Niagara Recycling is building on a unique model for MRFs
Non-profit social enterprise operation is efficiently recovering an extensive range of materials while providing employment for developmentally challenged adults
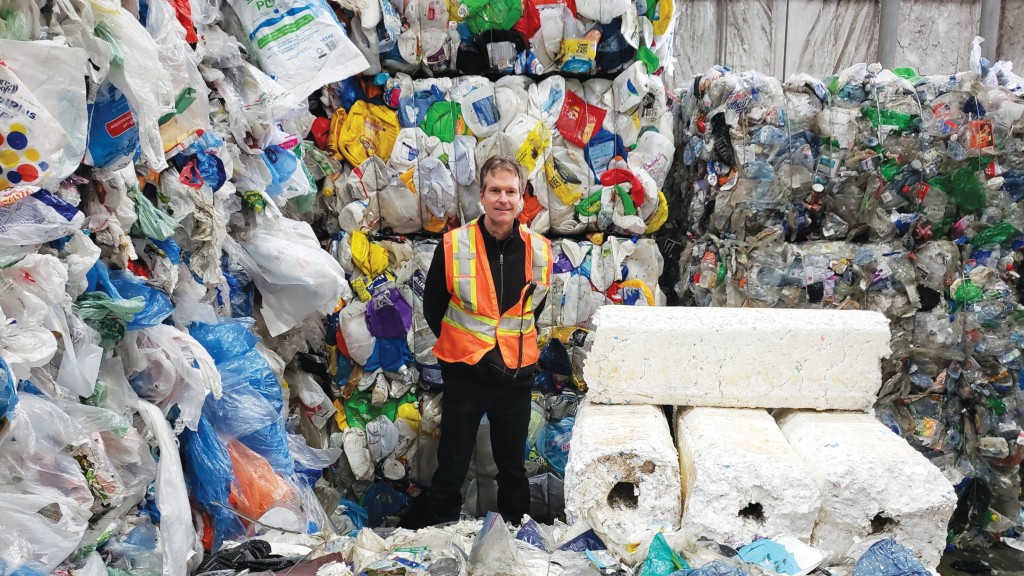
Niagara Recycling was incorporated in 1978 as a non-profit social enterprise company. Norm Kraft started with the company in 1989, became CEO in 1993, and has never looked back.
"I've seen everything in this business," says Kraft. "The ups and downs of the marketplace, the evolution of technology. It's certainly been an incredible ride."
Niagara Recycling pioneered recycling in the region in the Seventies, starting with door-to-door collection of newspaper using cube vans. In 1985 they implemented the second residential recycling Blue Box program in the province of Ontario - likely the second in Canada after nearby Kitchener-Waterloo.
"By the early nineties, all 12 municipalities in the Region had implemented blue box programs," says Kraft. "In 1996, the Niagara Region assumed responsibility for all waste management including recycling, and we've enjoyed a mutually beneficial 23-year partnership with them ever since."
At the start, as a non-profit social enterprise company, Kraft explains that Niagara Recycling was set up in partnership with another non-profit organization known as NTEC (Niagara Training and Employment Center) which has the sole mandate to provide assistance to people with developmental disabilities.
"We were originally one of the arms for NTEC, where we would integrate developmentally challenged adults into our workplace," he explains. "There was hardly any equipment then, maybe a few conveyors and mostly manual sorting of newspapers...a far cry from the sophistication used in MRFs today."
He adds that to his knowledge, Niagara Recycling's partnership with the Niagara Region, combined with its social mandate, is not a model that is being used elsewhere at MRFs on the same scale.
"Most of the MRFs in Ontario are operated by large corporations, as they are in many cities across North America, so it's rather unique to have this kind of close relationship with our Region," he says, adding that their facility also includes a MRF educational component through which they conduct public tours and school tours. "Since it is a public asset, it is important to showcase the facility to the community.
