The Value of image-based Sensors
Generators, haulers and municipalities can all benefit from implementation of container sensor technology
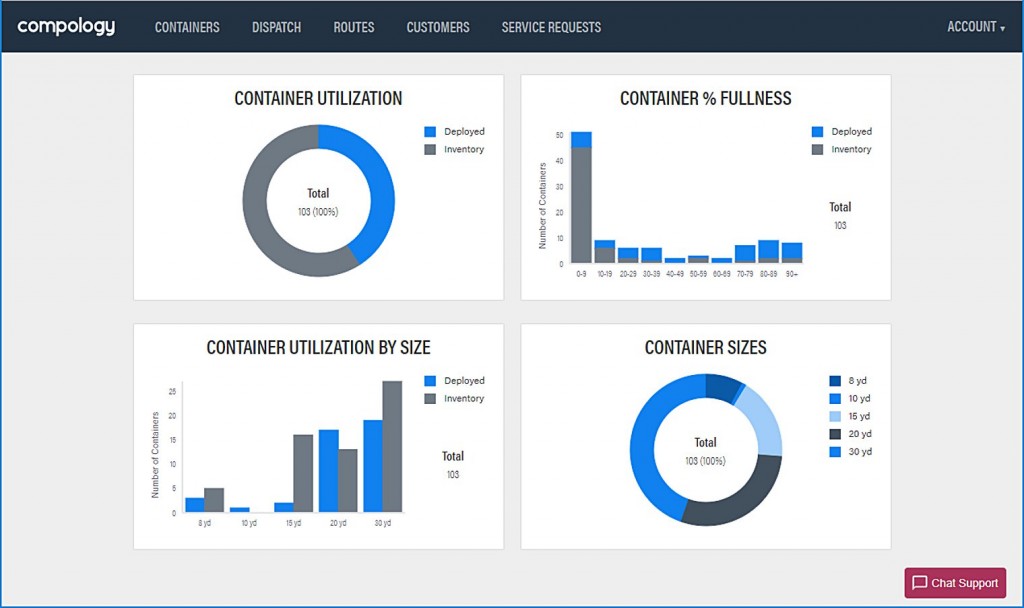
There's a shift happening in the way we, as individuals and collectively, think about minimizing our impact on our environment. Financial, political and environmental pressures are putting an increasing emphasis on consumers, businesses and governments to be more efficient, produce less waste and handle the waste we do generate more effectively. We see this across all industries, through increasing commitments to sustainable practices, and across all levels of government, through increasing numbers of environmentally-focused programs and mandates.
As a result, businesses and governments have rightfully turned to technology to aid sustainability and efficiency efforts. When it comes to the waste and recycling industry, we've already seen the implementation of robotics to sort recyclable materials, GPS to track truck performance, hand-held tablets for digital data entry and more. Where the industry has lacked technology, until now, is around collection of real-time information on the fullness, location and contents of waste containers. This lack of container information has limited the ability of waste haulers, waste generators and municipalities to operate more efficiently and take on the complex challenges of recycling and diversion efforts. Without a way to gather more information on generator habits and how haulers currently operate, gaining transparency and making impactful decisions for the future remains difficult; fortunately, help has arrived in the form of image-based container sensors.
Collecting The Right Data
For waste and recycling collection, the right data has to do with not only with type, but also quality and frequency. To have the ability to gain actionable insights, knowing what's happening inside of a dumpster 365 days a year is vital. However, until recently, haulers, city auditors or businesses have had no choice but to physically spot check dumpster locations just a few times per year and manually record their findings. This inefficient and costly strategy results in limited, outdated information that does little to help inform haulers, generators and municipalities on how to provide the right levels of service, improve behavior or set effective policy. Haulers, generators and municipalities have been ready and waiting for affordable, efficient and reliable solutions, and that comes in the form of image-based container sensors.
Compology's image-based sensors capture accurate and up-to-date container data such as the location, fullness and contents of a container, along with who is using it and when they were last serviced.
The Value of Image-based Sensors
Compology's sensor images provide a first-hand look at the contents of any container. With abundant sensor-generated data, waste haulers gain valuable insight into their own operational performance and visibility into generator behavior. This information allows haulers to efficiently deliver the right level and type of services, waste generators/businesses to gain transparency into their own disposal habits to inform more effective recycling and diversion practices and meet corporate social responsibility goals, and municipalities to have oversight and transparency into hauler and generator practices to better inform environmentally-focused mandates and improve outreach and education efforts.
