Advanced technical solutions can substantially reduce occurrence and mitigate cost of fire incidents in waste and recycling
In the line of fire — technology’s role in facing an epidemic
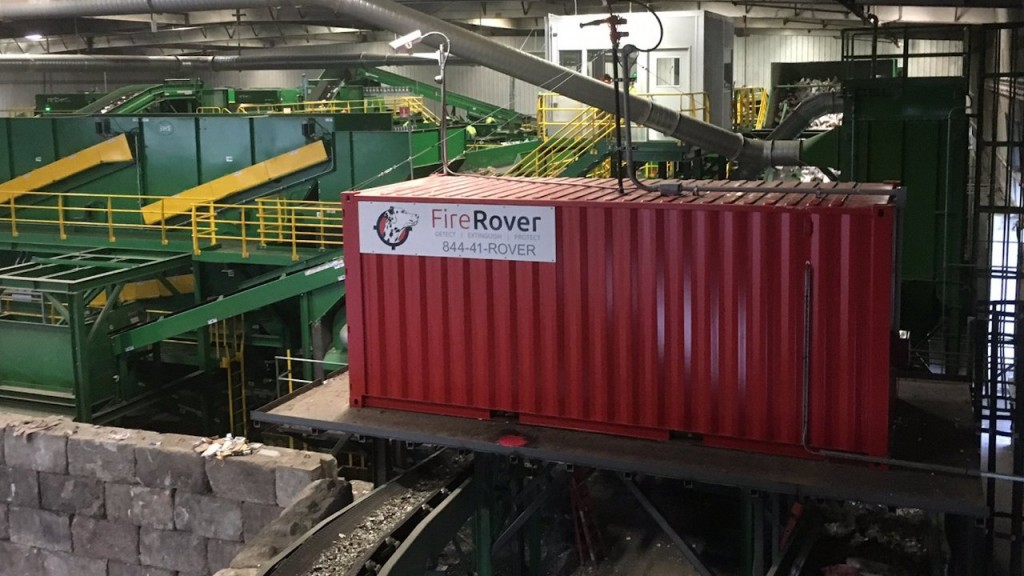
We have seen a spike in fires in the recycling industry in 2018, compared to previous years. March, April and May 2018 are now the highest months we have recorded for fire incidents at waste and recycling facilities. March 2018 could merely be an anomaly. But then came April, with 36 fires, and then May, with 38 fires reported - the highest number of fires in any month since I began reporting recycling and waste industry facility fires in 2015.
There are multiple factors that are contributing to this increase. For example, there has been a large increase of lithium-ion batteries into the waste stream. There has also been an increase of material stock in facilities, in part due to China's recyclable materials import restrictions, as well as warmer/drier-than-usual weather compared to previous years. It should be noted as well that there has been an increase in reporting and public awareness of fire incidents in all industries.
In the past 12 months, we have recorded 368 unique reported waste and recycling facility fire incidents in the U.S. and Canada. When you factor in my extremely conservative assumptions that we are under-reporting waste and recycling facility fires by about 5:1, we are looking at a reasonably estimated current number of fire incidents in the U.S. and Canada at approximately 1700+ yearly.
In our industry, whether processing metals, plastics, waste, chemicals, C&D, paper, e-waste, rubber, organics or hazardous materials, we have numerous inherent spark-developing dangers. This includes the presence of a range of explosive and combustible materials in mixed waste (hot loads), loader buckets scratching concrete, sparks from shredders and other large equipment, and large stockpiles of materials.
There are things the industry can do to alleviate the risk, including improving basic housekeeping and staff/public education. We can also increase investment in the most up-to-date fire protection and suppression technology, which means going beyond the fire alarm and sprinkler.
Seasonal factors and hot loads
Seasonal factors are important to note. Since we have started tracking fire incidents at recycling facilities and scrapyards, we have recorded an increase in fire incidents during the summer's warmer and drier months, as well as holiday spikes due to increased amount of materials being processed at the end of each calendar year.
