Calculating true capacity before buying your next trailer
Between the Road and the Load
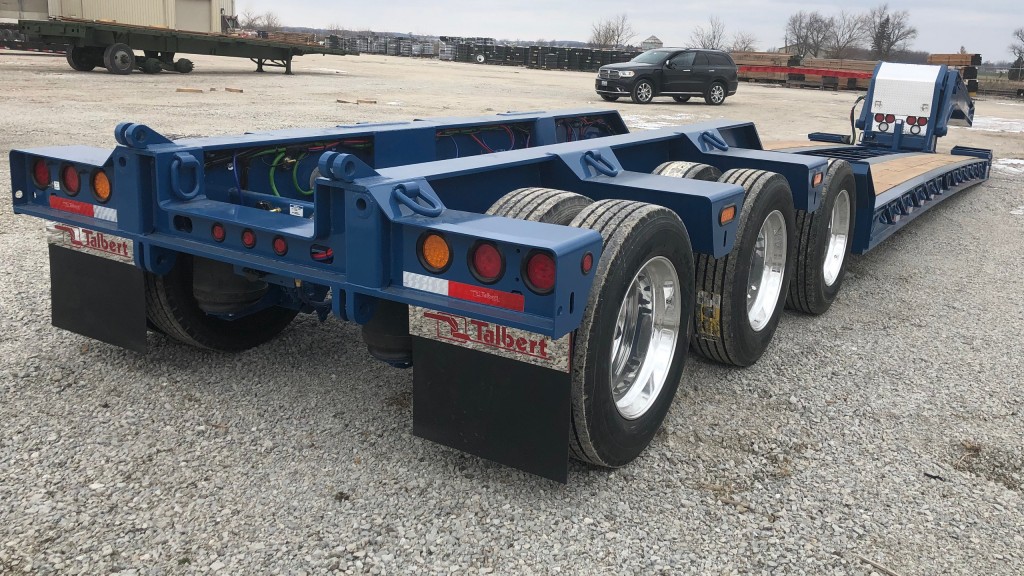
Long before a single load is booked or any wheels turn, someone - usually a fleet manager - needs to determine exactly what is going to separate the road and the load. There's a lot riding on this decision because, as much as some would like to think otherwise, a trailer is never just a trailer. It can be manufactured to many different specifications, with multiple raw material options, dozens of load and geographical considerations, various top speed requirements and hundreds of possible axle configurations coming into play. And it all comes down to one objective - the ideal trailer for an operation's specific loads.
To select the right trailer, the one that will require the least amount of maintenance, provide the greatest lifespan and deliver the highest possible return on investment, it is vital to understand the most important factor of all - capacity.
50 Tons in the Making
There are five contributors to capacity ratings. They apply to any kind of open trailer, from flat and step decks to lowbeds, and each can be varied to meet a carrier's specifications.
It begins, of course, with the materials used to build the trailer, specifically their sizes and weights. From there, capacity encompasses the overall weight that a trailer can carry, the area of the deck in which it can carry that weight, the speed at which the trailer will generally travel and the safety factor.
To make an apples-to-apples comparison, consider one 50-ton lowbed alongside another 50-ton lowbed. Because, just as a trailer is never just a trailer, not all 50-ton lowbeds are created equal.
Load Concentration: Half Deck, Full Utilization
There are more than 50 manufacturers of lowbed heavy-haul trailers in North America, and they apply several methods of rating the capacity of their trailers. Since there is no industry-set or government-mandated system, it's up to every buyer to be in tune with the method each manufacturer uses before making a purchase decision.
A key difference between manufacturers' ratings comes in load concentration, or the length of the deck that can handle the rated weight. Obviously, a 26-foot, 50-ton lowbed can haul 50 tons. But how much of the deck those 50 tons occupy is just as important as the weight itself. Whereas one trailer might need the entire length of the deck to be rated at 50 tons, another can be rated for 50 tons in a 16-foot span, and another can handle that same weight in half the deck length.
For example, a 26-foot, 50-ton lowbed might be rated for the trailer's entire span with equal weight distribution. In that case, the trailer would need to be hauling materials that run the entire length of the trailer, such as long steel poles, lumber or concrete culvert sections.
