Redwood Materials to supply Panasonic's Kansas battery production facility with cathode material
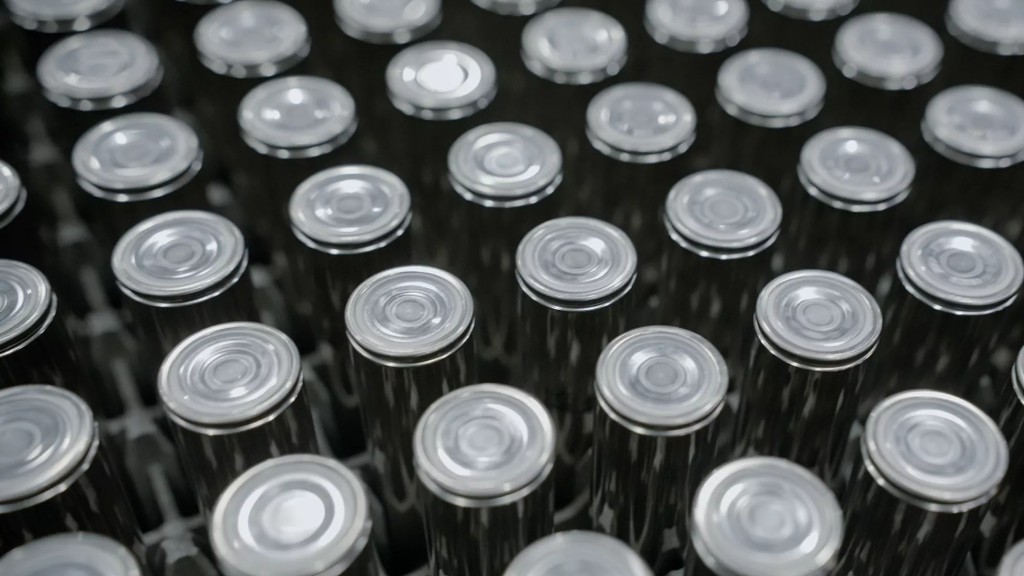
Panasonic will source Redwood's cathode material for battery cell production in Panasonic's new Kansas plant, targeted to come online in 2025.
In the next decade, global demand for lithium-ion batteries is projected to grow by more than 500 percent as more climate-change-combatting products are created. A key component for all batteries is cathode material, which accounts for over half the cost of a battery cell. The cathode cost is significant because it contains all of the critical metals – lithium, nickel, and cobalt – in the battery and has a complex manufacturing process and functional specification that is integral to the performance and safety of an electric vehicle battery.
With the battery cell manufacturing landscape in North America expanding each day to meet the increasing demand, vast quantities of cathode material are necessary to supply the EV industry. However, there is currently no cathode production at scale in North America.
Redwood aims to fix that issue. Redwood plans to build and expand the production of battery components, anode, and cathode, in the U.S. and produce them from an increasing amount of recycled content. The company will make investments in the U.S., and will scale the technology and facilities over the next few years to bring cathode online and ramp production to 100 GWh, enough for 1 million EVs by 2025. By 2030 Redwood expects production of both anode and cathode to scale to 500 GWh/year of materials, enough to power five million electric vehicles.
Panasonic will source Redwood's cathode material for battery cell production in Panasonic's new Kansas plant, targeted to come online in 2025.
Redwood's partnership with Panasonic Energy of North America first began in 2019 and since then the cell production scrap from the factory in Nevada (in which Panasonic is the battery cell manufacturer) has been recycled by Redwood. Panasonic will also be the first long-term buyer of Redwood's anode copper foil, another essential component in lithium-ion battery production. With both anode and cathode components created from recycled materials, Redwood and Panasonic are establishing a closed-loop for domestic cell production.
Cathode is produced via a convoluted supply chain. Whether metals are newly mined or recycled in the U.S., the existing supply chain and lagging infrastructure require that these minerals travel outside the United States where the majority of existing infrastructure and manufacturing expertise exists. Domestic cell production has tolerated a 50,000+ mile supply chain for cathode before it ever reaches a battery cell factory in the United States, but this is far from sustainable. To keep pace with domestic electrification plans and mounting EV demand, the U.S. would need to import greater than 2,000,000 MT of cathode through the year 2030, allowing a lost economic value of greater than $100 billion USD.
Redwood will supply U.S. battery cell manufacturers with battery materials produced domestically. Quickly ramping up a domestic battery materials supply chain and using the highest possible percent of local, recycled raw materials is the best way Redwood can help meet the U.S.' 2030 goal of 50 percent EV sales.