8 ways AIM Recycling is combatting labour shortages in metal recycling
How modern solutions are helping attract and retain talent in the scrap metal sector
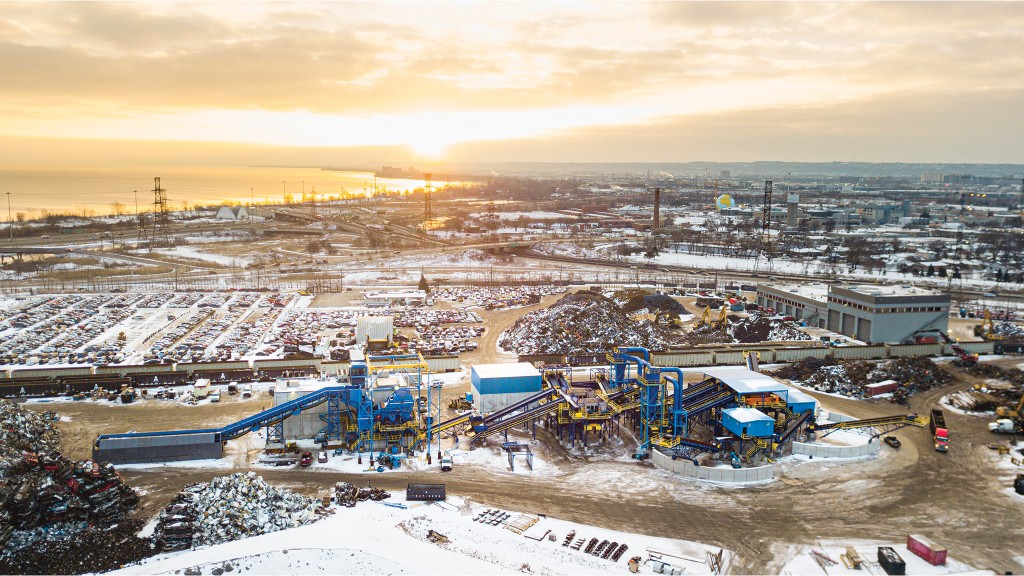
The scrap metal recycling industry has long faced a shortage of skilled labour, negatively affecting both operational efficiency and processing capacity at recycling facilities. To combat this issue, recyclers are turning to modern solutions - such as artificial intelligence and social media - to mitigate the adverse effects of a lack of available workers.
Taking the lead in these initiatives is AIM Recycling, a division of American Iron & Metal (AIM), a family-owned enterprise and a significant player in ferrous and non-ferrous metal recycling. Founded in 1936, AIM Recycling has grown to include over 4,000 employees at more than 135 sites worldwide, distinguishing itself by placing employee development at the core of its business strategy. To better understand how one of the largest metal recyclers is tackling this critical issue, I spoke with Director of Marketing Corey Cooper and Talent Acquisition Manager Ryan Melanson to get their perspective on the challenges and opportunities associated with labour shortages.
"The shortage has created growth opportunities for existing employees, with a focus on training and advancement programs," says Melanson. "As AIM Recycling continues to develop our current and future workforce, we're investing in advanced training to enhance the skills of our workforce, while diversifying recruiting strategies by targeting underrepresented groups like immigrants, refugees, or individuals with disabilities. We're continually researching automation and innovation to increase efficiency and productivity, as well as to improve working conditions and retain personnel."
According to Melanson, AIM Recycling attributes labour shortages in the metal recycling sector to factors such as a lack of public awareness about the role metal recycling plays both economically and environmentally, as well as an absence of formal training programs and apprenticeships tailored to the industry's specific needs. Moreover, Melanson notes that there's a critical lack of skilled trades workers with expertise in recycling, metal processing, and heavy machinery operation, all of which are essential skills in the industry. Economic downturns have also contributed to a reduction in construction and manufacturing, directly impacting demand for labour in the scrap metal sector.
Addressing these challenges will be crucial in ensuring the industry can meet the rising demand for recycled metals, an uptick that Cooper says is fuelled by infrastructure development, automotive manufacturing, and the widespread use of consumer electronics. To meet these needs, facilities must expand to handle the growing volume of materials.
"Expansion not only leads to efficiency improvements, but also enhances operational efficiency, reduces processing costs, and increases competitiveness," says Cooper. "It enables facilities to offer a broader range of recycling services, including electronic waste recycling, opening up new revenue streams and meeting changing customer demands."
As the company continues to grow, AIM Recycling is equipping employees with the necessary skills and opportunities for growth by investing in training, promoting from within, encouraging cross-functional skills, and fostering mentorship, all of which contribute to attracting and retaining employees in the long run. Here are eight strategies that AIM Recycling is leveraging to build its team and tackle the labour shortage in the metal recycling industry.