"Our relationship with Niagara also provides great flexibility for the Region as program changes can easily be made, often without complex and more costly negotiations that would occur with a private sector operator," he says. "We receive a fee for running the regionally owned 100,000 square-foot MRF and that fee is put back into the community. We submit an annual budget, they cover the expenses and they receive all the revenue from the sale of commodities.
"We operate as a non-profit social enterprise with two focuses. One is obviously to help the environment through recycling, but secondly, it is to support the program here for developmentally challenged adults. It's a very unique model for providing recycling services."
Working with NTEC, Niagara Recycling hires individuals with developmental disabilities who are fully integrated into their operation, working a 40-hour work week. They also run a work experience training program, providing part-time positions. According to Kraft, since 1996, Niagara Recycling has donated over $2.5 million back into the Niagara Region to support programs for developmentally challenged adults.
"Individuals in the part-time program receive counselling and coaching and skills development, and they get behavioural support and performance assessments," explains Kraft. "It's a way of teaching individuals with disabilities about life and work skills." He adds that while they only have so many positions to offer, the part-time positions often integrate into full-time or part-time jobs within the local community.
"For any business that has an opportunity to integrate developmentally challenged individuals into the workplace, we highly recommend it," he continues. "They're working on the sorting lines, sorting polystyrene, paper or other plastics - wherever anyone else can work. And the changes in these individual's personalities is profound - once they get into the workplace, they gain social and work skills."
He says the employment of developmentally challenged adults also provides great benefits for Niagara Recycling. "It brings a feeling of community and it boosts morale. Co-workers are always watching out for these individuals, and they have a great sense of humour and bring laughter into our workplace. They are a very special part of Niagara Recycling."
Dual-Stream and a diversity of inflow
Niagara Recycling, different from most programs in North America currently, is a dual-stream MRF, and always has been. Kraft says more and more programs, especially smaller ones, are starting to revisit the choice to operate as single-stream, especially in light of changing global markets, such as China which has all but shut their doors to anything other than nearly 100 percent pure, uncontaminated recyclable material.
When fibre is mixed with plastics and other Blue Box materials as incoming material in single-stream collection programs, it takes significantly more processing effort and infrastructure to meet very strict contamination standards - for both streams of materials.
"There's a rethink around the benefits of single-stream," he says. "The fact that we've been two-stream from day one has ensured that we maximize our revenues and diversion from landfill." Niagara Recycling processes about 300 short tons of curbside and commercial material daily. Of that total, about 75 to 80 percent is fibre and most of the remainder is plastic and other containers. In Niagara, with about 450,000 residents, residential recyclable materials are collected in two curbside boxes.
The fibre stream is collected, along with plastic film, in a curbside Grey Box, including cardboard box board, newspaper, magazines, catalogues and office paper. The second stream, collected in a curbside Blue Box, consists of glass bottles and jars, steel cans, aluminum beverage cans, foil, aluminum, steel and aluminum aerosol and paint cans, polycoat and aseptic cartons, as well as all plastics one through seven, including polystyrene (styrofoam).
Kraft says that, generally speaking, residents do a good job of keeping items separated properly, but notes that the biggest challenge remains the proper source-separation of plastic film. Residents are asked to make sure all their plastic film, grocery bags, plastic packaging and stretch wrap is put into one bag, tied and placed in the Grey Box with the fibre stream. Often however, plastic film is still placed in the Blue Box, or loose in the Grey Box, which makes separation very challenging.
"We find film stays cleaner when it's in the Grey Box, which makes it better for our end market to process," he explains. "It is easier to separate this way, because when it gets in the Blue Box container stream the bags can rip open easily on the glass and metal, and become contaminated with liquids and fine glass."
He adds that while their two-stream system is a part of why Niagara Recycling has proven to be one of the more cost-effective operations in the province, the diverse nature of the materials they accept is also a significant factor.
"We have as comprehensive a list of acceptable items as probably anyone out there," says Kraft. "Unlike most other recycling operations in Ontario, if not Canada, we have diversified beyond the traditional model where a municipality hires a contractor to process material from Blue Box or Grey Box programs.