Industry expert Jim Emerson provides his theory of what can cause an increase in summertime hot loads - which are created by the mixing of a wide range of combustible and explosive materials, including charcoal, fireworks, fertilizers, chemicals, batteries and more, along with organics, in a given load of material. Emerson says that because many waste generators today are putting waste in plastic bags, often sealed, the mix of material in those bags creates what are essentially millions of mini compost ovens.
"These bags sit there getting hotter and hotter," says Emerson. "They get put into compactors, dumpsters and trucks, squeezing them closer and closer together, and there is an aerobic compost process in motion. The current system is bringing a lot of heat sources close together, resulting in an ever-increasing heat feedback cycle. The temperatures have nowhere to go but up."
He adds that in summer, there is also generally more material in the waste stream from summer home improvement projects, including oil change rags, discarded paints, chemicals, aerosols, etc. When this mix of material is dumped on the tipping floor it is loosened up, says Emerson, just enough to allow the inflow of more oxygen, and increasing the possibility of material being hit with a spark from a loader bucket hitting the concrete, for example.
"This is just what material needs at the moment it needs it, to convert into a deep-seated fire," says Emerson.
The Lithium-Ion Battery factor
The increase in lithium-ion batteries in our waste stream has created the perfect storm for fire incidents. These batteries are becoming less expensive and more powerful, and are steadily increasing in number. This creates more potential fire hazard issues for the waste and recycling industry. According to Cameron Perks, a consultant for Industrial Minerals, "forecast demand for lithium-ion batteries is expected to increase up to seven-fold by 2024."
So, why do lithium-ion batteries have such potential to cause fires? According to Paul Shearing, a chemical engineer at the University College London, "Batteries can blow up or melt when internal electrical components short-circuit, when mechanical problems crop up after a fall or an accident, or when they are installed incorrectly."
Imagine the existing waste and recycling life cycle from trash to final separation. There are an infinite number of danger points where damage can occur to a tiny lithium-ion battery, increasing the risk of a mini explosion.
So why don't we just recycle all lithium-ion batteries? In practicality, they are so small that they can sneak into many places where they do not belong, and chances are high that the batteries are going to be damaged when being exposed to the "rough and tumble" environment of waste and recycling facilities. When these mini-explosions occur, out of sight or after hours, they can cause significant damage.
Layers of protection
So what happens when a fire incident occurs at a recycling operation? If it is caught and contained, everyone can breathe a collective sigh of relief. Alternatively, what happens if a fire occurs at a recycling operation and the fire gets out of control, causing significant damage?
As an industry, for us to begin to solve the problem we are facing, we are well-served to borrow an approach used by the chemical industry that looks at layers of protection to ensure the highest level of safety.
From an article by Joy LePree published in Chemical Engineering Online, figure 1 (above) shows these layers of protection. The lowest two layers show the areas of prevention provided by the control system and operator intervention. The next two layers demonstrate where technology kicks in to prevent significant disaster from occurring.
A typical "Active" protection layer consists of water sprinklers that are automatically set off when radiant heat passes 165 degrees. More often than not - they contain the fire. However, operations are temporarily offline. The cleanup process is sprung into action to restart the revenue-generating operations of the business with the goal of having the shortest amount of downtime. Subsequent investigation begins as the management team starts to search for answers to what went wrong. Sometimes backroom discussions and finger-pointing might begin, typically concluding that a combination of the Operations and EH&S Departments at the organization need to develop better processes and training to avoid future incidents like the one that has occurred.
The fact is that fire incidents that continue to plague the waste and recycling industry do not discriminate against poorly run operations. Some of the best operators in the industry are still victims of fire incidents.
Why? The answer lies in the fact that most organizations focus the bulk of their operational and safety resources around the "Prevent" and "Mitigate" stages. They create processes and training programs that teach their employees how to use equipment and run their operations safely. Also, they train how to effectively deal with an emergency by finely balancing containment and response with employee and environmental protection. But how effective is the actual fire prevention and suppression system itself?