1. Recruiting and retaining skilled labour
As part of their hiring strategy, AIM Recycling strategically uses platforms like Indeed, LinkedIn, and Glassdoor to recruit new employees, something that Melanson says has doubled AIM Recycling's reach. Taking charge of recruitment internally through a centralized talent acquisition function has further enhanced the selection process, allowing the company to identify, attract, and hire workers without the need for external agencies. Melanson says that AIM Recycling also incorporates artificial intelligence into its recruitment process, generating tailored behavioural questions, interview guides, and other resources for each specific position.
2. Running public awareness campaigns
Through collaboration with government agencies, industry associations, and educational institutions, AIM Recycling works to enhance public awareness of the benefits of careers in the metal recycling sector. According to Melanson, emphasizing the industry's contribution to sustainability and resource preservation serves as a strategy to attract new talent.
3. Standardizing training across all sites
With the labour shortage making it difficult to find workers with the necessary skills and qualifications for positions in the scrap metal industry, AIM Recycling provides training and development programs for its staff, helping to bridge skills gaps and promote career advancement through cross-training, says Melanson. This approach ensures that employees are prepared to take on various roles seamlessly, promoting operational resilience and flexibility.
Moreover, the company is implementing standardized management training programs across all of its sites, aiming to create a cohesive approach to leadership and management within the organization. As a key part of this initiative, AIM Recycling also creates in-house training manuals and conducts assessments.
"Our company has taken proactive steps to address the challenges of finding qualified candidates by implementing our own training manuals specific to our industry standards," says Melanson. "For example, new hires that will be operating the crane are required to complete an evaluation at the end of their training guaranteeing that they possess the necessary skills and knowledge. By adopting these measures, our company not only maintains a skilled workforce but also contributes to the overall development of industry standards."
4. Focusing on equipment fleets
According to Cooper, AIM Recycling's dedication to asset management has resulted in some of the best equipment life cycles across its entire fleet, helping the company gain a competitive edge within the industry.
5. Integrating environmental responsibility
When it comes to green initiatives, Cooper says AIM Recycling leads by example, integrating environmental responsibility throughout its operations in the form of sustainable practices, emissions reduction, and an overall minimization of its ecological footprint.
As an integral part of this, Cooper highlights that AIM Recycling actively advocates for policies supporting recycling, environmental sustainability, and the circular economy, factors that play a key role in shaping the industry's future.
"Our vision is centred around sustainability, aiming to reduce the environmental impact of metal extraction and processing, while conserving natural resources," says Cooper. "Improving productivity, sorting accuracy, and overall environmental performance requires embracing sophisticated technologies with automation and data analytics. AIM Recycling envisions a future where materials are continuously recycled and reused, thereby reducing waste and minimizing the need for primary resource extraction."
6. Embracing new recycling practices
When it comes to its day-to-day operations, Cooper says AIM Recycling actively pursues new recycling techniques, seeks to improve material recovery rates, and explores innovative methods for recycling and recovering valuable materials from sources such as electronic waste, industrial machinery, and automotive parts.
"By continuously seeking new methods for recycling and recovery, AIM Recycling positions itself as an industry pioneer, attracting employees who are passionate about environmental sustainability and innovation," says Cooper.
7. Fostering relationships in local communities
By engaging with local communities, providing educational programs, and supporting initiatives that promote recycling and environmental awareness, AIM Recycling has been able to foster positive relationships in the areas it operates in, says Cooper.
"We're dedicated to helping with the development of new programs, mentorship opportunities, and extra fundraising initiatives while investing in the communities we are a part of and supporting regional and national organizations and causes," says Cooper. "In the last five years alone, AIM has donated over $15 million to the communities it serves, focusing on healthcare and education, as well as children and youth."
Cooper also notes that the expansion of recycling facilities generates positive effects for surrounding communities by creating job opportunities in operations, maintenance, administration, and management. The increased economic activity associated with expansion, including relationships with suppliers and local spending by employees, can also play a role in stimulating the local economy.
8. Prioritizing employee well-being
Recognizing the importance of employee well-being in today's job market, Melanson says AIM Recycling offers competitive salaries and benefits packages, paid time off, and a Years of Service program that recognizes and rewards employees.
Beyond monetary incentives, the company is actively developing a collection of initiatives intended to increase employee satisfaction, well-being, and recognition, which in turn increases productivity and employee engagement.
"Our commitment to employee well-being is prevalent throughout our history. As one of the first metal recyclers globally to bring our operations indoors and into a heated warehouse, we were invested in providing a comfortable and safe working environment, further demonstrating our dedication to the health and comfort of our workforce, while setting us apart from competitors," says Cooper.