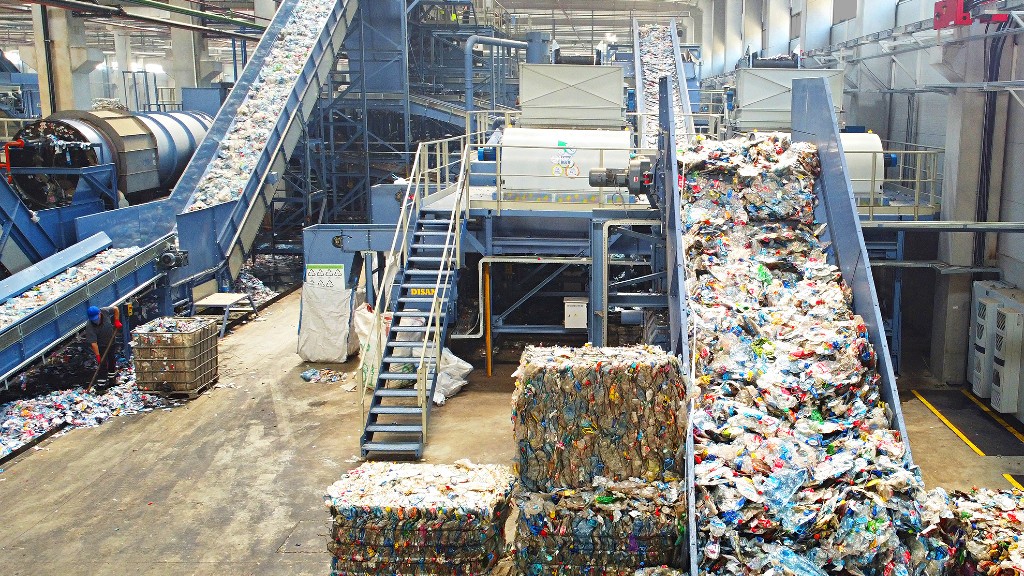
Drawing from its assortment of plastics recycling equipment, Herbold can custom configure wash plants for polyolefins capable of producing food grade recyclates.
While each wash plant is designed around the user's specific requirements and facility characteristics, all feature a multi-stage process usually consisting of pre-shredding, pre-washing and initial separation, granulation, high-density separation, and drying.
Pre-shredding is typically done in a single-shaft shredder such as the Herbold 60/120. With a 23.5-inch diameter rotor and 60 individual knives, these machines can accept bales of contaminated waste and process up to 13,000-pounds per hour.
Washing takes place in a VWE-60 pre-washing unit which employs a three-step process of sink and swims to remove heavy materials, intensive spray wash to loosen and remove embedded sediment and an additional sink and swim to further eliminate remaining sediment.
Further size reduction takes place in a wet granulator such as the Herbold 80/120. The wet operation provides additional separation of particles and contaminants from materials.
Additional high-density separation of contaminants and recyclate occurs in a Hydrocyclone. The centrifugal force of the Hydrocylcone provides separation that exceeds conventional methods by a factor of 15, ensuring the level of purity necessary for food grade recyclate.
After final separation, materials are conveyed to either a mechanical or thermal dryer for removal of residual moisture prior to use or storage.