"For us, 52 percent of the tonnage that we process is from the residential program here. But because our facility is owned by the Region, through our unique partnership we also work together to bid on other contracts. About 48 percent of the volume we bring in is from third party municipal contracts and from commercial recycling programs that Niagara Recycling has developed over the last 30 years or more."
He says some third-party contracts they bid on in Ontario include additional fibre and containers from other municipal Blue Box programs, and all their contracts add up. "If we're processing 78,000 tons a year, those third-party contracts are close to 37,000 tons, so it allows us to generate more income for the Region."
With all of these sources, including some acceptable drop-off of items, including textiles and bulky rigid plastics such as old Blue Boxes, lawn chairs and more, Niagara Recycling definitely has one of the more comprehensive recycling programs in Ontario and maybe in Canada. Outside of film plastic and black plastics (including food trays and flower pots), items that many programs do not accept, they also recycle aerosol paint cans and expanded polystyrene (white and coloured styrofoam.)
"We have been able to find diverse markets and we've put in equipment that has allowed us to stay in the business of recycling a wide range of commodities," he says.
Yet another example of the diversified nature of Niagara Recycling's business is that they provide on-site document destruction services. "We bought a Shred-Tech shredding truck in 2012 and we offer on site NAID (National Association for Information Destruction)-certified shredding," Kraft explains.
"We provide on-site shredding services to local businesses, institutions and municipal offices. It's another way to generate income.
"We bring in upwards of up to 80 tons a month," says Kraft. "Office waste is worth a significant amount of money. Plus we charge for shredding services, so it definitely brings in good extra revenue for the Region."
Processing polystyrene and glass
Niagara Recycling's diversified capabilities include two particularly challenging materials: polystyrene (white and coloured styrofoam) and glass.
In 2016, after their optical sorting units were installed, they also installed a cold-press polystyrene processing plant, by which styrofoam material is compacted, without melting, up to a 50-to-1 ratio.
"We make it into 50-pound blocks that are about four feet long by one foot by one foot, which we stack on a pallet," explains Kraft. "We're actually shipping that to Europe and it's been a huge benefit for the Region."
Formerly, they marketed polystyrene with their mixed plastics, but that devalued the mixed plastics. "Today, I probably couldn't even sell mixed plastics containing styrofoam," he says. "The reason we put the system in was to process the styrofoam separately from our mixed plastics. Now we get over $50/ton for our mixed plastics and over $250/ton for polystyrene EPS blocks."
He says their recovered polystyrene is made into pellets, and then into new products such as crown moulding and picture frames. "Something that we may look at down the road is: does it make sense for us to do some pelletizing of our styrofoam, rather than shipping it all overseas for pelletizing? Maybe it makes sense to do it right here in Ontario."
For glass collected through the Region's Blue Box and other contracts, Niagara Recycling uses a processing system they designed in-house, creating the end-product Niagara Ecoglass.
Kraft explains that while most MRFs throughout Canada accept glass and many are investing in cleanup systems so they can move the material to end markets, those markets remain very strict on quality. Glass processors charge anywhere from $10 per ton up to $60 per ton, plus freight.
Niagara Recycling, on the other hand, keeps it in-house, processes it and sells it for over $100 per ton.
"We sell our Ecoglass in 50-pound bags, with our product information in French and English. We sell it in bulk, loose, dump trailers, and in large 3,000-pound sacks for some industrial customers. We sell about 90 percent into the sandblasting market. Our process makes great economic sense for glass, even when you factor in the cost of processing it. We are saving money on shipping it and not paying a glass processor to take it."
Kraft explains that their process first uses magnets to remove any small caps, lids, nails, etc. that were missed by the container line electromagnet. Then glass goes through a primary grinding stage where it is broken down to about a three-quarter-inch material. From there it goes through a series of screens and more magnets which remove even smaller pieces of metal.
"Then it goes in the dryer, which is where our process starts to move away from a traditional cleanup system," he explains. "Once we have the moisture down to less than half a percent, then that glass passes over a large multi-deck screen and makes three different product sizes that we're able to sell. We have a coarse, a medium and a fine. The largest size glass that we make is about a 16-mesh - a little bit bigger than a sand particle."
