Is the recycling industry facing a fire epidemic?
With the risks of inherent fire ever increasing, solutions and technology needs to be considered that can mitigate, detect and manage fires
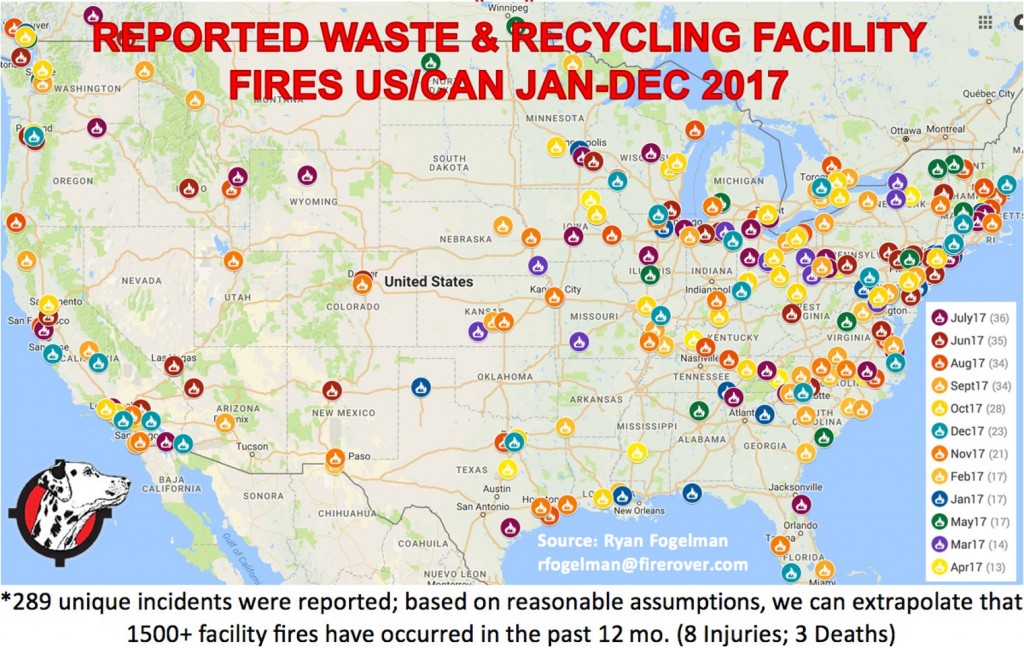
There is certainly no simple answer to the question: is there a fire epidemic facing the recycling industry? But it is an issue that needs addressing. The Merriam-Webster Dictionary defines an epidemic "as an outbreak or product of sudden rapid spread, growth or development." Although we have been faced with facility fires in the waste and recycling industry for years, we are just now seeing the real extent of the problem.
According to the NFPA (National Fire Protection Association) between 2009 and 2013: "U.S. fire departments responded to an estimated average of 37,000 fires at industrial or manufacturing properties each year, with annual losses from these fires estimated at 18 civilian deaths, 279 civilian injuries, and $1 billion in direct property damage." In an article written by Stephen Watkins, "Preventing the Five Major Causes of Industrial Fires and Explosions" which appeared in Occupational Health & Safety, February, 2017, he states that the five main causes of manufacturing and industrial fires are: (1) hot works; (2) dust explosions; (3) flammable liquids and gasses; (4) faulty equipment and machinery, and; (5) electrical hazards. Although these risks certainly need to be accounted for, there is a proliferation of unique risks that we face in our waste and recycling operations whether you are recycling or processing metals, plastics, waste, metals, chemicals, C&D, paper, rubber, organics or hazardous materials.
During 2017, I consolidated 289 "reported" fires— published by news outlets — at waste and recycling operations within the U.S. and Canada (see above). Based on my research, a number of factors and additional studies, including the number of fires at waste and recycling facilities within the UK, where between 2001 and 2014, there was an average of 332 documented fires at waste facilities[1] annually, it can be estimated that the number of facility fire incidents in the U.S. is well over 1,500 yearly. Referring to EREF's 2016 report, Municipal Solid Waste in the U.S., in 2013 there were 3,913 recycling facilities and 81 waste-to-energy facilities in operation. This means that more than 30 percent of waste and recycling facilities in the U.S. have experienced a fire incident within the past 12 months.
