Enviro-Smart Composting Facility First Of Its Kind in B.C.
Green Mountain Technologies’ high-pressure reversing aeration and control technology is taking composter’s production to the next level
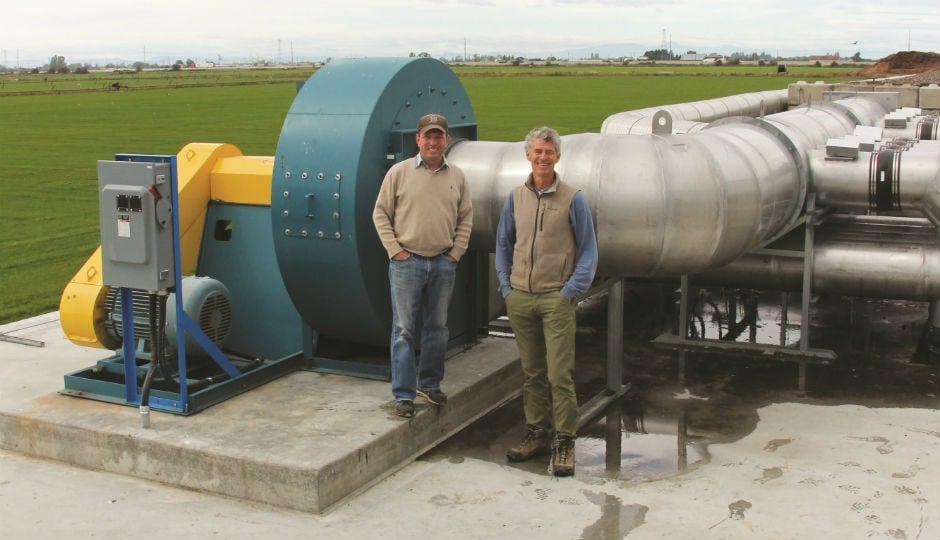
Daryl Goodwin is an ex-pilot, so by nature he is someone who likes to make sure things are done right. As the founder and president of Enviro-Smart Organics Ltd., located in Delta, B.C. (south of Vancouver), he built his original building for composting in 2007 to handle mostly food industry waste, and as an addition to his Westcoast Instant Lawns turf growing business. This is still a central part of his overall operations today, and benefits directly from the high-quality compost created at the facility. Up until recently, Enviro-Smart’s compost aeration system used low pressure positive air delivered by aeration trenches cast in concrete.
After years of growth (to approximately 90,000 tonnes of organic waste processed in 2014), Goodwin decided to upgrade his facility. He also wanted to “stay ahead of the curve” with respect to Metro Vancouver’s organics ban, which officially began this past January. According to Goodwin, the ban has resulted in a slight increase, so far, in the amount of food waste and other organic materials coming into their facility, from the City of Delta, as well as Vancouver and nearby Burnaby. Goodwin expects this to increase as the ban (including fines for violations of the rules) will take some time to fully take effect. Additionally, as part of Enviro-Smart Organics’ agreement with the City of Delta, residents of the community can drop off organic waste at no charge. Goodwin says it’s one way Enviro-Smart gives back, and it has also resulted in increased volumes of inflowing material.
In 2014, after installing their new 40,000 sqaurefoot steel-frame, open-end, fabric-covered building that would be dedicated to housing piles of curing compost (the second on the site, shown in the background, right) Enviro-Smart began the process of installing a fully automated high-pressure reversing aeration system.
Washington-based Green Mountain Technologies (GMT) was hired to supply the design for Enviro- Smart’s new aeration floor, and for the installation of a new blower and complete aeration system, including the software and controls that would be integrated into the company’s office network on site.
The new reversing aeration sparger floor, the first of its kind in the province of B.C. , uses a highpressure sparger nozzle system that eliminates the clogging Enviro-Smart experienced with their former trench system.
“We gave him the aeration floor and piping design prints,” explains Michael Bryan-Brown, president, Green Mountain Technologies. “Daryl hired contractors locally to build the floor, so in that respect, we did not provide the whole package on this installation. I think this was one of the advantages Daryl saw in working with us. We said ‘we’ll do the job piecemeal’, so we showed them the techniques for how to weld in the structure – essentially a long pipe running under the concrete, with spargers welded in.”
Once the aeration floor was built, GMT installed the complete aeration system, and operations began on the 15th of January this year. Since then, the system has processed over 65 thousand tonnes of organic compost.
“We are now getting lots of air through our piles, both positive and negative air,” continues Goodwin. “Our compost is much better and we’re producing it quicker.” [Positive air = pushing, negative air = pulling].
“We’ve cut curing time in our buildings by about half. We keep it inside for about seven to 10 days, and then it goes to outdoor curing and turning in our yard. In our original composting building, we used a trench system and indoor curing typically took us 20 to 24 days.”
Goodwin adds that his electrical bill has gone up since the new system was installed, but he knows this is what is required to deliver the very large amount of both positive and negative high-pressure air needed to achieve the kinds of efficiency and productivity increases they are now seeing. And he’s optimistic they will end up getting more efficient in the long run with respect to their use of electricity.
