Veolia e-waste division sees improvement in CSA Score with electronic fleet management system
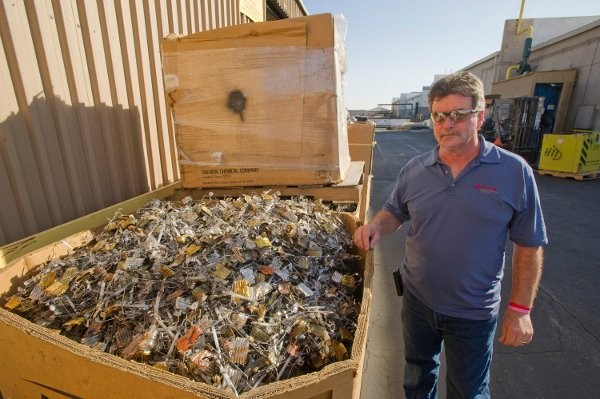
For Veolia Environmental Services’ operating groups, reducing waste is not only a key part of the company’s mission, but also a key objective in the company’s fleet operations. To help it fulfill that objective, in 2010 the Electronics Recycling Division (ERD) of Veolia ES Technical Solutions, LLC adopted Zonar’s electronic fleet management system. The system includes an electronic vehicle inspection reporting (EVIR) solution for pre- and post-trip inspections and an onboard telematics platform. The telematics system captures data including fuel consumption, rate of travel, idle time and fault codes. The ERD monitors this data to manage driver performance and streamline the maintenance process.
As a result of using Zonar to identify and then repair mechanical problems early, Veolia’s ERD realized $41,000 in year-over-year savings, according to Michael Bomgardner, fleet manager for the division. He says roadside service calls were reduced by 22 percent, resulting in a savings of $13,000 when compared to a 12-month period prior to Zonar’s installation.
The ERD also experienced a 13 percent reduction in the amount of time its vehicles spent in the maintenance shop, realizing annual savings of about $28,000 as a result of improved shop efficiencies. (Bomgardner’s estimate of savings does not include Veolia driver downtime costs which are based on $85 per hour.)
“Veolia charges customers when drivers are detained. It’s a fixed cost based in large part on how much the company pays drivers per mile,” Bomgardner explained. (This estimate doesn’t include the cost of roadside assistance or equipment that must be repaired or replaced to return the truck to service.) Ultimately, he says “reducing driver and vehicle downtime results in better on-time service to customers. This provides great value, but is also difficult to quantify in terms of savings.”
But more important to Veolia than the savings are the significant improvements in the division’s and company’s scores under the U.S. Federal Motor Carrier Safety Administration’s Compliance, Safety, Accountability (CSA) Program.
“Since adopting the Zonar system, the division’s percentile scores in nearly all of CSA’s seven categories were reduced by more than a third, which also contributed to the reduction of overall company scores,” Bomgardner said. “Under CSA, the lower the percentile score, the better.”
Compliance, safety and accountability
Veolia ES Technical Solutions is a division of Veolia Environment Services North America, which includes Veolia ES Industrial Services, LLC. The Technical Solutions group offers a complete range of hazardous and non-hazardous waste services through its nationwide network of service, treatment and transportation facilities. The group operates incineration, solvent recycling and electronics recycling services, and provides on-site services from a national footprint of locations.
Veolia’s customers include pharmaceutical companies, chemical manufacturers, refineries, hospitals, universities and research laboratories. The ERD division collects used lighting and electronic waste and transports it to processing facilities for recycling or disposal.
The Phoenix-based ERD division of Veolia ES Technical Solutions operates a mixed fleet of 33 tractors, with dry van, flatbed and tanker trailers, maintained through a nationwide leasing program administered by Penske. With equipment running in all of the “Lower 48 states”, ERD drivers or dispatchers call a toll-free number to schedule maintenance or arrange for assistance for emergency roadside service calls.
“By using Zonar and catching the problem before our truck leaves, and fixing it, we’re avoiding having to pay a tremendous markup for whatever parts and pieces the roadside serviceman is going to sell us to fix our truck,” he added. Veolia also realizes savings through maintenance shop efficiencies because Penske can better respond to unscheduled maintenance issues.