Here are just a few examples of the positive impact image-based sensors can have:
Generators can see which business locations are performing well or poorly with recycling using images to site contamination and fullness levels to see a rise in recycling vs. waste levels. In turn, they can use that insight to target educational outreach, improve practices and measure progress around sustainability goals.
Haulers can now modify "just in case" service schedules to provide service "as needed", while also removing the burden for customers to monitor and call in for service by using fullness measurements to anticipate service needs. Right-sizing service, such as servicing containers when they are full as compared to servicing them on a fixed schedule, reduces the cost of collection by 30% or more. And when it comes to recyclables, images will help identify any contamination prior to pick-up, simplifying the efforts to product clean, marketable commodities.
Municipalities gain transparency into both hauler and generator behavior and the ability to identify specific issues or actions that potentially hinder meeting zero waste and diversion goals. In turn, they can use oversight to guide data-driven mandates and to develop tactics to address identified roadblocks.
Ultimately, Compology's image-based monitoring solution can not only help improve diversion and recycling practices, but also take the waste and recycling industry to the next level by eliminating inefficiencies by allowing for a shift to an updated service structure based on accurate, real-time container and content information, previously not available. Send us a note to learn more about Compology's image-based sensors and how to be more efficient, produce less waste or handle the waste you do generate more effectively.
(This post was originally written as a guest blog for ISWA President, Antonis Mavropoulos's Wasteless Future Blog.) www.wastelessfuture.com.
Case Study: Peninsula Sanitary Service Inc. (PSSI) Implements Container Monitoring Sensors
Peninsula Sanitary Service Inc. (PSSI), provides waste collection, processing and hauling services to world-renowned Stanford University. In addition to collection of day-to-day waste generated by a large campus population, PSSI also services roll-off debris boxes for a high number of construction projects taking place throughout the massive 8,000+ acre campus. The primary challenges for PSSI included: anticipating service needs and managing container inventory.
Andrew Pellegrini, Operations Manager for PSSI, knew there had to be technology that could help PSSI work smarter to accomplish their tasks, maximize container utilization and streamline their operations.
In the summer of 2016, Pellegrini turned to Compology's container monitoring solution: a web-based software powered by rugged, container-mounted sensors that use automatic GPS location tracking, image-based fullness monitoring and motion-based service verification. With the combination of location and fullness data along with access to container images, PSSI hoped to address their main challenges of managing container inventory and anticipating service needs. Compology technicians quickly installed sensors on all 104 PSSI roll-off containers and worked with PSSI so they could hit the ground running.
With the use of Compology's container monitoring solution, PSSI was able to:
Anticipate service needs: Compology's sensors provided accurate fullness level and images allowed for error-proof, remote visual verification. By having accurate fullness levels for all containers and being able to anticipate service needs, PSSI was able to service each site quickly by scheduling a drivers day based on each container's service needs.
Manage container inventory: For each container, the software shows fullness of the container, up-to-date images of the container, the container's precise location and customer information, and the date/time of last service.
For example, PSSI would often have to switch styles or sizes of roll-off containers for the various construction sites. PSSI would have previously had to check a whiteboard to see how many, what size and what type container were at the site and walk the yard to see what containers they had available. But Compology's software resolved that time consuming and inefficient process by clearly showing what containers were on site and what was available in inventory, allowing PSSI to quickly organize a swap.
"Instead of having to go up and count inventory, I was able to go on the Compology software and know instantly I can have 30 boxes available," said Andrew Pellegrini, Operations Manager, PSSI. Additionally, PSSI realized the benefits for their drivers from pinpoint accuracy for container locations to reduce search time on routes to simplified data entry to simplify workflows and improve driver safety. "Using Compology's tablets, I can dispatch our drivers to exact container locations, and they can easily enter work order information without getting distracted. My drivers are happier, and I get accurate data I can actually use," added Pellegrini.
According to PSSI, their successful implementation of Compology's monitoring solution has led to conversations with its sister companies to begin working with Compology.
Company info
1045 Bryant Street Suite 101
San Francisco, CA
US, 94103
Website:
compology.com
Phone number:
.