At the beginning of September, Bryan- Brown was on site again, this time to help with the renovation of Goodwin’s original “old” 25,000 square-foot compost building, consulting on the addition of a new aeration sparger floor, and installing the damper controllers for the new automated system, similar to that in the new building. The old building renovation is scheduled to be completed this fall.
“One of our biggest goals is that we want to be fully computerized and automated,” says Goodwin. “That’s why we are now also renovating our older building. It will only use positive air, but we’re converting it to work with our computer system and automated probes, and it will save us a lot of time and effort. As with our new building, in our renovated building we’ll be able to monitor our compost continuously and very quickly.
“We have also replaced 20 small fans with two large, 60-hp fans, while the new building uses two 100-hp fans. All our new larger fans can run continuously, which eliminates all the stop/starts we had with the old system.”
Controlling odour and water
“In this business, it’s all about odour,” Goodwin says. “We’ve only had about five complaints in five years.
“Still, we do not want to create a hassle for our neighbours. We have to be very cautious of which way the winds are blowing, and with what we’re doing. Our new reversing aeration system helps with odours definitely.”
According to Bryan-Brown, the GMT reversing aeration system allows Daryl to suck air from his new building into a biofilter, which is 95 percent efficient in removing odours. If needed, the entire system can be switched to negative pressure only, providing 100 percent odour control.
“You’ll always get some odour from just even the operation of screening and moving product around, in and out of the buildings,” says Goodwin. “As long as we are aerating well, we are confident we can control odours.”
Water distribution is also a critical point when the goal is to process material quickly, to high quality and without environmental issues. For water management, Enviro-Smart’s site includes a large leachate pond, currently also undergoing some upgrades, where they collect all of the site’s leachate, aerate it and reuse it on site.
“Nothing goes into the environment here,” says Goodwin. “Our whole site is paved and we have drains everywhere, all throughout our whole operation. We also just set up a new system so that we can use city water in the winter, and we’re currently meeting with the City of Delta. We want to be able to suck out ditch water using an electric pump so we can irrigate inside both buildings.”
The Green Mountain Technology system
“What Daryl has here is a turned aerated pile system, using an automated reversing sparger floor aeration system. It is not static,” explains Bryan-Brown. “We designed all the software and programming to automate it, and use an industrial controller, similar to those used on cruise ships.
“The aeration floor is not a pipe-ongrade system where pipe is installed on top of the concrete slab. Enviro-Smart’s floor is designed so all the aeration is below-grade, with all the piping systems and manifold under the concrete. This enables wheel loaders and other equipment to drive right over the floor without having to make any adjustments to the system.
Enviro-Smart’s previous floor system used grates with multiple holes, causing problems, especially with plugging of holes which were difficult to clean. And the operation’s large, heavy wheel loaders were actually crushing the grates.
“With this floor system, it is protected by concrete and is essentially self-cleaning,” continues Bryan-Brown. “It forces all of the airflow into the spargers (cylindrical nozzles welded onto the aeration pipes running below the floor) to either push or pull air through the compost piles at high pressure. So if one gets plugged, this system just blows it out.”
Enviro-Smart’s floor design has spargers on a grid system, about 1/4-inch below the concrete, connected to the aeration pipe system and to drilled holes from the surface of the concrete, between 1/2-inch and one-inch in size. This creates very high pressure air flow to the floor.
“We designed the sparger system to direct air upward, essentially creating a jet of high velocity air (about 90 to 100 mph),” says Bryan-Brown. “It blows any plugs out and anything on top of the holes gets ejected.
“With our blower system, we use a pressure sensor inside the ducts. It maintains constant pressure for the whole system. When dampers are opened and closed, that changes the pressure, and it slows down or speeds up the blower. By delivering that constant pressure, we get consistent, predictable performance out of the whole system.
“Our blowers are running continuously. The damper position is controlled by a temperature probe. When a particular zone of compost, controlled by two dampers, heats up, those dampers start to open. It’s all based on continuous, temperature feedback, which is all recorded. This is something Daryl did not have previously.”
Bryan-Brown adds that with continuously recorded temperature data, Daryl doesn’t have to have a guy out every day with a manual temperature probe, writing down data on a clipboard. Additionally, operators can come in and change parameters system-wide automatically.
“I don’t believe there are any other computer-controlled reversing sparger systems in Canada currently,” says Bryan-Brown. “We have installed three similar systems in Washington State, but this is the first of its kind in B.C.”
An electric-powered future
According to Goodwin, another recent development for Enviro-Smart Organics and a further reflection of the growth the company is enjoying over the last few years, is that they are moving to electric power for the screening side of their operation.
“Coming in October, we’ll have a new West Salem Machinery electric-powered Titan screener capable of processing 450 yards per hour, to replace the 150-yardper- hour McCloskey screener we have used for many years,” says Goodwin.
He says, in his experience, it’s not so much their actual grinders, screens, turners, loaders and excavators that require a lot of maintenance – it’s the engines.
“Our new electronically-powered West Salem screener will eliminate the hassle of looking after an engine. It will be more efficient for us, has less moving parts and no diesel. And the best thing is – we’ll be able to turn our volume way up. We’ll be able to run our new Titan grinder four days per week, and one day off, and we’ll screen to 1/2 inch.
“After that, I’m going to look at a conveyor system,” Goodwin says, “for moving product like a gravel pit.” RPN