How machine monitoring systems can help you better manage your material handler
Telematics deliver real-time data to help you make smarter equipment decisions
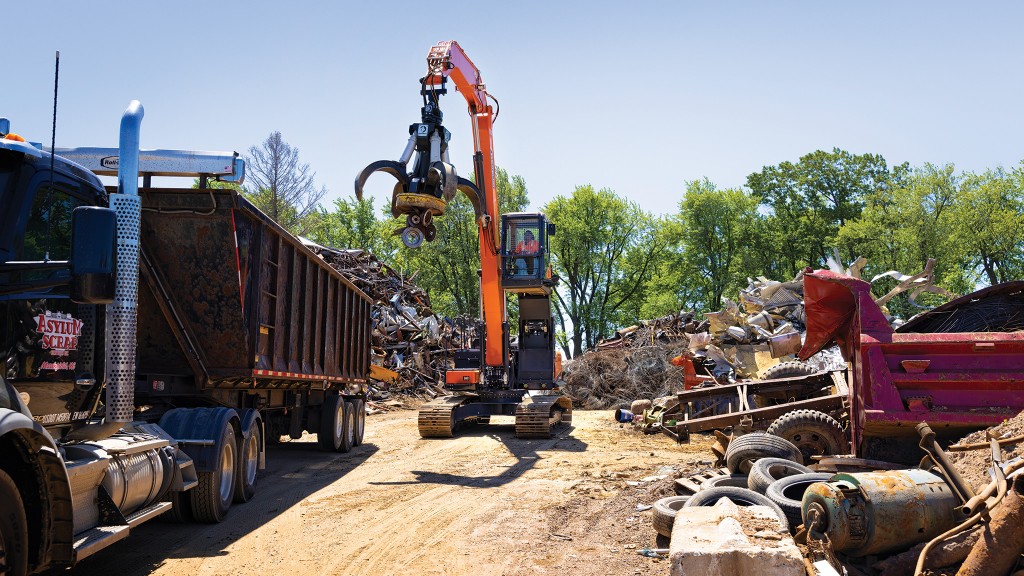
Material handlers, along with other pieces of recycling equipment, spend their days lifting, carrying, and moving a variety of materials in waste and scrap handling applications. They work long hours and spend most of their life on the same site.
To help keep machines functioning at their best, recycling operations can use technological advancements such as telematics machine monitoring services. Telematics goes beyond basic fleet location tracking and delivers a stream of real-time data to a computer or smartphone to help you make smarter equipment decisions. Telematics services can enhance safety and help your material-handling business run more efficiently.
Stojan Arezina, telematics manager at DEVELON, explains how telematics works and how it can help you better manage your material handler.
Understanding how telematics work
Many of today's material handlers come standard with telematics to collect data. The system can help you understand how, when, and where recycling equipment is working. The location is provided in longitude and latitude, and the mapping software automatically changes to the closest address.
"Many fleet tracking technologies use a terminal that is installed on equipment to gather and communicate data wirelessly via cellular or satellite service," says Arezina. "The data is sent to a website where the machine's performance, operating hours, fuel usage, engine idle time, and work time can be monitored. Engine and hydraulic oil temperature and fault and warning codes can be viewed via a computer or cellular device."
Your local equipment dealer will also have access to the machine reports. Their service department can identify upcoming machine maintenance and contact you to schedule a day and time to perform the service, minimizing any schedule disruptions.
Taylor Long, telematics coordinator for Swiderski Equipment, oversees more than 200 pieces of equipment at the Wisconsin dealership. He works closely with service managers, and customers like Asylum Scrap Services, to give them the telematics data they need to run their operations efficiently.
"At the control centre, I'm logged in as an admin, so I can see all of the machines at once," says Long. "If a customer has an issue, I can already see what the customer is seeing and can reach out to the service manager. It's a big benefit to the customer because we know exactly what parts they need in real time."
Another benefit is the data produced by the telematics system: specifically the fault codes, service monitoring and warnings, fuel usage, and daily reports.
"Each of our customers' machines needs to keep moving," says Long. "That's why telematics data - especially fault codes, warnings, service reminders, and daily reports - is so important. Our customers need to keep loading to improve their profit and uptime support. We know exactly when something's going on so we can go there and solve it."
The benefits of telematics monitoring services
Telematics can help you and your scrap and recycling business in multiple ways. Here are a few important ones to note.
Improve operator behaviour A scrapyard is a congested place, so it's critical to follow proper operating practices to ensure job site safety.
"Using data collected through telematics systems, you can improve operator performance," says Arezina. "It can help reduce improper use of equipment on the job site like hard braking, accelerating, and speeding. Telematics can also help reduce prolonged idle time. By monitoring this data, you can correct these issues to promote a more productive and safer job site."
You can also identify ways of reducing operating costs to extend component life cycles. This can help decrease the frequency of unplanned maintenance.
Save on downtime
Your dealership may be able to diagnose a problem without physically being in the same location as the machine, speeding up response time.
"This will help save unnecessary machine downtime and reduce travel time for your dealership's service department," says Long. "When a technician does need to visit your job site, they will be better prepared to fix your issue because of telematics data shared with the dealership."
Improve fuel efficiency
Telematics data can help you improve material handler fuel usage and efficiency.
"A lot of our customers are dialed into their fuel usage and uptime," says Long. "That's the great thing about telematics. It's here to make things more efficient and be a partner on the job to support them with whatever they need."
The system monitors equipment idle time, helping you identify machines that are working under or over capacity. Reducing idle times can extend engine life and reduce repair and maintenance costs. And you can monitor power mode operation and adjust the power mode to do the same work while using less fuel.
Help prevent unauthorized operation
Keep a close eye on your machine and see where it has been operated. A geofence or an invisible/virtual boundary can be created through the machine's GPS system. It will send a notification and can alert the authorities about possible equipment theft if your machine leaves the virtual fence. A time fence or curfew on each machine can also be created.
"If the machine is operated outside of working hours, an email or SMS text notification can be sent to you," says Arezina. "This helps prevent unauthorized operation and potential vandalism to the machine and job site."
Allison Grettenberg is a strategic communications specialist at Two Rivers Marketing.