance costs, allowing them to reuse corrugated plastic liners that previously had to be disposed due to oil contamination, and letting them participate in Cortec's recycling program. Because the VpCI-126 bags are also no longer oil-contaminated, the customer bales them and sends them back to CAF for reprocessing into new film.
Cortec pays shipping costs and gives the customer credit in return. "Their suppliers' garbage is now a revenue stream for their plant," explained Mike Gabor, Cortec VP Sales of Eastern North America.