OPTIMIZING A SUPERIOR SLUDGE SYSTEM SOLUTION
OR-TEC’S 2.2 METER WIDE GEMINI BELT PRESS DELIVERS LARGE DRY SOLIDS THROUGHPUT AND AN EXCELLENT/DRIER FINAL CAKE RESULT FOR HISTORIC CITY OF NITRO, WEST VIRGINIA.
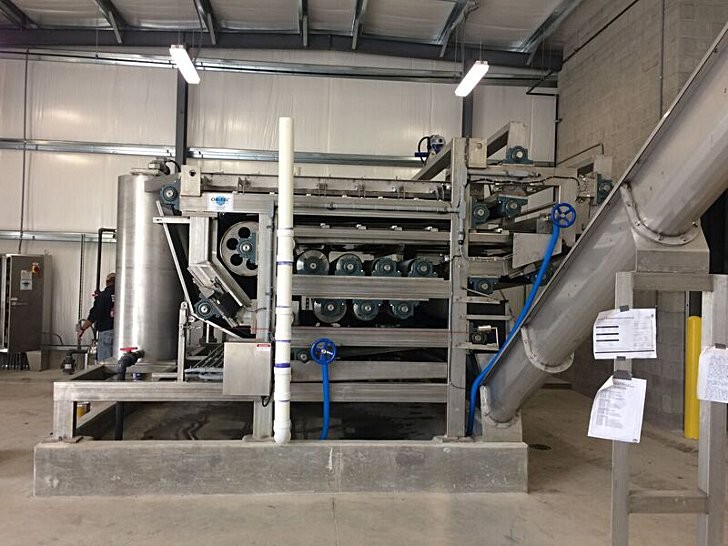
Given today's demanding wastewater treatment regulatory landscape, proper handling of sludge is a very important component of the design and operation of any size of wastewater treatment plant (W.W.T.P.) municipality. The ultimate mission of any such plant is to separate solids from water, and to disinfect both to different degrees by removing organic and inorganic contaminants−which may be hazardous or toxic to humans or have detrimental effects on the environment.
Solid waste, commonly called sludge, is typically comprised of approximately 1.5% solids and 98.5% liquid by the time the biological processing is complete. Removing harmful waste and rendering it safe for reuse or final disposal in landfills or farm field applications is paramount. Therefore, a key element in the wastewater treatment process is the Belt Press, which is used to dewater the sludge and change it from a liquid to a solid. For these reasons, the proper handling of sludge is a very important component of the design and operation of any W.W.T.P.−regardless of municipality or industrial scope.
In a progressive effort to adhere to West Virginia's recently stringent uniform water treatment regulations regarding land application of treated bio solids, West Virginia's City of Nitro Waste Treatment Plant (NWTP) sought out a superior solution to their existing Belt Press. The antiquated system was not performing at optimal levels, didn't have the capacity to handle their sludge loading, and required excessive system maintenance.
Located between two of the Mountain State's largest cities of Huntington and Charleston, Nitro was originally born as a "Boom Town" during America's mobilization for World War I for production of gun powder. Now celebrating a centennial in 2017, NWTP is nestled near a coal burning power plant and services approximately 4,500 customers within the regions' 7,178 population.
OR-TEC / NITRO SOLUTION:
Having researched Belt Press system options via visiting a number of different installations for nearly three years, Danny Lewis, NWTP's Plant Superintendent, discovered a unique Belt Press system in operation at a wastewater treatment plant in Williamstown, WV. The plant's superintendent, Bob Stirling, noted that it was a Gemini Belt Press from OR-TEC, Inc. (Maple Heights, OH), a leading integrated manufacturer of advanced wastewater treatment equipment for the municipal and industrial marketplace.
With previous experience utilizing OR-TEC's Screw Screens successfully for a number of years at the inlet of their plant to remove non organic debris (plastics, rags, sticks, and anything else you can imagine), Lewis invited OR-TEC to bid on their new system. Matching the specifications from the Williamstown plant operation, OR-TEC provided Lewis with detailed engineered specification proposal that ultimately won them the project.
OR-TEC / GEMINI BELT PRESS SYSTEM SPECS:
At 2.2 meters wide, the Gemini Series Belt Press is the largest made by OR-TEC and is ideal for the medium to large size W.W.T.P. The double belt system is constructed of stainless steel vs. haptic galvanized steel due to it being a far better material in wet/corrosive environments. This press combines a gravity drainage zone, a squeezing zone, and high pressure shear zone to provide a large dry solids throughput of up to 1,500 lbs. per hour, low polymer usage, high solids capture rate, and an excellent final cake.