Lithium-Ion Batteries
If you look at the increase in lithium-ion batteries in our waste stream, it is the perfect storm for fire incidents. According to Cameron Perks, a consultant for Industrial Minerals, "forecast demand for lithium-ion batteries is expected to increase up to seven-fold by 2024." How this increase correlates to waste and recycling facilities fires is something that we honestly do not know, but what we do know is that at the very minimum there is an anecdotal effect."
First, we must ask why do lithium-ion batteries have the potential to cause fires? According to Paul Shearing, a chemical engineer at the University College London, "Batteries can blow up or melt when internal electrical components short-circuit, when mechanical problems crop up after a fall or an accident, or when they are installed incorrectly."
Imagine our existing waste and recycling lifecycle, from trash to final separation. There are an infinite number of danger points where damage can occur to a tiny lithium-ion battery, increasing the risk of a mini-explosion.
Why don't we just recycle lithium-ion batteries? In practicality, they are so small that they can sneak into a ton of places where they do not belong. The chances are high that the batteries are going to be damaged when being exposed to the "rough and tumble" environment of waste and recycling facilities. When these mini-explosions occur out of sight or after hours, they can cause significant damage.
The proliferation of lithium-ion batteries is only getting greater. Apple is going to add an estimated three billion mini lithium-ion batteries to the market alone with their new AirPod wireless headphones over the next 10 years.[2] German supplier Robert Bosch GmbH and Japanese battery partner GS Yuasa Corp. aim to sell a lithium ion battery by 2020 that slashes production costs in half and delivers twice the energy density of today's batteries.[3] The less expensive and more powerful they get, the more issues the waste and recycling industry will face, as the number of lithium-ion batteries increases.
Mitigate and Avoid Risk of Fire
In Stephen Watkins article, "Preventing the Five Major Causes of Industrial Fires and Explosions" (mentioned above), he suggests the steps that manufacturing and industrial organizations should embark upon to mitigate and avoiding the risk of fire. This includes: (1) Conduct a hazard analysis; (2) Establish fire prevention and emergency procedures; (3) Provide fire safety training; (4) Implement a regular housekeeping routine; (5) Inspect and maintain your equipment and systems.
I suggest that we add one more step to mitigating and avoiding fire risks. Add a level of proven thermal technology, including proactive detection and manual remote suppression to the safety & operations department's tool belt in order to drastically reduce the risk of a fire incident occurring at waste and recycling facilities.
What happens when a fire occurs at your operation? If it is a fire incident that is caught and contained, we all breathe a collective sigh of relief. "Pats on the back" are passed out for having the safety and procedural processes in place to successfully prevent a fire event from becoming a major incident. In simple terms, the safety and operations teams did their job, and processes and training worked.
Alternatively, what happens if a fire occurs at your operation and the fire gets out of control and causes significant damage? The "Active" protection layer typically consists of water sprinklers that are automatically set off when radiant heat passes 180 degrees—more often than not—contain the fire, protecting the lives of your employees and most of the building structure. However, in reality, your operations are offline. The cleanup process is sprung into action to re-start the revenue generating operations of your business with the goal of having the shortest amount of downtime. The subsequent investigation begins as the team starts to search for answers for what went wrong. The backroom discussions and finger-pointing begin, typically concluding that a combination the Operations and EH&S Departments of the organization need to develop processes and training to avoid another incident in the future like the one that occurred.
The inherent risk of fire in our waste and recycling industry operations is not secret. As an industry, for us to begin to solve the problem we are facing, we only need to borrow an approach used by the chemical industry that looks to the "layers of protection" to ensure the highest level of safety.
From an article by Joy LePree published on Chemical Engineering Online[4], figure 1 below shows these layers of protection. The lowest two layers show the areas of prevention provided by the control system and operator intervention. The next two layers demonstrate where technology kicks in to prevent significant disaster from occurring.