He says in total they process over 5,000 tons a year of glass, adding that because the material is very dirty when it comes in, contaminated with plastic, lids, labels, food waste and other residue, they do depend on their equipment and process to do a lot of cleaning and vacuuming to get that contamination out. "When you sell it as a sandblasting abrasive you can't have clumps of paper in there because it will jam their sandblasting nozzle."
Kraft continues, "We have a sustainable market for glass where we're actually in control of our own destiny. And we have an efficient process. We don't have to worry about having a market that may change, or where they may not take our material in the future. We've developed a very solid market for glass, which is a great accomplishment for Niagara."
Optical upgrades with end markets in mind
In late December 2015, the Niagara Region implemented a $2.5 million upgrade at the Niagara Recycling facility.
"We became one of the first in Ontario to use twin optical sorters to positively eject brown materials (cardboard/boxboard)," says Kraft. "At that time there was nobody else doing that at the level that we were proposing."
He explains that prior to their upgrade, fibre was manually sorted after the OCC separator. Now, the twin optical sorters are not only effectively ejecting cardboard and boxboard, they also eject items that shouldn't be in the fibre stream, including polycoat cartons, loose film, and all plastic bottles and containers.
"Each optical sorter operates at a throughput rate of 12 tons per hour, so up to 24 tons per hour over the two units, which is very impressive," says Kraft.
Niagara Recycling's optical sorting system was installed by Van Dyk, using Titech optical sorters - the largest models currently on the market at nine feet wide (shown above, opposite) While Van Dyk won the bid to put in the upgrade on the fibre optical sorting system, Kraft says the rest of the facility, since it was commissioned in 2004, is a combination of equipment and technology from various suppliers.
At the time they installed the optical sorters in late 2015, he says the objective was mainly to help create better quality material for the local mill, Resolute Forest Products. "We made the investment to improve our quality. At that time our quality was upwards of 30 percent contamination, consisting of all the plastic, garbage, as well as cardboard and boxboard. But within a year of installation, Resolute went out of business. All of a sudden, now we had to look at the export market because there wasn't sufficient domestic capacity to take our recovered newspaper.
"Then all the ‘problems' started happening in 2017 with China's announcement about restricted imports of mixed recycled materials."
At that point he says because of their 2015 upgrade, they were well suited to be able to tackle the challenges associated with the new quality requirements. "Our quality went from about 30 percent contamination, including prohibitives and outthrows, down to about 12 percent, which for us was tremendous," he says. With close to a 60 percent improvement in quality, it ensured they were able to continue to ship to export markets, other than China.
"With that investment in our optical sorters in 2015, taking a risk at that time on this equipment, it worked out very well in terms of being able to meet the current tougher market specifications."
Currently, Kraft says about 80 percent of Niagara Recycling's newspaper is exported to markets including Indonesia, Korea, Vietnam and India.
With respect to plastics, the story is a bit different.
"We have not shipped any of our residential Blue Box program plastics to China in almost 10 years, and never to India," he says. "We have sustainable markets right here in Ontario and the U.S. for our plastic film, our mixed plastics, our bulky rigid plastics and our PET and HDPE. We don't have any dependence on foreign markets for plastics."
Still, according to Kraft, the recent news about India planning to close its doors to mixed materials, with a similar policy to China's, leaves a lot of questions about what effect it will have on pricing in North America. He says MRFs that were shipping to India may now have to look at possibly re-routing into facilities in Canada and the U.S., which could end up driving prices down and be a big concern for MRF operators.
"I don't know how that's going to impact things here, but it certainly will impact companies that ship commercial grade films and other grades overseas," Kraft says. "It's going to probably put renewed emphasis on the need for more advanced processing here in North America in terms of pelletizing plastics. Once you pelletize, you can ship more into foreign markets."
