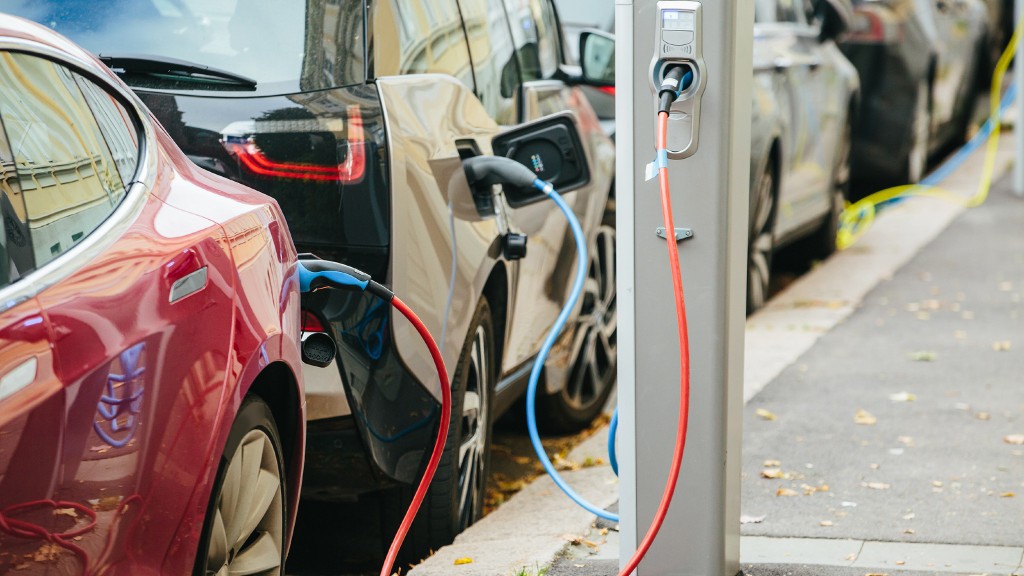
Electra Battery Materials Corporation has started commissioning its black mass recycling demonstration plant at its battery materials park located north of Toronto following the successful installation of material feed handling and lime delivery systems, two key circuits in Electra's hydrometallurgical process designed to recycle end-of-life lithium-ion battery materials.
"Automakers are looking for a closed-loop supply chain for their batteries and Electra's recycling process presents a compelling solution to move to a circular model for recycling end-of-life batteries and battery manufacturing scrap," says Trent Mell, CEO of Electra Battery Materials. "Consistent with our strategy, integrating battery materials recycling to our cobalt sulphate production activities at our refinery will not only serve as an important differentiator but will allow us to generate incremental cash flow while strengthening our relationships with various stakeholders that make up the North American EV supply chain.
"Pending completion of the demonstration plant and a review of project economics, success could pave the way towards the buildout of a 5,000 tonne per annum black mass processing facility within our battery materials park in Ontario using existing infrastructure, personnel, and lab facility. Additional capacity would be added through construction of additional modules as the market for recycled battery material expands."
Electra is currently retrofitting its existing cobalt sulphate refinery located in Temiskaming Shores, Ontario, to accommodate its proprietary hydrometallurgical process designed to treat black mass, a byproduct generated from the recycling of end-of-life EV and other lithium-ion batteries.
Under the parameters of the black mass demonstration, Electra plans to process up to 75 tonnes of material in a batch mode. Using its lab-tested process, Electra anticipates the recovery of high-value elements found in lithium-ion batteries, including nickel, cobalt, lithium, manganese, copper, and graphite.
Electra also anticipates the full commissioning of all equipment and circuits of the black mass recycling demonstration in the fall of 2022 with the full commissioning of the cobalt sulphate refinery expected in the spring of 2023. The company will provide regular updates on the status of its demonstration plant and commissioning efforts.
In preparation for the black mass demonstration plant, Electra completed process development and engineering on recycling black mass material. Electra previously sourced black mass samples from suppliers in North America, Europe, and Asia, studied the feed characteristics, and developed a hydrometallurgical process route to recover contained lithium, nickel, cobalt, copper, and graphite. The test work was conducted using the facilities of SGS Labs in Lakefield, Ontario, and engineering was completed using the combined resources of Electra technical personnel, supported by process design engineers of Hatch Associates and mechanical and electrical engineering support by Bestech.
Electra's proprietary hydrometallurgical process has a low carbon footprint and produces stable non-acid generating tailings, thereby reducing environmental impacts while meeting or exceeding water discharge effluent criteria as stipulated by both federal and provincial regulations.
Electra completed a benchmarking study that indicates that the carbon intensity of the cradle-to-gate battery grade nickel sulphate produced from the recycled black mass using its hydrometallurgical process in a low-carbon electricity grid is lower than other feed options, including Class 1 nickel metal, nickel mixed hydroxide precipitate, or ferronickel.
In addition, the carbon intensity of nickel sulphate produced from recycled black mass at Electra's refinery, which uses hydroelectricity as its primary energy source, is less than 50 percent of the carbon intensity of nickel sulphate produced from mixed hydroxide precipitate when the source of energy relies on non-renewables such as coal-powered electricity. The refinery's primary power source is hydroelectric from Ontario Power Generation, resulting in nearly zero greenhouse gas emissions.
Company info
Bay Adelaide Centre
333 Bay Street, Suite 2400, P.O. Box 20
Toronto, ON
CA, M5H 2T6
Website:
electrabmc.com