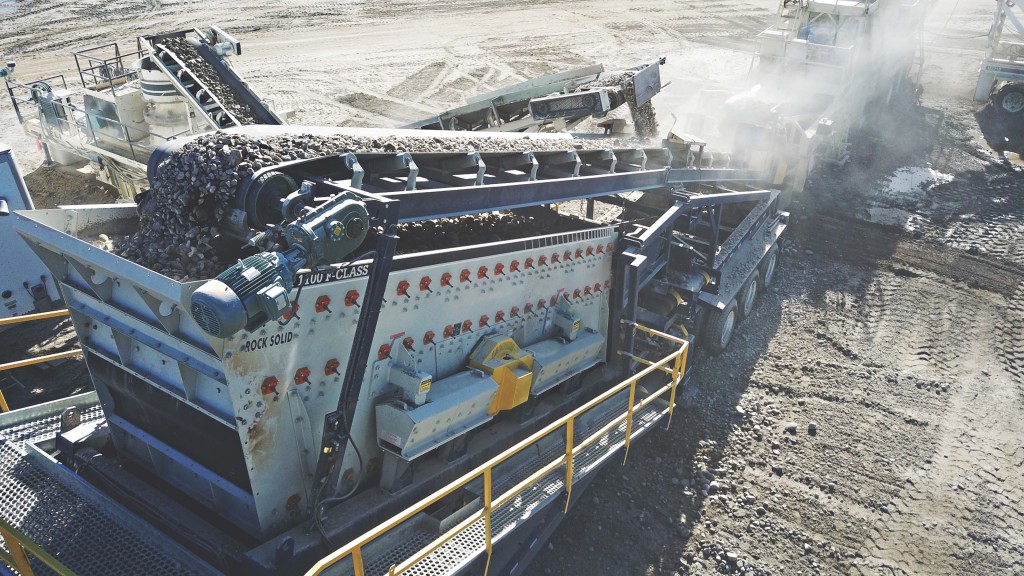
A producer's job never ends. In addition to managing the mine, it's the producer's responsibility to keep all equipment in proper working order. To do so, they use different programs and services to increase equipment productivity and extend its lifecycle because implementing innovative technology and tools can help minimize downtime and increase ROI.
Four steps to get the most out of equipment and increase ROI
A vibration analysis system
Look for a vibration analysis system designed specifically for vibrating screens. This offers mining operations a way to safely monitor performance in real time. The vibration analysis system should have eight triaxial sensors, which attach to key places on the equipment. From there, the sensors transmit 24 channels of data to a heavy-duty tablet, which then illustrates the machine's orbit, acceleration, and deviations. An advanced vibration analysis system transfers data wirelessly to a certified engineering team, which evaluates the machine's performance, alerts the user to any issues, and suggests recommendations for improvement.
Partner with a manufacturer
Partner with a manufacturer to ensure heightened equipment functionality through programs such as screen installation, commissioning, and operator training. Although producers might take the time to perform preventative maintenance themselves, larger problems can occur and cause extended downtime if it's not done correctly. That's where a manufacturer comes in. A thorough, trained technician should walk through a detailed checklist to evaluate screening equipment, train personnel on proper operation and screen installation, and work with the producer to develop a preventative maintenance plan.
Work with a screen media expert
Take the guesswork out of installation by working closely with a screen media expert. Even with the best maintenance plans, issues occur if screen media isn't properly selected and installed. Sometimes producers struggle with blinding as clay-heavy materials clog the screen openings, or pegging, where near-sized stones get trapped in screen media openings. Working with a manufacturer proficient in screen media takes the guesswork out of screen selection and installation as well as ensures the extended life of the screen.
Utilize trained technicians
Optimize production with trained technicians. Some manufacturers include programs – such as onsite maintenance, screen installation, training, and analysis of operational safety and performance – in a single plan. These programs might even offer complete machine refurbishment, machine monitoring, and servicing, as well as related services to maximize uptime.
Maintaining equipment increases the longevity and efficiency of machines. And, as with any business, profits are the key measure of success. A good maintenance program focused on preventing downtime pulls together vibration analysis, proper screen selection, and installation, as well as implementing in-house training and preventative maintenance schedules. Also, partnering with the right manufacturer ensures peak equipment performance and reliability for years to come.
Karen Thompson is the president of Haver & Boecker Niagara's Canada location.
Company info
225 Ontario St.
St. Catharines, ON
CA, L2R 7B6
Website:
haverniagara.com
Phone number:
1-905-688-2644