New stewardship Policy - uncertain future
In Ontario, currently, the province is looking at switching to a 100 percent Stewardship-funded program for residential recyclables, similar to what has been done in other provinces in Canada. For Niagara Recycling, Kraft says the prospect of this new policy in Ontario evokes some red flags with respect to the future of their operation.
"Right now, in the province of Ontario, Stewardship Ontario pays 50 percent of the costs of our programs for collection and recovery of blue box materials," explains Kraft. "In British Columbia, about five years ago they switched to a 100 percent Stewardship-based program. Now they want to go to a similar 100 percent stewardship-run program here." He notes though that Ontario is somewhat different from B.C., because of the difference in scope. "Ontario produces at least three times as much recyclable volumes as B.C., so it means larger scale impacts."
He explains that Stewards in Ontario currently pay more than $125 million a year to municipalities to offset 50 percent of their recycling program costs. The money is removed from the residential tax base. With the proposed new program, that number could double to about $250 million a year.
"If you talk to the Stewards or the Provincial Environment Ministry, basically the philosophy is that if the Stewards are going to pay for the program entirely, they want full control of the collection contracts and MRF processing operations," says Kraft. "What it means potentially is that there is going to be consolidation, there's going to be local job losses. Companies like ours who help the community through our social enterprise model - the small companies, the non-profits who really are the engines that started recycling back in the ‘70s and ‘80s here - will likely all be gone and it's going to be only the ‘big players' that are going to be running our recycling facilities."
He says as far as he understands at this early stage, what the provincial government is aiming to do is have a centralized framework that essentially takes the number of MRFs in Ontario from about 53 to as low as 10 or 12. So far, a strategy has been developed based on what is referred to as catchment areas. Due to their location and population, it is most likely the nearest centralized facility would be situated in the Hamilton area.
He says if this happens, Niagara Region material may have to be hauled to Hamilton at the Stewards' expense, for example. "Then what opportunities will we have to stay in the business?" asks Kraft. "The Niagara Region would have to bid on processing its own material, and if Stewards don't like the price they get from Niagara, then our region would be stuck with a potentially empty facility - a stranded asset as the Stewards refer to it."
He says the current government is pushing this agenda, and it is expected that a new program will be rolled out by late 2021. "That's the latest I've heard and read and that's a pretty quick timetable to start transitioning municipalities over to a 100 percent Stewardship based program."
He also notes that while Stewards would only be responsible for the residential recycling program, which does not include commercial materials, they would likely also lose some of their current third party contracts with municipalities, as these would be captured in the other catchment areas established by the Stewards.
"It's disappointing that the Stewards and Province would not consider a hybrid model in which municipalities who own MRFs and prefer to do their own curbside collection and processing would have a choice to receive an increase in funding from the current 50 percent to about 80 percent, and could then continue to operate their recycling program on this basis. This would be a win-win situation for municipalities and smaller operators such as us. The Stewards would save about 20 percent in funding and in Niagara, we would make up some of the difference through our unique programs such as on-site shredding, glass processing and other commercial programs. There would also be no impact in recycling service levels to the taxpayers in Niagara."
"If we have 53 plants in Ontario and all of a sudden we're switching to a smaller number of massive MRFs, fully automated, with robotics and optical sorters, from a business perspective it makes sense. But it's a huge change and it could have local economic impacts for smaller MRFs and smaller communities across the province.
He says questions that should be asked include: how do we protect some of the smaller facilities that are out there? For some of the MRFs that have been here for many years, how do we ensure minimal job losses?
"I don't get a good feeling currently as to where companies like ours fit in in the future of recycling in our Province, and that's a big challenge we're faced with."
Still, for Kraft, despite the uncertainty of the future, overall he remains optimistic. He can certainly attest to the fact that Niagara Recycling has had an incredible journey over its 41 years in business, diverting more than 1.5 million tons of recyclables from landfill, and providing huge benefits to their region.
"Life is full of uncertainty," he says. "But I am optimistic we will find a new place in the future, and that we'll ensure continued job opportunities and support for developmentally challenged individuals in our community." RPN
This article was originally published in the April 2019 edition of Recycling Product News, Volume 27, Number 3.