Advancing aerobic composting at Freestate Farms
Vermeer trommel key part of system in Virginia allowing for processing of 80,000 tonnes of organic waste yearly
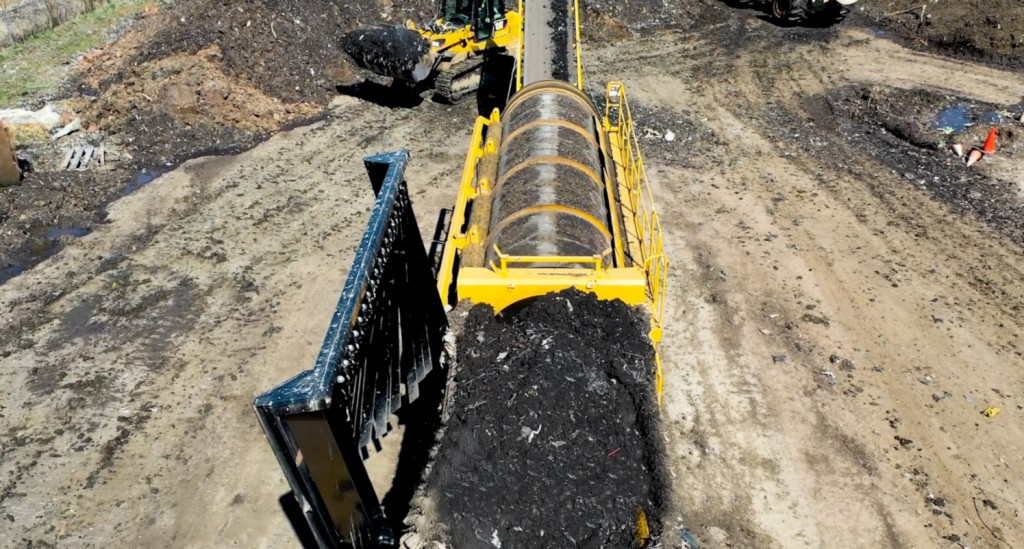
Communities throughout North America are implementing recycling programs to extend the life of waste management facilities. Green waste programs have been a centrepiece of these efforts for decades. However, until recently, many green waste recovery programs have only focused on the efficient collection of yard and wood waste material, with the majority of profits coming from disposal fees. Today, savvy composting facilities are flipping that "old" business model on its head by incorporating technology and science to create both renewable energy and nutrient-rich compost that can be sold at a premium price.
Advanced aerobic composting
At the Balls Ford Road Composting Facility in Manassas, Virginia, construction is underway on a new advanced aerobic composting system. When completed in 2020, the facility will be able to process over 80,000 tons (72.6 mt) of organic waste per year, turning it into compost, soil products and non-synthetic fertilizers. The operation is a public-private partnership between Prince William County and Freestate Farms, LLC, a local organic waste recycling and agricultural services and production company.
Freestate Farms operates the Balls Ford Road Composting Facility and is responsible for financing and building the new facility. The first phase of the construction project, currently underway, involves using advanced aerobic composting technology to speed up and optimize the composting system. When complete, the system will automatically control the flow of air through concrete aeration floors to maintain optimal aerobic conditions in piles and control odours.
In the second phase of the project, Freestate Farms will construct an anaerobic digestion system for processing food waste in a fully enclosed airtight tank, producing methane-rich biogas and fertilizer products. In the final phase, Freestate Farms, with its roots in organic agriculture, will use the material it produces to generate energy and grow produce for the local area.
"It's taken several years of planning to get to where we are today, but when it's all complete, people will get a first-hand look of what can be done through a robust recycling program," said Jeffery Morton, operations manager for Freestate Farms. "All of the work and knowledge we've gained along the way is being incorporated into this new system. The quality products that we're able to produce and distribute right now are what makes building a more advanced facility a viable option."
Focus on the end-product
Freestate Farms took over operations at the Balls Ford Road Composting Facility back in 2015. The facility takes in yard waste from approximately 150,000 households and 8,000 local businesses and has a permitted capacity of 50,000 tons (35.4 mt) per year. Currently, the facility is handling about 30,000 tons (27.2 mt) tons of material annually.
Incoming material is comprised mostly of yard waste such as grass, leaves, tree limbs and some food waste. According to Morton, processing, handling and screening are vital in creating quality end products.
"Incoming material gets run through our grinder, then stacked in windrows and turned regularly to make sure there are adequate oxygen levels," Morton said. "That part of the process usually takes between 6 to 8 months. After that, we screen off the larger material, leaving us with nutrient-rich compost and soils that are used by growers and consumers. The larger material is then turned into dense nutrient mulch or added back into the composting piles."
According to Morton, the experienced team at Freestate Farms understands how the material that is screened has an impact on its value and what someone will pay for it. "Screening takes time and is often viewed as a bottleneck in the composting process, but it doesn't have to be that way," he explained.
"After trying several different models of trommel screens on the market, we discovered that the VermeerTR626 trommel screen was the right fit for our operations. It's convenient to operate, reliable and consistently produces, no matter what the moisture content is outside."
Delivering value
Freestate Farms invested in its fourth Vermeer TR626 several years ago and is anticipating adding another soon.
"When we're thinking about adding a machine, we look at the purchase price and production rates," explained Morton. "We've always found that this Vermeer trommel produces more per hour than any other machine in its price range.
"We consistently produce close to 65 yards (59.4 m) per hour. It's also efficient with fuel and easy to maintain, which helps keep our running costs low."
Sam Morton, Freestate Farms trommel operator and site manager, added that the TR626 is convenient to use and it does a fantastic job of removing unwanted material from the finished product. "It outperforms anything I've operated before," he explained. "Also, replacing and swapping out screens is pretty darn easy to do too."
Both Jefferey and Sam Morton agree that balancing equipment costs and operating expenses greatly helps Freestate Farms manage its fixed expenses - but fixed expenses are only part of the equation.
Composting facilities need to have a demand for the products they are producing.
The Mortons give the TR626 high marks for helping in that department.
"Word-of-mouth has driven up demand for the compost we produce," said Sam Morton. "Businesses and homeowners know we produce an excellent product, so we never find ourselves in a spot wondering what we are going to do with all the material we take in. Instead, we hustle every day to try to keep up."
Working together, building for the future
The public-private partnership formed between the Prince William Board of County Supervisors and Freestate Farms is benefitting everyone in the community.
"Having a good partner is important for business success. We have that with the county, and with the companies who supply the equipment we use to produce compost," said Jefferey Morton.
"One of the first calls we made after taking over operations in 2015 was to Vermeer Mid Atlantic Recycling & Forestry Specialist Steve Zaicko," he added. "Steve set us up with the grinder and helped us fine-tune our process. Since then, we've added more Vermeer equipment because of the fast and reliable service we received from Steve and everyone at the Vermeer Mid Atlantic dealership in Manassas. Steve is knowledgeable about our business and our equipment needs. It's partnerships like this one that are helping us get to where we want to be."
The processes and machinery Freestate Farms employ today is definitely also helping them prepare for future operations. By continuing to tweak methods and by consistently producing quality compost and soil products, the team will be ready to take on more in the future.
In fact, in just two years, according to the Mortons, the Balls Ford Road Facility is expected to not only double its processing capabilities and handle a broader range of organic waste, but also significantly extend the life of the local landfill. It is also expected increase the county's recycling rate by 30 percent.
John Reasor is a senior product marketing specialist, Vermeer.
This article was originally published in the November/December 2019 edition of Recycling Product News, Volume 27, Number 8.