The unit has a large flocculation tank with a variable speed mixer which allows the sludge and polymer solution to be thoroughly mixed. This flocculation process is critical to the dewatering process as it helps separate the water and the sludge-the sludge then forms into small popcorn size balls in the water. The variable speed mixer allows operators to easily change the mixing energy which helps ensure the best possible flocculation.
Following the flocculation tank, the sludge enters a large gravity zone where plows and dewatering rollers begins the process of thickening the sludge. From here, the thickened sludge enters a low pressure zone which features a large perforated stainless steel roller followed by an increasing pressure wedge zone. The final dewatering zone is a high pressure area where multiple rollers of decreasing diameter continue to squeeze and dewater the sludge.
A single control panel is used for all this equipment, and the Belt Press system also features electric actuation− so no hydraulics or pneumatics are needed. These electrically actuated belt tracking and tensioning systems are controlled by the onboard programmable logic controllers (PLC's) in the Belt Press panel. Ultimately, this means there's no need to have a separate pneumatic or hydraulic system to operate and maintain tracking and tensioning of the belts.
Polymer dosing feed system: A proprietary OR-TEC component, a mixing tank ahead of the system was added with a flocculation tank that was used in synergy to mix the polymer and sludge prior to sludge thickening or dewatering.
Wash water pump: High pressure pump used to feed the systems spray bars and polymer dosing system.
Screw auger system: Used to transport the dewatered sludge when it is discharged from the belt press to the dump truck.
Lime feed system: Used for adding supplemental lime for the sludge prior to it being land applied. Added lime helps the sludge to meet West Virginia's 20% solids landfill requirement. Lime addition is also beneficial for farmland if sludge is being land applied.
Sludge cake monitoring system: A unique OR-TEC add-on feature which constantly monitors and detects the sludge being discharged from the Belt Press. If no sludge is detected for one minute, this entire system shuts down and an alarm is activated.
OR-TEC / ONE-SOURCE OPTIMIZATION:
An integrated Belt Press system as complex as Nitro's typically involves a number of third party suppliers to realize its optimal performance goals. Not only is this time intensive, it makes installation more complicated. W.C. Weil Company (Charleston, WV) Sales Manager, Danny Lusk, who collaborated with both entities on the project from its inception, noted, "OR-TEC's ability to serve as a one supplier source means the equipment functions as a cohesive system−with one company and one phone number for questions or troubleshooting moving forward.
Ultimately, OR-TEC advised and supplied all aspects of Nitro's system, adding value via working out all of the kinks at every stage of implementation. Some of these variables included trouble-shooting wiring of the control panel on the wall, upgrading to the recommended stainless steel (vs. haptic galvanized) at no additional cost, and even providing conveyers that would typically need to be sourced out. These value-added benefits are particularly important for a smaller plant as no installation or maintenance crews are required.
According to Jim O'Leary, OR-TEC's Sales & Marketing Manager, "Every application requires specialization for their municipal market, and developing products that work in those applications requires close collaboration with customers. It's part of our core definition to work closely with users−we have the technical people on staff to optimize that process every step of the way."
OR-TEC / NITRO CONCLUSION-RESULTS:
Delivered in September 2016, Nitro's new Belt Press system has now been in operation for months and running at advanced capacity and performance. According to NWTP's Danny Lewis, "The system handles a lot of throughput, so there is substantially less for operators to deal with on a daily basis. There's no oil, filters, or air supply needed so it's more user friendly, easier to operate, and maintain. If there is any maintenance or service issue, OR-TEC comes in to work out the bugs immediately."
Notably, NWTP's engineering specification originally called for a minimum of 16% final dry cake−the percent solids in the sludge following dewatering. OR-TEC's Gemini Belt Press system is exceeding the required production rate requirements, as NWTP is currently achieving a 20% plus final dry cake standard.
With the system now operating at full-potential, Nitro continues to advance its operation this summer by adding two OR-TEC Screw Screen Compactors (OSC7C). Positioned at the inlet of the plant, the screens compact, wash, and lift debris to a convenient height for ease of disposal. These units are provided with perforation size of 6mm for municipal wastewater. The system is stainless steel (AISI 304 or AISI 316) and can be mounted at an angle in a channel, in a tank, or supplied for vertical installation.
Regardless of the end-use capacity requirement profile, OR-TEC focuses on detailed customization to optimize wastewater treatment needs every step of the way−providing a one-stop service source for the entire life of the system. All OR-TEC's products are competitively priced and comprehensively backed by a customer service support system that is unparalleled in the industry. All OR-TEC Belt Press and associated wastewater products are designed, engineered, manufactured, and assembled in the USA.
For more detailed information contact: www.or-tec.com