The risks of not staying on top of shredder maintenance
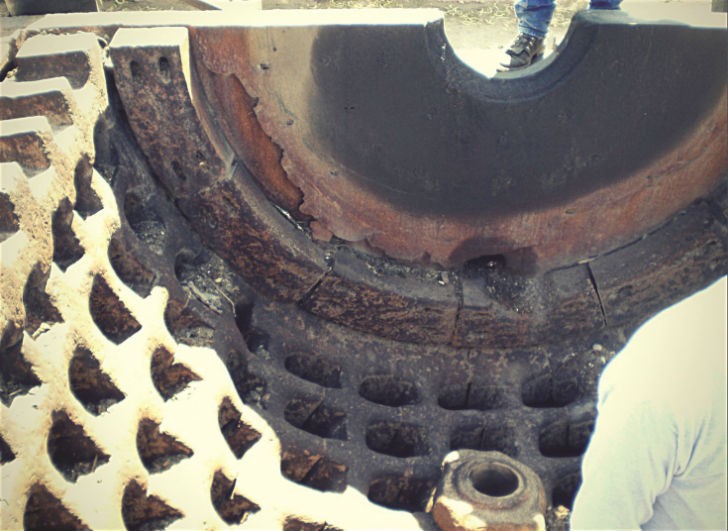
Late 2015 continues as a tough time to be in the shredding business. Scrap prices continue to find new lows while the input side of the business tries to adjust to the change in value. It may be the sign of a fundamental reset in the value of scrap. How the volume adjusts to the new price is not yet clear, and obsolete scrap volumes may lag for some time until the economics of disposal and transport adjust.
Scrap economics today dictate the need to cut operating costs, and one of the first things to target is maintenance.
The question is; if you are running a scrap shredder on a limited schedule, can you safely defer routine maintenance?
What do we mean by routine? Routine refers to the habitual tasks that are part of best practice. They are the small things operators know are important, but are tempted to defer because of limited run time or available maintenance hours. And they are normal maintenance expenditures that might be put off until better markets return. Skipping what we know works is not adapting to new markets, but a mentality that will cause more costly problems down the road.
Making the maintenance adjustment
Take stock of current production requirements and adjust based upon facts, not guesses. The plain truth of the matter is a shredder has to be opened and inspected after every production shift.
Inspecting the box is a matter of routine, not tons. Who has not had a problem in the first part of a production shift? There may be a piece of scrap jammed in such a way it will pop off end caps or bind the rotor during start up. Inspecting after each production shift helps you plan for regular maintenance and reduces the chances of surprises. When you see it, you inherently know what needs to be done.
On a shredder, everything needs to be checked, despite reduced personnel and run hours.
The list above isn’t news, it’s items operators know, but are tempted to defer. Many things should be checked on each shift, and will influence how well a shredder performs and keeps production costs in line with expectations.
Maintenance, production and uptime are part of the same equation. Allowable downtime, and changing the “who” and “when” part of maintaining a shredder can help lower costs. Balancing expectations, uptime and production with the maintenance plan helps bring expenses that can be trimmed and deferred into focus.
Vital spares and replacements are popular deferred expenses, but replacement parts cannot be deferred too far into the future. If you shred, often you will need parts sooner than you think. Rotors, motors and bearings can fail at the least opportune moment. A six month wait for a rotor could substantially change your business. Check lead times with key suppliers and then revise your stock plan for vital spares and replacements.
To trim maintenance costs, you must continue to be pro-active, not reactive. You can defer things, but in an intelligent way. Ordering ahead of time and using your labour hours in a pre-determined way helps keep overtime and costs level. You can't anticipate everything, but preparedness counts.
Following are a few “DOs” and “DON’Ts”– some important tips for most effectively maintaining your shredder.
In the business of shredding scrap, not everything works out as expected. Despite economizing on maintenance and repair, you know where you can defer and where you can’t. Go with the things you know work best in your production process. It will save you headaches and money in the long run.
Ben Guerrero has over 40 years of scrap industry experience and is vice president, K2 Castings.