However, if the payload is a 100,000-pound excavator that's only 13 feet long, a trailer rated for the entire deck length, or even for 16 feet, won't be right for the load. Even though the load is only 50 tons, that trailer will be overloaded because the weight will not span the entire length of the deck; making it too concentrated for the area the excavator covers. For a trailer that's rated at full deck length or 16 feet to safely handle the excavator, it would likely need to be rated at 55 or 60 tons.
So again, using the 13-foot, 100,000-pound excavator as the payload, the ideal trailer will be one rated at half the deck length. Trailers rated for half the deck length can carry a specified load in just that, half the length of the deck. These ratings give a more realistic indication of the concentrated loads the trailer will be able to handle safely and without structural failure. In addition, manufacturers who build trailers with half-deck ratings often do so with a two-point rigid load base specifically for the tire spacing, or hot spots, of large equipment and heavy machinery.
Load Distribution: Scaling Out
How a load is distributed over the deck and the axles can be just as important as the overall weight rating. However, even though the trailers will be operating in the United States, the states are not very united when it comes to axle weight laws and regulations.
All across the country, the laws and regulations related to weight change from state to state. Companies operating in Indiana deal with one set of laws and regulations, but when they cross the border into Ohio they run into entirely different set of regulations. Pennsylvania has yet another distinct collection of rules of the road and so on along the truck's route.
Fleet managers need to be aware of, and plan for, variances between states and regions where their trailers will be used. It's important to have the proper trailer configuration to make the load distribution work for a fleet's particular area of operation. Manufacturers bear some responsibility, too, and should work with buyers to define not just the best trailer for the cargo those buyers will be carrying, but also the best axle configurations for maximizing the load in every one of the states they'll be hauling through.
Clearly, it's impossible to max out a trailer's capacity in every state, but the goal of most interstate heavy-haul carriers is to get a trailer as close to the maximum as possible across all the states where the carrier intends to operate.
There are many ways to achieve the best possible weight distribution over the axles. It may be as simple as adding a fourth flip axle or as complicated as adding two or three axles and spreading them apart to make sure they can each accept an equal amount of weight from the payload. And there are other possibilities in between depending on the specific state's regulations and the nature of the load.
For example, carriers can vary gooseneck lengths in the front to achieve the proper steer weight and drive axle weight. Carriers also can alter the distances between axles and axle groups to hit max weights and remain in compliance with various state laws. With an East Coast trailer, for example, they can add shims to a rigid spread bar or, if the trailer has a nitro version of a spreader bar, use hydraulics to vary the weight distribution. Yet another way is to move the load closer to one end or the other to properly distribute weight over the axles. And, finally, a carrier can use a jeep dolly to add extra axles, thereby lowering the per-axle weight distribution.
Speed: How Slow Can You Go?
Another capacity determinant is speed. While some manufacturers rate their trailers at 55 mph, others rate them at 65 mph. The slower a rig travels, the less added weight or stress is placed on the trailer. That's due to the fact that, while road dynamics such as potholes, railroad tracks and so on still come into play, the impact on the trailer decreases along with the speed. However, sometimes a 55 mph rating is not as realistic for a carrier as a 65 mph rating. The key is to purchase trailers that will perform at a fleet's normal operating speeds.
Safety: A Crucial Multiplier
A trailer's safety rating also comes into play when discussing capacity. Without understanding the safety rating, it's difficult for a carrier to get a clear, comprehensive picture of true capacity.
A safety rating is an indicator of how much stress a trailer can safely handle. It encompasses the strength of the raw materials and components that a manufacturer has put into the trailer's design and construction, how the beams and cross members are configured and so on.
A widely accepted average magnification of payload weight on a trailer due to road dynamics is 1.8 to 1 ratio. When a driver is rolling down the road, the truck is hitting chuckholes, bouncing over bumps and crossing railroad tracks along the way. On average, the stress placed on a 50-ton-rated trailer by a 50-ton load when the rig hits those bumps, chucks and tracks equals 1.8 times 50 tons, or 90 tons.
