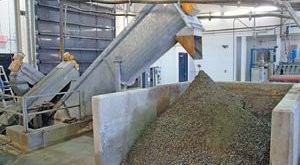
Dynamic Concrete, out of Calgary, is recognized as western Canada’s largest concrete pumping and finishing company. The organization is also at the forefront of the green movement in their industry.
Dynamic Concrete started out in the early 1980’s as a small Vancouver branch of a “one-stop-shop” ready mix company that provided multiple services. The ready mix portion sold off, and Dynamic Concrete opened its first Calgary operation in 1998, which eventually became their head office. They commission 23 concrete pumps and employ over 150 people in seven divisions, with focus on concrete pumping, finishing, formwork, cutting, grinding and polishing. A separate speciality division provides concrete equipment parts and repair service, along with vehicle safety certified inspections.
In the summer of 2009, Dynamic moved into a state-of-the-art 45,000 square-foot facility, which included the latest in concrete pump washout systems.
Pumping concrete in minus 25-degree temperatures is common, and traditionally concrete pumpers dump concrete waste at the job site or on a vacant lot without incident. Dynamic Concrete is a little different from your average concrete company however, and since their move last summer, they have made a huge statement in the concrete pumping industry by constructing the first indoor concrete washout and recycling facility. And not only is it the first facility of its kind, they opened it up to any pumping company wishing to reduce their environmental impact and improve stewardship.
The right equipment
Challenged with the physics of ground-level pump discharge, Dynamic investigated the success of a Pump Discharge Conveyor (PDC) at a nearby cement company. The maintenance operator there recommended BIBKO.
The operation managers at Dynamic were diligent in their research. It began with site visits and facility tours by representatives of BIBKO Recycling Systems USA. The company specializes in the field of leftover concrete recycling systems for both the Ready Mixed and Precast industry.
The visiting technical engineer provided a customized solution that not only provided a dual ground level pump washout system, but a mechanical process to reclaim aggregate and cementitious water for reuse in the production process. This resulted in an environmentally friendly “zero waste” operation specifically designed to overcome the problems of leftover concrete and washwater disposal. BIBKO’s complete system was designed to handle pickups, pump trucks, and other washouts. Central to the system is a BIBKO Model 1000 Reclaimer that was implemented to remove heavy sand and gravel, and produce clean, recyclable material.
The other machine on site that is proving key to Dynamic’s success in their concrete washout and recycling efforts is an ALAR Auto-Vac water-recycling filter. This machine provides the ability to handle slurry water without any discharge back into the environment.
Build-up of cement fines can become a burden, by causing excessive fresh water makeup and dirty water storage, along with exorbitant dredging and wet tonnage hauling costs.
The Auto-Vac is engineered to enhance concrete reclaiming efforts when the after-effect of reclaimer gray water (cement fines) becomes just as difficult to manage as the returned concrete itself. The machine filters out cement fines and colour, yielding clear recyclable water and dry manageable solids. ALAR units are designed to handle a variety of wastewater applications generated by ready mix, precast, hydrodemolition, sawing, drilling, and other concrete producers dealing with high return rates, colour, and high strength concrete wash-up issues.
Running a zero-discharge operation
With the new technology being used and their new facility, Dynamic has effectively created a zero-discharge operation. Concrete pump trucks enter one of two 120-foot bays and easily dump into twin PDC hoppers located below the floor, which feeds into the reclaimer. After the BIBKO machine reclaims the heavy aggregate, the wastewater containing cement fines is pumped into an agitated holding tank for filtering through the ALAR water recycling system.
Because the Auto-Vac is a self-cleaning dewatering system, active concrete will not blind or plug the filter. The system separates water from cement fines, generating clear/colourless (non-potable) water for recycling and re-use in the batch reclaimer and washout, and it produces dry, manageable solids for easy transport offsite. (The dewatered fines measure approximately 65 percent dry solid content by weight, and have the consistency of damp sand.)
At Dynamic Concrete, filtered water from the ALAR machine is reused in daily operations. Surplus water is held in a 10,000-gallon concrete container to fill the pumper’s water tank for future truck washing.
“The combination BIBKO/ ALAR system has been in operation for over six months,” states Joe Delehay, Dynamic Concrete Company president. “To say the least, it has been impressive, and is out-performing our expectations. Not only are we reducing the amount of waste going into the environment, but our truck fleet operations are more efficient.”
Delehay went on to explain that in the “old days” trucks would drive around after a pour was complete (in rush hour traffic) looking for a ready mix producer yard where they could dump the waste concrete. It became apparent that this dumping practice was becoming costly for the ready mix companies, and Dynamic sensed that it was not a matter of “if” but “when” producers would turn the pumpers away from their yards. Facing the prospect of being cut off from ready mix disposal, and with talk of future government dumping regulations, Joe and his company took a proactive approach.
“This system has produced the results intended and is making Dynamic Concrete more environmentally friendly to its neighbours each and every day,” Delehay concluded.
Now, with their indoor concrete washout and recycling facility in place, truck drivers can return each night, dump the waste, then wash and park their units inside a heated building.
The proactive approach of pairing a BIBKO Reclaimer and ALAR Water Recycling Filter instead of using traditional dumping practices, along with providing sustainable solutions to concrete construction pumping projects along Calgary’s eco-sensitive rivers and streams, is proof that Dynamic Concrete is not your average concrete company. It also demonstrates that a commitment to hard work, ingenuity, and stewardship can give forward thinking companies like Dynamic Concrete not only an environmental, but also an economic edge.