Lithium-Ion Batteries
If you look at the increase in lithium-ion batteries in our waste stream, it is the perfect storm for fire incidents. According to Cameron Perks, a consultant for Industrial Minerals, "forecast demand for lithium-ion batteries is expected to increase up to seven-fold by 2024." How this increase correlates to waste and recycling facilities fires is something that we honestly do not know, but what we do know is that at the very minimum there is an anecdotal effect."
First, we must ask why do lithium-ion batteries have the potential to cause fires? According to Paul Shearing, a chemical engineer at the University College London, "Batteries can blow up or melt when internal electrical components short-circuit, when mechanical problems crop up after a fall or an accident, or when they are installed incorrectly."
Imagine our existing waste and recycling lifecycle, from trash to final separation. There are an infinite number of danger points where damage can occur to a tiny lithium-ion battery, increasing the risk of a mini-explosion.
Why don't we just recycle lithium-ion batteries? In practicality, they are so small that they can sneak into a ton of places where they do not belong. The chances are high that the batteries are going to be damaged when being exposed to the "rough and tumble" environment of waste and recycling facilities. When these mini-explosions occur out of sight or after hours, they can cause significant damage.
The proliferation of lithium-ion batteries is only getting greater. Apple is going to add an estimated three billion mini lithium-ion batteries to the market alone with their new AirPod wireless headphones over the next 10 years.[2] German supplier Robert Bosch GmbH and Japanese battery partner GS Yuasa Corp. aim to sell a lithium ion battery by 2020 that slashes production costs in half and delivers twice the energy density of today's batteries.[3] The less expensive and more powerful they get, the more issues the waste and recycling industry will face, as the number of lithium-ion batteries increases.
Mitigate and Avoid Risk of Fire
In Stephen Watkins article, "Preventing the Five Major Causes of Industrial Fires and Explosions" (mentioned above), he suggests the steps that manufacturing and industrial organizations should embark upon to mitigate and avoiding the risk of fire. This includes: (1) Conduct a hazard analysis; (2) Establish fire prevention and emergency procedures; (3) Provide fire safety training; (4) Implement a regular housekeeping routine; (5) Inspect and maintain your equipment and systems.
I suggest that we add one more step to mitigating and avoiding fire risks. Add a level of proven thermal technology, including proactive detection and manual remote suppression to the safety & operations department's tool belt in order to drastically reduce the risk of a fire incident occurring at waste and recycling facilities.
What happens when a fire occurs at your operation? If it is a fire incident that is caught and contained, we all breathe a collective sigh of relief. "Pats on the back" are passed out for having the safety and procedural processes in place to successfully prevent a fire event from becoming a major incident. In simple terms, the safety and operations teams did their job, and processes and training worked.
Alternatively, what happens if a fire occurs at your operation and the fire gets out of control and causes significant damage? The "Active" protection layer typically consists of water sprinklers that are automatically set off when radiant heat passes 180 degrees—more often than not—contain the fire, protecting the lives of your employees and most of the building structure. However, in reality, your operations are offline. The cleanup process is sprung into action to re-start the revenue generating operations of your business with the goal of having the shortest amount of downtime. The subsequent investigation begins as the team starts to search for answers for what went wrong. The backroom discussions and finger-pointing begin, typically concluding that a combination the Operations and EH&S Departments of the organization need to develop processes and training to avoid another incident in the future like the one that occurred.
The inherent risk of fire in our waste and recycling industry operations is not secret. As an industry, for us to begin to solve the problem we are facing, we only need to borrow an approach used by the chemical industry that looks to the "layers of protection" to ensure the highest level of safety.
From an article by Joy LePree published on Chemical Engineering Online[4], figure 1 below shows these layers of protection. The lowest two layers show the areas of prevention provided by the control system and operator intervention. The next two layers demonstrate where technology kicks in to prevent significant disaster from occurring.