“If the check engine light comes on while the truck is out on the road, I’m going to see it at the same time or soon after the driver sees it on his dashboard,” Bomgardner said. “Using Zonar, we can then determine whether it’s a problem that needs to be addressed right away or if the driver can continue to finish his run. I can then alert Penske that our truck is coming in and this is what the truck’s sensors are telling us.
“In these kinds of situations, we’re going to have downtime no matter what,” he added. “Zonar gives us a heads up so we can minimize the effect on our operations by getting our trucks and drivers in and out of the shop faster and back on the road sooner.”
Another significant positive aspect of Zonar, Bomgardner said, is being able to produce hard-to-refute records that show, among other things, how fast the company’s trucks are actually traveling when drivers are involved in accidents that are not their fault.
From August of 2011 to August of 2012, Bomgardner said there have been three accidents in which he’s been able to trace the path of the truck and clearly show what company drivers were doing. From a disciplinary standpoint, it cleared all three drivers from repercussions as far as the company was concerned.'
“The Zonar system protects our company and our drivers when they’re involved in accidents by giving us the ability to show what happened,” he said. “And that’s how we sold it to our drivers, who were initially concerned about this ‘Big Brother’s watching you’ aspect. I think our 31 drivers have really come to appreciate the need for this, particularly since we’re a hazardous materials hauler.”
Bomgardner said the company is better prepared should its safety records ever get audited by state or federal inspectors. Currently under CSA, all accidents count against the carrier and the driver, regardless of who’s at fault.
Bomgardner said he’s been a big proponent of CSA since it was introduced in late 2010 because it places equal responsibility for safety on the company and its drivers, and because it makes driver behaviours and pre- and post-trip inspections more critical to running a safer operation.
Bomgardner said he realizes that the system could be a double-edged sword if it ever shows company drivers speeding or driving erratically. But since the Zonar system alerts him to vehicle speeds, it allows him to monitor driver behaviours and quickly identify potential problems and address them before they lead to accidents. Zonar’s onboard computer and EVIR make it easier for him to monitor and counsel drivers on their driving behaviours and for drivers to conduct their pre- and post-trip inspections correctly and more efficiently.
“Because we’re doing better pre-trip and post-trip inspections on our equipment we’re catching more problems before they leave to go on the road and we’re identifying potential problems and fixing them before we go out,” Bomgardner added. “At the end of the day we’re providing a better service for our customer and operating safer equipment on our highways.”
The Zonar inspection system
To help Veolia accomplish better pre- and post-trip inspections, Zonar’s radio-frequency identification (RFID) tags are placed, just once, on the division’s vehicles in critical inspection “zones.” These weather-resistant tags contain information about their location on the vehicle, the components to be inspected and the identity of the vehicle or trailer. Using Zonar’s 2010 inspection tool, Veolia drivers conduct their inspections by placing the reader within inches of each tag and indicating the condition of the components within the zone with one-handed, push-button responses.
When a defect is discovered, the driver selects a description from a pre-defined list and indicates if the vehicle is safe to operate. When the inspection is complete, drivers place the Zonar 2010 into the vehicle mount. The information is then transmitted to a secure database that can be readily accessed from any web-browser via Zonar’s Ground Traffic Control web-based fleet management software, providing a real-time picture of fleet operations.
“We have to improve and maintain good CSA scores in order to maintain our safety rating,” Bomgardner said. “If we lose our good safety rating, then we can’t haul certain hazardous materials for Fortune 500 companies, and that’s our bread and butter. We can’t afford to have a cowboy out there driving a truck, getting us into trouble and jeopardizing our livelihood.”
Mike Bartholomew, director of special programs for Veolia ES Technical Solutions, said customers are increasingly recognizing the importance of their carriers having a robust asset tracking and management program in place. As a result, the company has plans to expand the use of Zonar in more of its divisions.
“Recently, we put together a major proposal for new business and on the application one of the questions specifically asked, ‘do you have a GPS tracking system in place?’,” Bartholomew said. “With some of the high-hazard materials we haul, safety and security are critical issues. Our customers need to know where our trucks are and having the ability to track them using Zonar is a very important tool for our operation.”
Veolia ES Technical Solutions Zonar Systems