It's important to keep in mind that the 1.8 multiplier is only an average. On any given haul, the stress placed on the trailer can go above that level multiple times. If no cushion is built in to the trailer to handle those spikes in stress, there will be more potential for long-term, progressive structural damage.
Since there is no universally prescribed level for safety ratings, they vary from manufacturer to manufacturer. They range from a safety factor of 1.8 to 1, which allows for no margin, to an industry high of 2.5 to 1, which is considered an ample cushion for even the most extreme road dynamics a trailer might encounter.
Not only does the safety rating tell a carrier how strong his trailer is, it's also a very good indicator of potential life. The greater the difference between the static design safety factor, be it 2.5 to 1, 2 to 1 or some other factor, and the dynamic 1.8 average multiplier, the longer one can expect a trailer's useful life expectancy to be.
Most trailer manufacturers do not like to advertise safety ratings, often for good reason. To understand why, it's helpful first to comprehend what a safety rating is not. A safety rating should never be used to determine how much weight can be added over the capacity rating and still keep the load, the driver and other drivers safe. In other words, a 2.5 to 1 safety rating on a 50-ton lowbed should not be used to justify loading a trailer with 125 tons of cargo. Just as the deck rating indicates, that trailer can safely handle a 50-ton payload under dynamic conditions.
Materials: The Sum of the Parts
Safety factors are strongly related to the quality of the components incorporated into the trailer, and that gets down to the nitty-gritty of the steel and the deck material.
Manufacturers have several options when choosing steel. For the most capacity and smallest impact on the trailer weight, some manufacturers use a T1 material with 100,000 psi minimum yield. T1 not only has maximum strength versus ductility, but also equates to a lighter, stronger trailer frame over other materials.
A trailer's decking is continually exposed to the elements, making durable decking with a long wear life also crucial. Apitong decking provides a tougher, longer lasting wood in comparison to other varieties, such as oak or pine. Tightly woven and incredibly dense, apitong is less susceptible to chipping and cracking and provides some amount of traction in comparison to a smooth metal surface.
Overload at Your Own - and Others' - Risk
Sometimes trailer owners or operators don't completely understand the capacity rating and mistakenly put more weight on the trailer than it is built to handle, or more weight in a concentrated area than it can handle.
Overloading a trailer once is not likely to make it break. Overloading it twice probably won't either. But do it consistently over time and eventually it will likely fail.
When a trailer breaks, the manufacturer hears about it. But often the complaint will be that a 50-ton trailer broke when it was hauling less than a full payload. For example, a 50-ton trailer might break when it's only hauling a 40-ton payload. The reason is not in that 40-ton load, but the number of times the trailer previously was overloaded and by how much each overload exceeded the yield strength of the trailer's load-bearing beams and cross members.
Yield strength refers to the amount of stress that the steel can withstand and still return to its original shape when unloaded. The first time a trailer is overloaded, the steel will return to something close to the shape it was in when it came off of the manufacturing line, but not exactly to that original shape. Each time it's overloaded, the steel will return to something less than the shape it was in the time before. Eventually, the steel, and therefore the trailer, will break.
So in our example, even though the trailer only carried a 40-ton payload, it is likely that it had been overloaded to some extent at one or more points in its past. That's when the damage was done, and that is what ultimately caused the failure. The steel got weaker and weaker and, on the day the trailer failed, it happened to be rolling with 40 tons on the deck.
Help To Be Had
It can be tempting to look at a trailer's capacity rating and stop there. But for a true sense of how much a trailer can handle and how it will hold up under the stresses of a specific operation, with its individualized loads, geographies, weights and other variables, fleet managers need to consider everything that goes into that rating.
Purchasing the right trailers for updating a fleet can be complicated and, clearly, the decision is an important one. But there is help available. Many manufacturers have sales people who know capacity from top to bottom and can help fleet managers select exactly the right trailer with the optimal combination of load concentration, load distribution, speed and safety rating for specific applications and load types.
And having that knowledge about each specification will help ensure an investment that leads to a long, smooth ride.
Troy Geisler is the vice president of sales and marketing for Talbert Manufacturing. He has more than 10 years of experience in trailer sales, including three years with Talbert. Troy earned his bachelor's degree from Purdue University in West Lafayette, Indiana.