Langille’s continues to build on experience recovering heavy-duty electric- powered vehicles
No small task: Latest hybrid transit bus recovery contract a sign of big things to come
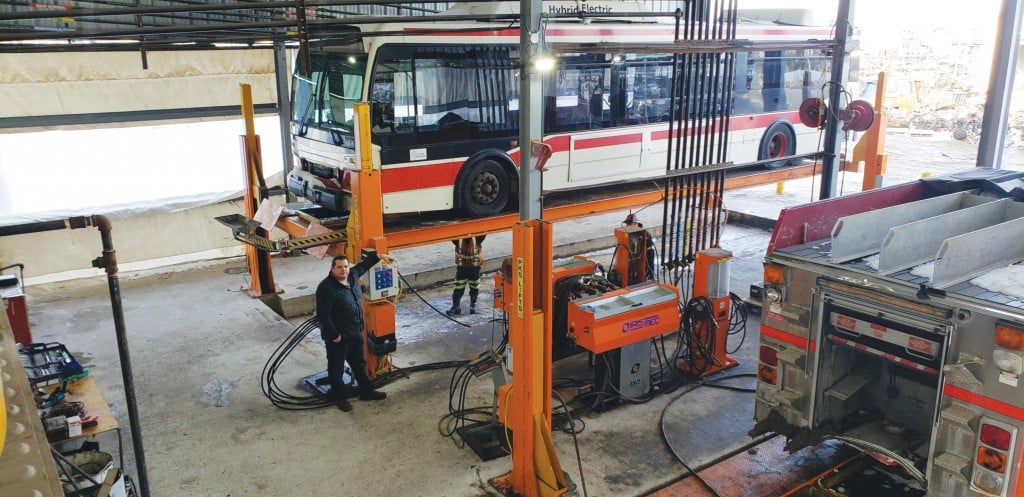
Dave Langille started in the scrap metal and auto parts business as a peddler in the late 1980s, working out of a pickup, collecting and selling cores and scrap metal, same as his father and grandfather before him. He was at it from his teenage years into the early 2000s, until in 2006 Langille purchased an auto-wrecking yard in Port Perry, Ontario (about 50 kilometres north-east of Toronto) and established Langille's Scrap & Cores.
He subsequently bought a neighbouring yard in 2008, another neighbour in 2009, and then bought the family's auto wrecking yard, owned by his brother, on the same street. Today Langille's Truck Parts and Langille's Metal Recycling together comprise about 12 acres and over 60 employees, with the primary business being the recycling of heavy trucks and heavy-machinery cores, including engines.
"We probably have 3,000 diesel motors in stock at any given time here," says Langille, adding that while he considers himself to be an end-of-life vehicle processor primarily, they also handle auto and heavy truck parts and cores, and are a busy scrap metal recycler through Langille's Metal Recycling.
Langille's processes upwards of 80 to 100 light-duty vehicles per week (up to the size of a Ford F550), or about 5,000 per year. Incoming vehicles have valuable cores and parts removed for resale and scrap vehicles are de-polluted, then baled and sent to the shredder for recycling. For heavier class trucks, they process closer to 3,000 per year, and they see a wide range of other large vehicles, including transit buses and heavy equipment ranging from wheel loaders and excavators to construction cranes. He says the biggest single vehicle they have ever processed was a 190-ton Euclid mining truck.
Recycling electric
Recently, Langille's took on a contract with a large local transit commission to process close to 400 hybrid diesel-electric powered buses. Prior to the current contract, Langille says, over the years they've gained experience with this particular niche, having processed close to 50 fully electric or electric-hybrid commercial vehicles.
"On a fully electric vehicle, the environmental and hazard considerations are not quite the same as for a gas- or diesel-powered vehicle," explains Langille. "You still have brake and cooling fluid to deal with, but you don't have the oil, gasoline or diesel fuel. You are dealing with high-voltage batteries however.
"On a hybrid vehicle, there's more environmental considerations because you have all of the components of a gas or diesel vehicle, as well as the high-voltage electric battery components."
Langille says they have built custom processes into their operation to handle hybrid diesel-electric buses in particular, and had extensive consultation with the local transit commission as well as BAE Systems (the OEM which makes the hybrid drives used on the buses they are processing).
"There's a whole procedure for dealing with EVs (electric-powered vehicles)," explains Langille. "We start with disconnecting and removing the diesel engine batteries. We then have to wait for a period for safety, because they have capacitors in them that carry high voltage."
He emphasizes that the EV batteries they are dealing with are usually roof-mounted and encased in a very heavy-duty casing, and so are not necessarily hazardous to remove or store. But Langille's still takes extra safety precautions due to the high voltage, using specialized PPE (personal protective equipment) and tools for the job, and targeted training for employees, including electrical safety and working at heights.