Lithium-Ion Batteries
If you look at the increase in lithium-ion batteries in our waste stream, it is the perfect storm for fire incidents. According to Cameron Perks, a consultant for Industrial Minerals, "forecast demand for lithium-ion batteries is expected to increase up to seven-fold by 2024." How this increase correlates to waste and recycling facilities fires is something that we honestly do not know, but what we do know is that at the very minimum there is an anecdotal effect."
First, we must ask why do lithium-ion batteries have the potential to cause fires? According to Paul Shearing, a chemical engineer at the University College London, "Batteries can blow up or melt when internal electrical components short-circuit, when mechanical problems crop up after a fall or an accident, or when they are installed incorrectly."
Imagine our existing waste and recycling lifecycle, from trash to final separation. There are an infinite number of danger points where damage can occur to a tiny lithium-ion battery, increasing the risk of a mini-explosion.
Why don't we just recycle lithium-ion batteries? In practicality, they are so small that they can sneak into a ton of places where they do not belong. The chances are high that the batteries are going to be damaged when being exposed to the "rough and tumble" environment of waste and recycling facilities. When these mini-explosions occur out of sight or after hours, they can cause significant damage.
The proliferation of lithium-ion batteries is only getting greater. Apple is going to add an estimated three billion mini lithium-ion batteries to the market alone with their new AirPod wireless headphones over the next 10 years.[2] German supplier Robert Bosch GmbH and Japanese battery partner GS Yuasa Corp. aim to sell a lithium ion battery by 2020 that slashes production costs in half and delivers twice the energy density of today's batteries.[3] The less expensive and more powerful they get, the more issues the waste and recycling industry will face, as the number of lithium-ion batteries increases.
Mitigate and Avoid Risk of Fire
In Stephen Watkins article, "Preventing the Five Major Causes of Industrial Fires and Explosions" (mentioned above), he suggests the steps that manufacturing and industrial organizations should embark upon to mitigate and avoiding the risk of fire. This includes: (1) Conduct a hazard analysis; (2) Establish fire prevention and emergency procedures; (3) Provide fire safety training; (4) Implement a regular housekeeping routine; (5) Inspect and maintain your equipment and systems.
I suggest that we add one more step to mitigating and avoiding fire risks. Add a level of proven thermal technology, including proactive detection and manual remote suppression to the safety & operations department's tool belt in order to drastically reduce the risk of a fire incident occurring at waste and recycling facilities.
What happens when a fire occurs at your operation? If it is a fire incident that is caught and contained, we all breathe a collective sigh of relief. "Pats on the back" are passed out for having the safety and procedural processes in place to successfully prevent a fire event from becoming a major incident. In simple terms, the safety and operations teams did their job, and processes and training worked.
Alternatively, what happens if a fire occurs at your operation and the fire gets out of control and causes significant damage? The "Active" protection layer typically consists of water sprinklers that are automatically set off when radiant heat passes 180 degrees—more often than not—contain the fire, protecting the lives of your employees and most of the building structure. However, in reality, your operations are offline. The cleanup process is sprung into action to re-start the revenue generating operations of your business with the goal of having the shortest amount of downtime. The subsequent investigation begins as the team starts to search for answers for what went wrong. The backroom discussions and finger-pointing begin, typically concluding that a combination the Operations and EH&S Departments of the organization need to develop processes and training to avoid another incident in the future like the one that occurred.
The inherent risk of fire in our waste and recycling industry operations is not secret. As an industry, for us to begin to solve the problem we are facing, we only need to borrow an approach used by the chemical industry that looks to the "layers of protection" to ensure the highest level of safety.
From an article by Joy LePree published on Chemical Engineering Online[4], figure 1 below shows these layers of protection. The lowest two layers show the areas of prevention provided by the control system and operator intervention. The next two layers demonstrate where technology kicks in to prevent significant disaster from occurring.
Lithium-Ion Batteries
If you look at the increase in lithium-ion batteries in our waste stream, it is the perfect storm for fire incidents. According to Cameron Perks, a consultant for Industrial Minerals, "forecast demand for lithium-ion batteries is expected to increase up to seven-fold by 2024." How this increase correlates to waste and recycling facilities fires is something that we honestly do not know, but what we do know is that at the very minimum there is an anecdotal effect."