The Fire Rover system
Every fire incident has different costs, but outside of the obvious direct costs due to damaged equipment, building and materials, there are the indirect costs of downtime, insurance increases, fines, penalties, public exposure and more. Recently, a colleague of mine mentioned that in the case of a fire they experienced, their insurance premium increased from $150k per year to over $1M per year. They were also told that if they have another incident in the subsequent 24 months, their facility would be uninsurable.
When it comes to using technology, most organizations use options that come standard with equipment, such as automatic sensors and shutoffs, along with fire alarms, strobe lights and water sprinklers. For fire in industrial applications, this technology simply does not cut it. Developing standard operation and safety processes and procedures, while important, can only take a facility so far in lessening the risk of fires.
An effective fire technology solution, such as the Fire Rover system, works diligently to provide a safety system that has the primary function of preventing incidents that may cause unplanned business interruption, property damages, pollution and/or injuries. A proper solution should be designed to detect an out-of-control process and take automatic action to ensure that the process and the plant are returned to a safe state. The solution should encompass a combination of proactive automated detection of excessive heat and its location; manual verification of the source of the abnormality; and on-site remotely operated coolant options to eliminate and contain the threat.
The Fire Rover solution does all of this. It rapidly identifies fire in its incipient phase, alerts all forms of emergency response and initiates containment with coolant/pre-wetting options before the growth stage is realized. This leads to multiple benefits including improved employee and fire-fighting personnel safety, and because fire is detected in its earliest stage and is pre-wetted and cooled, it allows time to set up hoses, nozzles and connections to a water supply. Plus, heat buildup beneath structural elements is reduced along with smoke development. Additionally, the technology allows a fire service to locate the seat of the fire swiftly and surely.
By using this kind of advanced fire detection and suppression system, fire footprint is exponentially reduced, preventing unplanned downtime, costly damage and safety hazards.
The Fire Rover solution is a final layer of protection meant to compliment and function as part of the diligence and hard work that safety and operations teams have developed, maintained and worked to continuously improve upon.
With Fire Rover technology, we have shifted the focus from containment of a major fire incident once underway, to early detection and cooling of a fire incident. This solution seamlessly integrates military-grade thermal detection (not IR, flame or smoke detection) with remote human verification and on-site remote targeted application of its cooling/wetting agent.
The Fire Rover solution is currently installed in 100 waste and recycling facilities across the U.S. This solution has extinguished over 78 fires in the past 12 months at the sites we protect. We are protecting assets including tipping floors, in-feeds, equipment, rubber feedstock, scrap metal, hazardous materials and more.
The Fire Rover system typically catches most fires during the incipient, pre-incipient and smoldering stages, and we have not had one fire incident within a protected area that has grown to the Major Fire Incipient stage. In fact, most of our "saves" have resulted in little to no cleanup required and clients were able to continue their operations after the event. Additionally, Fire Rover technology includes a built-in fire watch, so there is no need to worry about risk of immediate reoccurrence or resetting the unit.
With the risks of inherent fire in the waste and recycling industry steadily increasing, especially when the materials we are processing are so unpredictable, we need to develop and install effective, advanced solutions that can mitigate fires as early in the process as possible. Proper fire detection technology works to compound the level of safety within organizations and can give EH&S and operations staff the right tools to meet their goal of No Fire Incidents. It fills the void between standard operations manual processes and proactive fire protection - providing the right combination of human knowledge and technology, working together for the greater goal of fewer fire incidents in industrial environments such as waste and recycling facilities.
Ryan Fogelman is vice president of national accounts for Fire Rover, Southfield, Michigan. He has been compiling and publishing "The Reported Waste and Recycling Facility Fire in the US/CAN" report since February 2016.
This article was originally published in Recycling Product News July/August 2018, Volume 26, Number 5.
Company info
6960 Orchard Lake Road, Suite 303
West Bloomfield, MI
US, 48322
Website:
firerover.com
Phone number:
844-417-6837