"The hybrid bus batteries we're currently working with are 680 volts at 2,250 amps. It's a lot," he says, adding that the transit commission and BAE have been great to work with so far on the current contract.
"BAE had four guys came up from their manufacturing facility in New York state, visited us, shared all information that we needed. They were really good."
Still, there are challenges with electric batteries, particularly when it comes to end markets. One of the biggest issues from Langille's perspective as a recycler, is that there's not enough standardized voltage, amperage and BMS (battery management systems) used in manufacturing.
"All the manufacturers are building using different voltages and BMS," he says. "Our research tells us that these batteries, when they come out of an end-of-life EV or hybrid electric vehicle, may have between 60 and 80 percent life left. When they're taken out of the EV situation and put it into backup power, standby power or solar power, whatever they are used for, they could have as much as 30 years capacity left in them.
"But the issue is, the BMS, inverters and electrical components needed to put used batteries into a new application, while they are available, are not available at a mass production cost, like standardized voltage and BMS components would be.
"It's not like every battery that comes out of a hybrid-electric-powered bus is 680 volts," he continues. "We've done commercial vehicles in the past that were 440 volts. Everything's different."
Because there's no standardized voltage and BMS, he says end-buyers can't just plug and play into readily available inverters and equipment that is generally used for solar power generation or other applications. But there are definitely potential markets for used EV batteries. In China, for example, he says he knows of a company with the goal to take millions of recycled batteries out of end-of-life vehicles to use as backup power for cellphone towers.
Overall, the process would work better if design for recycling policies were improved - if all the OEMs started thinking more about what's going to happen at their products' end of life, and started using standardized BMS batteries and voltages.
"If every electric-powered heavy vehicle and hybrid vehicle used 600 volts and a standardized BMS, for example, now it's going to be feasible for the companies that manufacture inverters and different components for use in solar and wind power generation to manufacture at a mass-production-based cost. Then, with recovered EV batteries, end users just plug and play. It's that simple."
He says he believes it will happen eventually. "From the OEMs that we've spoken to about it, they said that they wished it had went that way. Not because of recycling, but because it would be cheaper to come to market with a product if everybody's using the same design. Many major auto and heavy equipment manufacturers already work this way.
"Every piece of Caterpillar equipment uses a 24-volt battery, Komatsu takes a 24-volt battery. There's a reason that big manufacturers have gone that way, because if you use a component that is specialized for your particular application, it costs you more to source."
The EV bus recycling process
When Langille's starts processing a hybrid-electric-powered bus, they use a custom-built de-pollution setup and an Iris-Mec drainage system they bought through local equipment supplier Recycling Equipment Canada.
"We have two 100,000-pound hoists and we use all Iris-Mec vehicle de-pollution equipment," says Langille. "A bunch of it was custom built because we had to add extra pumps. We also have a 20,000-gallon tank farm for collected fluids."
When a hybrid-electric bus comes in, similar to any other vehicle, once batteries and electronics are disconnected and removed, de-pollution is the next step.
"We pull all the fluids out, but before it gets de-polluted, our guys remove the diesel engine batteries which is part of de-electrifying the vehicle. We also remove the hybrid-drive batteries and all the high-voltage stuff prior to dismantling."
"Then they ‘get hit on the head,'" he says, meaning they pull out the drivetrain.
Once Langille's crew has removed the core items, all resalable and fluid-filled parts, including diesel engines and all electric battery components, what is left - mostly ferrous and other metals, as well as glass, rubber, wood and plastics - is ready to be cut into pieces. They use excavators mounted with shears to remove the bodies and cut the chassis, and smaller excavators and wheeled material handlers with grapples to sort and move material.
Specifically, Langille's uses a 350 Komatsu excavator with a 2500 Labounty shear on it and a 490 Komatsu with a 4000 Labounty shear. They also use a smaller 228 Komatsu with a Bateman grapple and a 138 Komatsu mini-excavator with a picker attachment for sorting and for handling nonferrous, such as the aluminum body panel of a truck or bus. Once the bus is dismantled, Langille uses two Liebherr dedicated scrap handlers - a 924 HD and a 934 HD - to get material from the dismantling phase to their Sierra CR 6000 logger/baler.
With respect to specific recyclable materials they are pulling out of a bus, at Langille's it is mostly ferrous metal. There is some copper cable, aluminum, and there are a lot of seats, which are mostly plastic and steel. There's also a lot of additional plastics, fibreglass, as well as wood and rubber in a bus.
"The floors are all wood and rubber," Langille says. "They use about 3/4-inch pressure-treated wood with rubber on top. We take all of that out as well and everything outside of metals, for the most part, is sent to the transfer station for further sorting or disposal."