First, we must ask why do lithium-ion batteries have the potential to cause fires? According to Paul Shearing, a chemical engineer at the University College London, "Batteries can blow up or melt when internal electrical components short-circuit, when mechanical problems crop up after a fall or an accident, or when they are installed incorrectly."
Imagine our existing waste and recycling lifecycle, from trash to final separation. There are an infinite number of danger points where damage can occur to a tiny lithium-ion battery, increasing the risk of a mini-explosion.
Why don't we just recycle lithium-ion batteries? In practicality, they are so small that they can sneak into a ton of places where they do not belong. The chances are high that the batteries are going to be damaged when being exposed to the "rough and tumble" environment of waste and recycling facilities. When these mini-explosions occur out of sight or after hours, they can cause significant damage.
The proliferation of lithium-ion batteries is only getting greater. Apple is going to add an estimated three billion mini lithium-ion batteries to the market alone with their new AirPod wireless headphones over the next 10 years.[2] German supplier Robert Bosch GmbH and Japanese battery partner GS Yuasa Corp. aim to sell a lithium ion battery by 2020 that slashes production costs in half and delivers twice the energy density of today's batteries.[3] The less expensive and more powerful they get, the more issues the waste and recycling industry will face, as the number of lithium-ion batteries increases.
Mitigate and Avoid Risk of Fire
In Stephen Watkins article, "Preventing the Five Major Causes of Industrial Fires and Explosions" (mentioned above), he suggests the steps that manufacturing and industrial organizations should embark upon to mitigate and avoiding the risk of fire. This includes: (1) Conduct a hazard analysis; (2) Establish fire prevention and emergency procedures; (3) Provide fire safety training; (4) Implement a regular housekeeping routine; (5) Inspect and maintain your equipment and systems.
I suggest that we add one more step to mitigating and avoiding fire risks. Add a level of proven thermal technology, including proactive detection and manual remote suppression to the safety & operations department's tool belt in order to drastically reduce the risk of a fire incident occurring at waste and recycling facilities.
What happens when a fire occurs at your operation? If it is a fire incident that is caught and contained, we all breathe a collective sigh of relief. "Pats on the back" are passed out for having the safety and procedural processes in place to successfully prevent a fire event from becoming a major incident. In simple terms, the safety and operations teams did their job, and processes and training worked.
Alternatively, what happens if a fire occurs at your operation and the fire gets out of control and causes significant damage? The "Active" protection layer typically consists of water sprinklers that are automatically set off when radiant heat passes 180 degrees—more often than not—contain the fire, protecting the lives of your employees and most of the building structure. However, in reality, your operations are offline. The cleanup process is sprung into action to re-start the revenue generating operations of your business with the goal of having the shortest amount of downtime. The subsequent investigation begins as the team starts to search for answers for what went wrong. The backroom discussions and finger-pointing begin, typically concluding that a combination the Operations and EH&S Departments of the organization need to develop processes and training to avoid another incident in the future like the one that occurred.
The inherent risk of fire in our waste and recycling industry operations is not secret. As an industry, for us to begin to solve the problem we are facing, we only need to borrow an approach used by the chemical industry that looks to the "layers of protection" to ensure the highest level of safety.
From an article by Joy LePree published on Chemical Engineering Online[4], figure 1 below shows these layers of protection. The lowest two layers show the areas of prevention provided by the control system and operator intervention. The next two layers demonstrate where technology kicks in to prevent significant disaster from occurring.
Investing in the Proper Technology
The fact is that fire incidents that continue to plague the waste and recycling industry do not discriminate against poorly run operations. Some of the best operators in the industry are still victims of fire incidents. Why? The answer lies in the fact that most organizations focus the bulk of their operational and safety resources around the "Prevent" and "Mitigate" stages. They create processes and training programs that teach their employees how to use equipment and run their operations safely. Also, they train how to effectively deal with an emergency by finely balancing containment and response with the employee and environmental protection.
