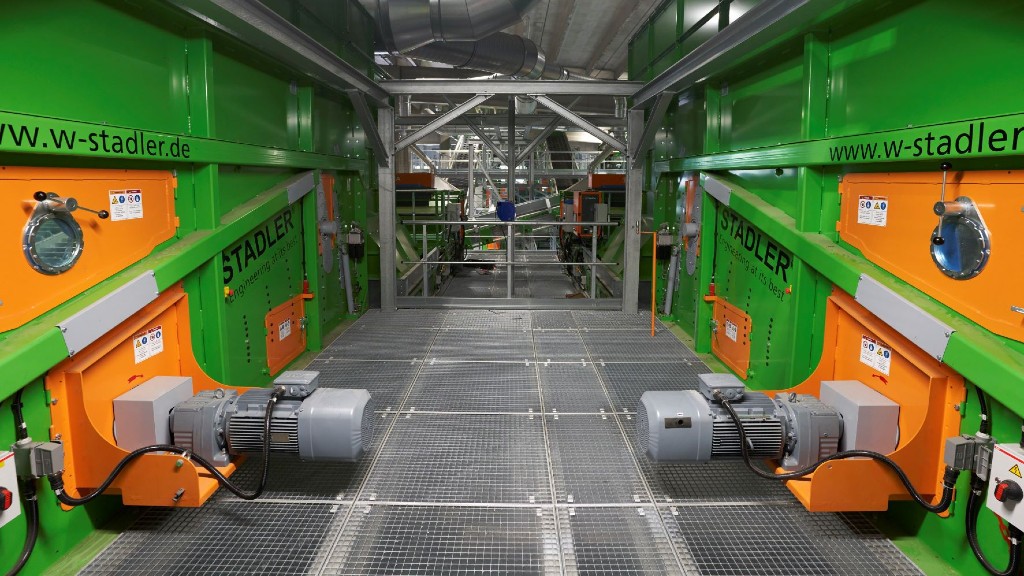
The construction industry is by far the biggest generator of waste in the European Union - about 870 million tons in 2017 - which accounts for 30 percent to 40 percent of the total waste generation in industrialized countries. In spite of the high volumes of generated C&D waste, its recycling rates vary enormously in different countries around the world: while countries including the Netherlands, Ireland, and Hungary reported recovery rates of 99 percent to 100 percent from 2017 to 2018, the figures for other nations ranged from 0 percent to 69 percent. In all cases most of the recovered materials are downcycled - mainly used for backfilling in road construction, building foundations or embankments - or sent to landfill. This means that the recovered materials do not replace or significantly reduce the use of raw materials in the production process, hindering an effective circular economy.
The potential of C&D waste
"This represents a huge untapped potential," says Dr. Juan Carlos Hernández Parrodi, Senior Project Manager, Research & Development at STADLER. "Typically, CDW [C&D waste] is made up of concrete, wood, metals, glass, masonry rubble, stones, soil, sand, gypsum, plasterboard, asphalt, plastics, insulation, paper, cardboard, and salvaged building components. There is very little that can't be recycled - the recycling potential of this waste can be higher than 90 percent."
Recovered materials from C&D waste can be recycled in a variety of applications. For example, today less than 5 percent of recovered aggregates are used in the production of new concrete. However, recovered aggregates are said to be suitable for the substitution of 10 percent to 20 percent of virgin aggregates for many concrete applications, which range from pipe bedding to concrete and block construction.
"In fact, some previous studies have pointed out that, if appropriately processed to remove moisture and impurities, recovered aggregates can even have advantages over raw materials in some cases, such as higher compressive strength and a wider range of applications in the construction industry," explains Hernández Parrodi."
The demand for advanced recovery plants is set to increase quickly
The effective management of C&D waste is becoming an increasingly urgent issue. As natural resources are depleted and the demand from the construction industry continues to grow, recycling C&D waste to replace raw materials is fast turning into a necessity.
"Even if we were to recycle 100 percent of the generated CDW, we would not be able to meet the current demand of construction materials," says Hernández Parrodi.
Awareness among governments, environmental organizations, educational institutions, and the general public is growing. The gradual implementation of ordinances and directives in the EU and around the world is diverting increasingly significant amounts of C&D waste from landfills toward recycling and material recovery plants.
"This evolution is accelerating," says Hernández Parrodi. "Legislation regulating the amounts of CDW that can be disposed of in landfill is increasingly restrictive and aims to promote the recovery of secondary materials and recycling. At the same time, new regulations are setting high standards for recycled construction materials, encouraging a shift from downcycling to recycling and upcycling. All these factors are driving a fast growth in the demand for technology innovation and facilities capable of recovering high-quality materials from CDW."
The development of the C&D waste recycling industry
The effective sorting of C&D waste is key to achieving the high-quality levels required for successful recycling and upcycling in a broad range of construction applications. The composition of this type of waste and the requirements for the targeted output fractions varies significantly from country to country, and sometimes even at a regional level.
"Similarly to other waste streams, such as municipal solid waste or packaging waste, there is no standard recipe for processing CDW," explains Hernández Parrodi.
STADLER is able to bring its extensive experience in the design of advanced sorting plants to the construction sector, developing tailored solutions to match the individual situation.
C&D waste sorting processes need to be flexible, robust and capable of handling high throughputs with considerable fluctuations. STADLER's machines perfectly fit the bill. They are conceived to process large amounts of mixtures of diverse materials in very challenging conditions, such as the presence of fines and humidity, as well as heavy and bulky objects. For example, the STADLER ballistic separator STT6000, chain conveyor belt and trommel screen are heavy-duty machines that can withstand the wear and tear associated with processing and recycling C&D waste, while delivering effective and efficient sorting.
STADLER has applied its waste sorting know-how in a number of C&D waste projects - the most recent ones for Sogetri in Switzerland and Remeo Oy in Finland. The latter is a facility that combines a C&D waste plant capable of processing 30 t/h and a C&I plant with 15 t/h capacity, featuring state-of-the-art Artificial Intelligence (AI) technology from partner ZenRobotics, cutting-edge processes and a high level of automation. Mauri Lielahti, Business Director, Processing at Remeo was impressed with STADLER's tailored approach to the project and ingenuity:
"We appreciated STADLER's capability to be innovative, their willingness to seek new solutions and that they were ready to listen to the customer's needs."
STADLER's sorting plants enable the separation of C&D waste into different fractions, which can have a broad range of applications. They can substitute raw construction materials such as sand, gravel, metal, wood, and many more. Recovered concrete can be used to produce recycled concrete. Recovered fractions from C&D waste can also be utilized to innovate and produce new materials, such as inorganic polymers and glass ceramics.
"This means that with recovery not only is it possible to close the loop in material life cycles and move towards a circular economy," concludes Hernández Parrodi, "but it also enables upcycling, consequently expanding the applications and increasing the added value of recovered materials."