Ontario ELV regulations and EASR
Since 2016 in Ontario, end-of-life vehicle processing facilities fall under EASR (Environmental Activity and Sector Registry) regulations. EASR provides a public, web-based system that allows businesses conducting certain activities to register with the Ministry of Environment & Climate Change, rather than applying for environmental approval, which is a much more complicated, costly and time-consuming process.
Under EASR all auto recycling facilities and operations in Ontario (processing more than two ELVs per year or holding more than ten) are required to register. And anyone processing ELVs (no matter how many) now needs to meet a specific range of requirements and operating standards.
These new requirements include the mandatory collection of operating fluids (gasoline, oils, windshield washer fluid, antifreeze and refrigerants) removal of tires and batteries for recycling, plus the management of substances of concern such as lead, mercury and asbestos. Under EASR, de-pollution of vehicles also needs to take place on an impermeable surface under cover from the elements, and waste removed from vehicles needs to be properly stored, re-used or removed offsite to an accredited recycler. There are also educational and reporting components to the standard.
According to Steve Fletcher, managing director of the Auto Recyclers of Canada (ARC), of which Langille's is a long-time member, EASR includes a modernization of established policies and regulations for ELV processors, and is essentially a simplified environmental compliance tool.
"It's a checklist-based approach that assumes that about 98 percent of the legitimate players in a given sector are already meeting or can feasibly meet the requirements. For us the incorporation of ELV processing into to the EASR system has been very positive," says Fletcher.
Up until 2016, he says, under the Canadian Auto Recyclers Environmental Code of Conduct, which was in part developed and managed by ARC, there were lots of rules for the sector, but they were spread around. "Many in the business were unsure about the rules and regulations that applied," says Fletcher. "Now with EASR it's all in one place."
Langille agrees that the new regulations were needed.
"We don't want to make our living off of the environment," he says. "I always joke with my guys that ‘we're saving the world one ELV at a time.' For us, it means spending the money to be in compliance."
Langille says specifically that they have invested about two million into their state-of-the-art de-pollution setup, between their heavy-truck and light-duty operations.
"Our light-duty system is being built as we speak," he says. "It has four bays with four 18,000-pound side load hoists, using Iris-Mec de-pollution equipment on each bay. We also use a 20,000-gallon tank farm, a 300 CFM air compressor, and industrial HVAC pumps so we can remove refrigerant quickly.
"At the end of the day, you have to invest the money into the right equipment and processes to be in the business and stay in the business."
But while the EASR system helps to create a more level playing field for ELV recyclers, and it is now essentially against the law in Ontario to crush or shred a vehicle that has not been de-polluted properly, there are still those in the industry that continue to look at an ELV as scrap on wheels, and who operate without compliance to the regulations.
According to Langille, this is the biggest challenge with the new regulations - its enforcement with those that are "flying under the radar" so to speak, and who are "wrecking cars out behind a barn somewhere."
"Those that are operating outside of the program - those are the guys where they need to enforce the regulations," he says. "We're complying, we're spending the money. In 2018 we generated about 250,000 litres of waste fluid, not including gasoline and diesel that we recycle on site. So that number is probably 500,000 litres of weighted fluids that we generate here overall in a year.
"Half a million litres is not a drop in the bucket. It has to be properly managed."
For an operation like Langille's which tends to deal more in heavy trucks, buses and a lot of bigger equipment, it's definitely more costly to meet some of the provincial regulations, compared to others in the industry, simply due to the size of vehicles they are processing.
One of the key regulations, for example, is the requirement that all drainage and dismantling be done under a cover, on an impermeable surface. Wet parts, like engines and transmissions also need to be dealt with fully under cover.
For Langille's, some of the vehicles they are dealing with, including the EV hybrid buses currently, are quite simply massive, as are the volumes they are seeing. This means their setup needs to be big enough and sophisticated enough to accommodate the task at hand.
Fletcher provides an example of the comparative scope of what Langille's is doing. "When you de-pollute a car, there may be five litres of oil to account for," he says. "When you de-pollute a highway truck, there may be 100 litres.
"Langille's is doing things in a bigger way than most," he continues. "When it comes to electric-powered and hybrid vehicles, many of our members might deal with one EV per week, and have some batteries stockpiled. But Langille's is being provided big volumes with a steadiness and a commonality to it."
Fletcher definitely considers Langille to be well ahead of the curve on both heavy truck and electric-powered vehicle processing.
"I've never seen the kind of volumes he does on heavy vehicles," he says. "Most don't see things as a trend until it overwhelms. Dave Langille has planned for being overwhelmed and he is managing very, very well." RPN
This article was originally published in the March 2019 edition of Recycling Product News, Volume 27, Number 2.