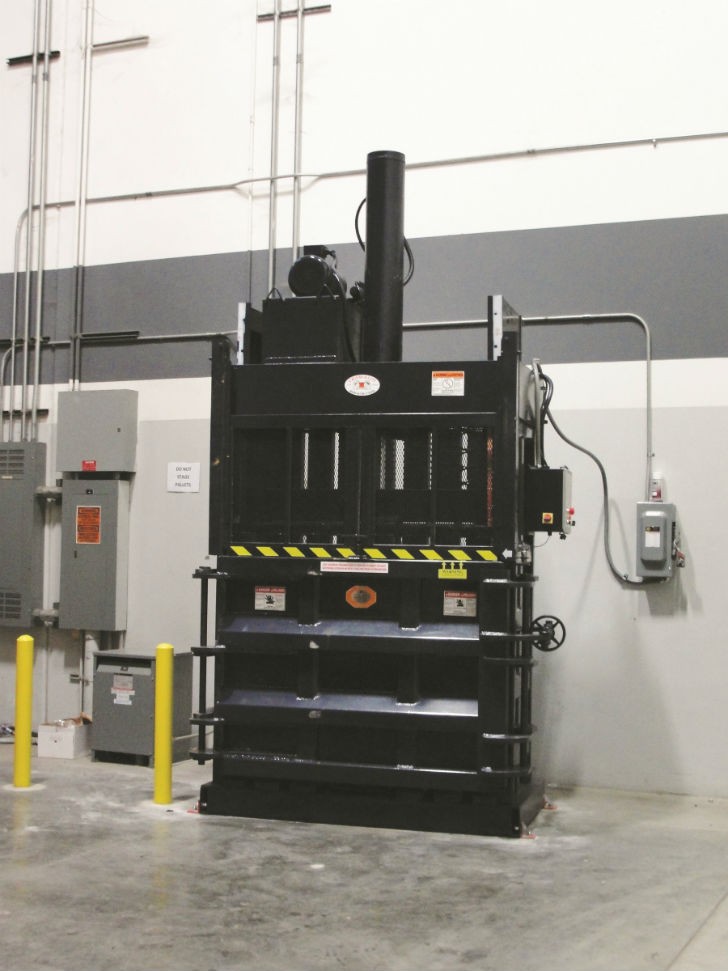
Recyclables handling and the implementation of a solid waste management program along with good in-house procedures can keep costs in check and greatly reduce expenses. The key is to identify areas of concern and begin working with a qualified waste services consultant/equipment supplier to establish an understanding and develop an unbiased plan. When it comes to baling, the first step is selecting the most suitable type of machine for your operation.
Baler Selection
The two different configurations of baler – vertical and horizontal – each have their pros and cons, but they both accomplish the same goal. When it comes to selecting the right baler, there are three key factors that must be considered:
1. The type of materials that are baled – cardboard, aluminum, plastic, plastic film, or other materials?
2. Volume – how many kilograms, pounds (or tons) of materials are being baled per day?
3. Space – balers come in different sizes and businesses have varying amounts of floor space.
When would a horizontal baler be recommended? A good rule of thumb to follow is if your business or recycling operation is baling more than three tons of recyclable waste per day, then a horizontal baler would be recommended. However, horizontal balers take up more space than a vertical so this is not always the best option. Vertical balers remain the most commonly used balers – for retail businesses especially – because not only are they efficient, they are space-efficient. Vertical balers are ideal for installation at grocery and retail stores, and at small manufacturing companies and distribution centres, as well as recycling facilities.
Baler Maintenance
Once the right baler has been selected, it functions as an efficient machine as long as the right maintenance and upkeep procedures are followed. The maintenance procedures depend on the type of baler in question. Following are three key points to consider for vertical and horizontal balers respectively.
Vertical balers
- Grease and lube bearings once or twice weekly.
- Grease hinges and chains once or twice weekly.
- Change oil yearly.
Horizontal balers
- Grease bearings once or twice weekly.
- Grease hinges and chains once or twice weekly.
- Re-lining the baler floors – this can be an expensive proposition, but considering the volume of material horizontal balers are capable of processing, it can result in tremendous savings. Re-lining depends on volume and materials being baled (aluminum cans are relatively abrasive) as well as how often a baler is used.
Making the right choice: Amko Recycling
Colorado-based Amko Recycling has been utilizing EPAX balers for several years, following their first purchase of a DX60-8 downstroke vertical baler.
“Prior to 2010 we had worked with many industrial baler companies and gained very little help from them in terms of service,” said Melissa Akins, Amko Recycling. “In April 2010 I set up a new account that required a reliable compactor along with service.”
Akins decided on the Epax DX60-8 downstroke vertical baler and has since set up many compactors and balers at customer sites. “Amko is very lucky to be partnered with Epax to cater our customers’ needs in recycling,” added Akins, who says they rented another DX60-8 downstroke vertical baler in 2013. “The efficiency of baling aluminum cans has improved ever since we started using the DX60-8. Indirect cost has been reduced due to the fact that there is no need to move loose cans around to get to a conveyor. Our loose aluminum cans are converted into a compact bale, ready to be processed, all in one area.”
This article, courtesy of EPAX Systems, first appeared in the September, 2016 edition of Recycling Product News, Volume 24, Number 6.