Making Safety part of the scrap business
Creating a positive safety culture in recycling means reducing risk
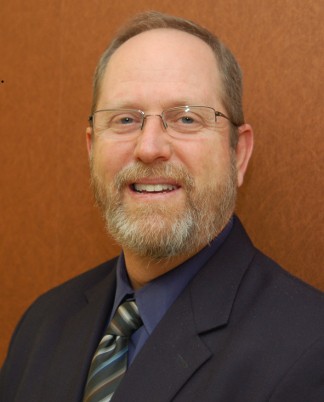
In April, while attending the ISRI 2018 conference in Las Vegas I sat in on an educational session titled "Implementing a Forward Looking Safety Program to Reduce Costs."
At the start of the session the speaker asked the group what the expression "good safety culture" meant to them. The answers varied from commitment and discipline to strength and leadership. I offered up to the group that I believed that safety culture is defined as the worst behaviour that your senior management is willing to accept. The management in this case can be the line supervisor, the plant manager, division manager, and even the company's ownership. The worst behaviour that these leaders are willing to accept is what is going to set the tone of the culture of that business. And because safety is an important part of any business the way that the leadership of a company looks at this issue will set the safety culture tone. Especially in the operations and maintenance sectors of a company.
Over the past decade the scrap recycling industry has seen a strong and continued focus on safety. The industry is known to be high hazard, and because of that all levels of the business have to be dedicated to the safety program in order for it to flourish and grow.
Commitment from the top down is a critical element to make safety work and to weave it into the fabric of the company. But often times there is a disconnect at the mid-level of management and downward when it comes to the company's safety goals. What exactly are the company's safety goals?
We have all heard a business use the words "zero injuries" or "zero accidents" as the number one safety goal. This is a fallacy that needs to be discussed. While achieving a zero accident and injury rate is an attainable goal, you must first realize that safety is not about the absence of injury. Safety is about the reduction of risk. Of course we should all be striving for a zero accident and injury rate, but if you take a moment and focus your safety program on hazard recognition and reduction of those hazards and risks, then the safety metrics (i.e. injury and illness rates) will begin to show favourable results.
Creating a positive safety culture
There are many different ways to create a positive safety culture in your business. The supervisor, plant manager, and the division manager play a big role in the success of a company's safety program. Getting tangible information to individuals that need it the most is important. Through education and training programs at your company you should be offering tools that are easy to relate to and understand for workers. "Tool box talks" or "tail gate meetings" are a simple yet effective way to bring safety discussions to line level employees. These tool box talk meetings are a three- to five-minute discussion on a legitimate issue that is currently, or has the potential to affect boots-on-the-ground employees. Most businesses and the working groups within them conduct operations meetings every morning to discuss the business of the day, (i.e., what is being shipped, received, etc.) so why not take an extra three to five minutes to discuss a safety issue that could educate the employees. You will also find that these meetings can educate the leaders of the business on what the daily issues in the field are. This is a win-win for any operation.
Another positive step towards an inclusive safety culture is to create and empower safety committees. A safety committee can be a big help in the development and promotion of the company safety program. The safety committee should be comprised of the working men and women who know the business at the operations and maintenance level. These folks are out in the operation every day. They have an understanding of how the business flows at the plant or worksite, and are the point of contact that can best help the safety program focus on matters in the field. Setting up self-inspection teams that are comprised of safety committee members can be a big help when it comes to hazard recognition and risk reduction.
Does your operation have a safety manager who is responsible for health and safety at your facility? Or, does your operation have a safety manager who is viewed as a resource to the business - because everyone is responsible for safety at the facility?
Safety should be part of everyone's responsibility. It is through management commitment, employee engagement, good education and training, as well as hazard identification and prevention, that we create a solid foundation for a safety program to build upon. A safe operation makes smart business sense.
The Institute of Scrap Recycling Industries will be holding its annual safety stand down day on Wednesday, June 13, 2018. On this day we are asking that businesses in the scrap recycling industries take at least one hour of their working day and dedicate it to safety leadership through hazard recognition or safety education and training sessions.
Tony Smith is ISRI's director of safety outreach. For more information, including resources, contact [email protected].
This article was originally published in the May/June 2018 edition of Recycling Product News, Volume 26, Number 4.