The issue is our lack of investment and reliable technology available to protect our operations from the "Incident" stage. When it comes to using technology, most organizations use the options that come on the equipment, such as automatic sensors and shut offs. However, when it comes to the tools we use during the "Incident" stage, including standards such as fire alarms, strobe lights and even water sprinklers, the current technology available simply does not cut it.
The issue lies in the fact that developing operation and safety processes and procedures, while important, can only take you so far in lessening the risk of fires. An effective fire technology solution works diligently to provide a safety system that has the primary function of preventing incidents that may cause unplanned business interruption, property damages, pollution and/or injuries. This solution should be designed to detect an out-of-control process and take automatic action to ensure that the process and the plant are returned to a safe state. Unlike the options available in the past, the solution should encompass a combination of: • Proactive automated detection of excessive heat and its location • Manual verification of the source of the abnormality, and • Onsite remotely operated coolant options to eliminate/contain the threat.
This combinational solution rapidly identifies fire in its incipient phase, alerts all forms of emergency response and initiates containment with coolant/pre-wetting options before the growth stage is realized. This leads to multiple benefits including:
1. Employee and fire fighting personnel safety automatically improved. 2. Fire is detected in its earliest stage, something that is not standardized in this occupancy. 3. Fire is pre-wetted and cooled, allowing time to set up hoses, nozzles and connections to water supply. 4. Heat buildup beneath structural elements is reduced along with smoke development. This allows the fire service to locate the seat of the fire swiftly and surely. 5. Fire footprint is exponentially reduced, preventing unplanned downtime, physical damages and safety hazards.
This type of combinational solution is a living, breathing layer of protection meant to complement and work within all of the diligence and hard work that safety and operations teams have developed, maintained and continuously improve upon. Imagine if a surgeon only had humans (without the help of technology) available to keep us alive during a surgical procedure. Surely, the percentage of incidents during surgery would increase. Fire detection technology works to compound the level of safety within organizations and can give EH&S and Operations staff the right tools to meet their goal of "No fire incidents". It fills the void between the operations manual processes and proactive fire protection, with the right combination of human knowledge and technology working together for the greater goal of fewer fire incidents.
With the risks of inherent fire only increasing, we need to develop and install solutions that can mitigate the fires as early in the process as possible. Especially when the materials we are processing in the waste and recycling industry are unpredictable. Using a combinational approach to protection converts the fire situation from playing defense late in the game and deep in your own territory to winning the coin toss, going on offense, crossing the 50 and taking the game downfield. Two vastly different outcomes.
Ryan Fogelman, JD/MBA, is VP of Strategic Partnerships for Fire Rover. Ryan is focused on bringing solutions to market that can be implemented in the "First Sixty Seconds" of a fire incident. Ryan has been compiling and publishing the "The Reported Waste & Recycling Facility Fire In The US/CAN" data since February of 2015 and speaks regularly on the topic of scope of the problem, detection solutions and onsite proactive suppression solutions. He can be reached at [email protected].
[Notes]: 1. The CFOA (Chief Fire Officers Association) reported from the Environmental Association; 2. http://fortune.com/2016/12/20/... ; 3. Autobody News, http://www.autonews.com/articl... 4. http://www.chemengonline.com/d...
Operational Guidance for Lowering Your Risk of Fire - Developed in conjunction with Brent Shows, Director of Recycling For Advanced Disposal.
• Keep the trash moving! • Stay in compliance with regulatory authority • Do not park equipment near a potential heat source • Implement pre-placement plan with local fire department • If available, verify and maintain existing automated suppression system • If facility is not protected source an additional layer of protection • Schedule fire watch with local security company if necessary • Develop action plan to follow should an event occur to limit confusion and facilitate information flow • Housekeeping
—Courtesy of Brent Shows, Advanced Disposal
Company info
6960 Orchard Lake Road, Suite 303
West Bloomfield, MI
US, 48322
Website:
firerover.com
Phone number:
844-417-6837